20 ton chiller
A 20 – ton chiller is a powerful cooling system used in various applications to remove heat from a space or process. The “20 – ton” rating is a measure of its cooling capacity. Specifically, it means that the chiller can remove heat at a rate equivalent to melting 20 tons of ice in a 24 – hour period. This amount of cooling capacity is substantial and is suitable for a range of medium – sized to some larger – scale applications.
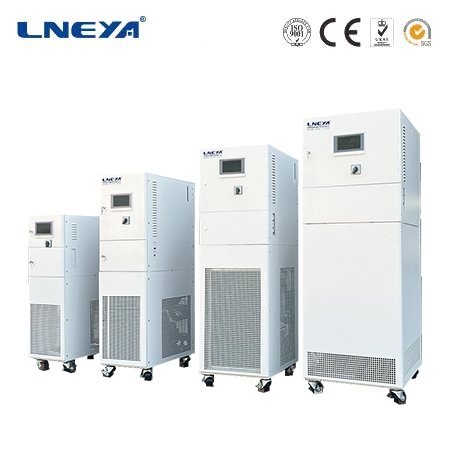
Understanding the Cooling Capacity of a 20 – Ton Chiller
Conversion to Standard Units
In the metric system, 1 ton of refrigeration is approximately equal to 3.517 kilowatts (kW). So, a 20 – ton chiller has a cooling capacity of around 20 x 3.517 = 70.34 kW. This conversion helps in comparing the chiller’s capacity with other cooling equipment and in understanding its energy requirements.
In British Thermal Units per hour (BTU/h), 1 ton of refrigeration is equivalent to 12,000 BTU/h. Thus, a 20 – ton chiller can remove 20 x 12,000 = 240,000 BTU/h of heat. These units are often used in the United States and in some international standards related to HVAC (Heating, Ventilation, and Air Conditioning) systems.
Implications for Cooling Applications
The 20 – ton capacity is sufficient to cool a medium – sized commercial building, such as a multi – story office building with a floor area of approximately 10,000 – 20,000 square feet, depending on factors like insulation, internal heat gains from equipment and occupants, and climate conditions. In an industrial setting, it can be used to cool specific processes, such as in a medium – sized food processing plant where certain production lines require precise temperature control.
Types of 20 – Ton Chillers
Air – Cooled 20 – Ton Chillers
Construction and Operation
Air – cooled 20 – ton chillers use ambient air to dissipate heat from the refrigerant. They typically consist of a compressor, a condenser with finned tubes, and an evaporator. The compressor pressurizes the refrigerant, and the hot, high – pressure refrigerant vapor then enters the condenser. In the condenser, ambient air is blown over the finned tubes by fans. As the air passes over the tubes, heat is transferred from the refrigerant to the air, causing the refrigerant to condense. The condensed refrigerant then passes through an expansion device and into the evaporator, where it absorbs heat from the process fluid (usually water) that needs to be cooled.
Advantages
Simplicity: They are relatively simple in design as they do not require a complex water – cooling system. This makes them easier to install, especially in locations where access to a water source is limited.
Lower Initial Cost: Generally, air – cooled 20 – ton chillers have a lower upfront cost compared to water – cooled models. This is because they do not need components such as a cooling tower, water pumps, and extensive plumbing.
Disadvantages
Limited Efficiency in High Temperatures: Their cooling efficiency can be significantly reduced in hot climates. When the ambient air temperature is high, the temperature difference between the refrigerant and the air is smaller, resulting in less effective heat transfer. This can lead to increased energy consumption as the compressor has to work harder to maintain the desired cooling effect.
Higher Noise Levels: The operation of the fans in air – cooled chillers can generate more noise compared to water – cooled chillers. This may be a concern in applications where noise restrictions are in place, such as in some commercial or residential areas.
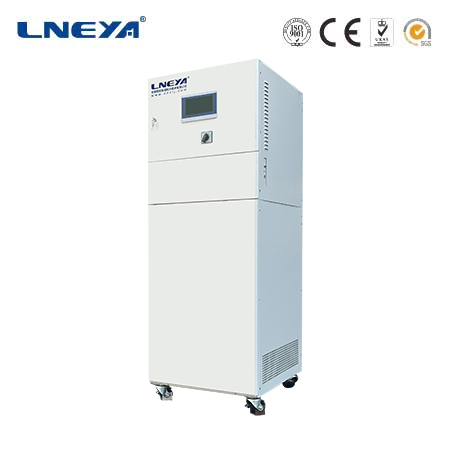
Water – Cooled 20 – Ton Chillers
Construction and Operation
Water – cooled 20 – ton chillers use water as a heat – transfer medium between the refrigerant and the environment. They typically include a compressor, a shell – and – tube or plate – type condenser, an expansion device, and an evaporator. The compressor raises the pressure and temperature of the refrigerant. The hot refrigerant vapor then enters the condenser, where it transfers heat to the water flowing through the condenser. The warm water leaving the condenser is usually sent to a cooling tower, where heat is dissipated to the atmosphere through evaporation and sensible heat transfer. The cooled water then returns to the condenser to continue the heat – transfer process. The refrigerant, after condensing, passes through the expansion device and into the evaporator to absorb heat from the process fluid.
