adiabatic chillers
Adiabatic Chillers: A Deep Dive
Introduction
In the pursuit of more energy – efficient and sustainable cooling solutions, adiabatic chillers have emerged as a promising technology. They offer an alternative approach to traditional chiller systems, aiming to optimize the cooling process while minimizing energy consumption and environmental impact. Adiabatic chillers are designed to address the growing demand for cooling in various sectors, from commercial buildings to industrial plants, in a more resource – friendly manner.
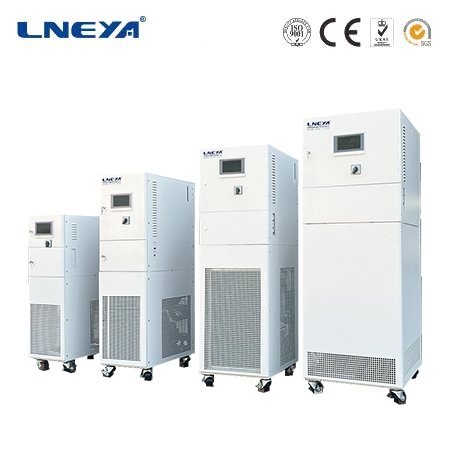
Working Principles of Adiabatic Chillers
Adiabatic Pre – Cooling Process
Water Evaporation for Air Cooling: At the core of an adiabatic chiller’s operation is the adiabatic pre – cooling mechanism. This process starts with water being introduced into the air stream that will eventually enter the condenser. In direct adiabatic chillers, water is sprayed directly into the air flow. As the water droplets evaporate, they absorb heat from the surrounding air. This is an adiabatic process, meaning that the heat for evaporation comes solely