Advantages
Higher Energy Efficiency: Water – cooled chillers are generally more energy – efficient than air – cooled ones. Water has a higher heat – carrying capacity than air, allowing for more effective heat transfer. In large – scale applications or in regions with high ambient temperatures, the energy savings can be substantial over time.
Quieter Operation: Since they do not rely on large fans to dissipate heat, water – cooled 20 – ton chillers tend to operate more quietly, making them suitable for applications where noise is a concern, such as in hospitals or high – end office buildings.
Disadvantages
Higher Initial Cost: The cost of a water – cooled 20 – ton chiller, including the chiller unit, cooling tower, water pumps, and plumbing, is typically higher than that of an air – cooled chiller. The need for a reliable water source and the installation of a cooling tower add to the overall expense.
Complexity and Maintenance Requirements: Water – cooled systems are more complex and require regular maintenance. The water in the system needs to be treated to prevent corrosion, scale formation, and biological growth. Additionally, the cooling tower requires regular inspection and cleaning to ensure proper operation.
Applications of 20 – Ton Chillers
Commercial Applications
Office Buildings: In medium – sized office buildings, a 20 – ton chiller can effectively cool the interior space. It can handle the heat generated by office equipment, lighting, and occupants. The chiller can be integrated into a central HVAC system, providing cool air to different floors and rooms. For example, in a 5 – story office building with open – plan work areas and a few meeting rooms, a 20 – ton chiller can maintain a comfortable temperature throughout the building, improving the productivity and comfort of the employees.
Retail Stores: Many medium – sized retail stores, such as supermarkets or department stores, use 20 – ton chillers to cool the sales floor and storage areas. The chiller helps in maintaining a comfortable environment for customers and also keeps perishable goods at the right temperature in the store’s refrigerated sections. In a supermarket, the chiller can supply chilled water to air – handling units that cool the main sales area, as well as to the refrigeration systems for the display cases.
Industrial Applications
Food and Beverage Industry: In the food and beverage industry, 20 – ton chillers are used in various processes. For instance, in a medium – sized bakery, the chiller can be used to cool the dough during the mixing and proofing stages, ensuring consistent quality of the baked products. In a beverage production plant, it can cool the product during bottling or canning processes to prevent spoilage and maintain the desired taste. The chiller can also be used to cool the water used for cleaning equipment in the plant.
Pharmaceutical Industry: In pharmaceutical manufacturing, precise temperature control is crucial. A 20 – ton chiller can be used to cool the production areas, storage facilities for raw materials and finished products, and laboratory spaces. It helps in maintaining the stability of pharmaceutical products and ensuring compliance with strict quality and safety regulations. For example, in a pharmaceutical research laboratory, the chiller can provide cooled water to equipment such as centrifuges and incubators that require specific temperature conditions.
Installation and Maintenance of 20 – Ton Chillers
Installation Considerations
Space Requirements: Both air – cooled and water – cooled 20 – ton chillers require sufficient space for installation. Air – cooled chillers need enough clearance around the unit for proper air circulation. The fans should be able to draw in fresh air and exhaust the heated air without obstruction. Water – cooled chillers, in addition to the chiller unit, need space for the cooling tower. The cooling tower should be installed in a location that allows for proper water drainage and ventilation.
Electrical and Plumbing Requirements: For electrical connections, a 20 – ton chiller typically requires a dedicated electrical circuit with the appropriate voltage and amperage capacity. The electrical wiring should be installed by a qualified electrician following local electrical codes. In the case of water – cooled chillers, proper plumbing connections for the water supply and drainage are essential. The water supply should have the correct pressure and flow rate to ensure efficient operation of the chiller and the cooling tower.
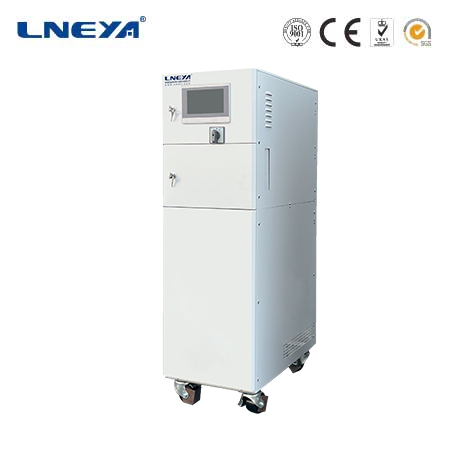
Maintenance Requirements
Regular Inspections: Regular inspections are essential for both types of 20 – ton chillers. In air – cooled chillers, the condenser fins should be inspected for dirt, debris, or damage. Dirty fins can reduce the heat – transfer efficiency of the condenser. The fans and their motors should also be checked for proper operation. In water – cooled chillers, the condenser tubes should be inspected for scale formation, corrosion, or leaks. The cooling tower should be inspected for proper water distribution, the condition of the fill material, and the operation of the fans.
Refrigerant Management: The refrigerant charge in a 20 – ton chiller needs to be monitored regularly. Leaks in the refrigerant system should be detected and repaired promptly. The quality of the refrigerant should also be checked, and any contaminants should be removed. In addition, the compressor oil level and quality should be maintained according to the manufacturer’s recommendations.
Control System Maintenance: The control system of the 20 – ton chiller, which includes temperature sensors, pressure sensors, and controllers, should be calibrated regularly. The sensors need to provide accurate readings to ensure proper operation of the chiller. Any software updates for the control system should be installed to improve performance and functionality.
Comparison with Other Capacity Chillers
Smaller Capacity Chillers
Differences in Applications: Smaller capacity chillers, say 5 – ton or 10 – ton chillers, are more suitable for smaller spaces. For example, a 5 – ton chiller may be used in a small office suite or a single – family home. They are also used in some small – scale industrial processes where the heat load is relatively low. In contrast, a 20 – ton chiller is designed for larger areas or more demanding industrial applications.
Energy Consumption and Cost: Smaller capacity chillers generally consume less energy as they have a lower cooling capacity. Their initial cost is also lower. However, for larger spaces, using multiple smaller capacity chillers may not be as efficient as using a single 20 – ton chiller in terms of energy consumption and overall cost, as there may be additional inefficiencies associated with multiple units and their control systems.
Larger Capacity Chillers
Applications and Performance: Larger capacity chillers, such as 50 – ton or 100 – ton chillers, are used in large – scale commercial buildings like shopping malls, hospitals, or large – scale industrial plants. These chillers can handle much higher heat loads. While a 20 – ton chiller is suitable for medium – sized applications, larger capacity chillers are designed for spaces with significantly greater cooling requirements. In terms of performance, larger capacity chillers may offer better part – load efficiency in some cases, as they can be equipped with more advanced control systems to adjust the cooling output according to the load.
Cost and Complexity: Larger capacity chillers are more expensive to purchase, install, and maintain. They require more powerful components, larger heat exchangers, and more complex control systems. The installation of a large – capacity chiller also involves more significant space requirements and higher electrical and plumbing demands compared to a 20 – ton chiller.
Conclusion
A 20 – ton chiller is a versatile cooling system with a wide range of applications in commercial and industrial settings. Understanding its cooling capacity, different types, applications, installation and maintenance requirements, as well as how it compares to other capacity chillers, is essential for making informed decisions when choosing a cooling solution. Whether it’s for cooling a medium – sized office building or a specific industrial process, a 20 – ton chiller can provide reliable and efficient cooling, but careful consideration of all these factors is necessary to ensure optimal performance and cost – effectiveness.
Related recommendations
low pressure chiller
21Low Pressure Chillers: A Comprehensive Guide Introduction Low pressure chillers play a crucial role in modern cooling applications. They are designed to provide efficient cooling solutions...
View detailshigh temp controller
209High Temp Controller: Regulating Extreme Temperatures in Industrial Processes Introduction High temp controllers are specialized temperature control devices engineered to operate and maintai...
View detailstexas chillers
217Understanding Texas Chillers Texas chillers encompass a range of cooling systems designed to meet the demands of various industries operating in the state of Texas. These industries may include...
View detailsWhat is the reason for the high low pressure value of the low temp chiller?
736What is the reason for the high low pressure value of the low temp chiller? In the application of industrial refrigeration, low-temperature coolers are used in conjunction with producti...
View details
HelloPlease log in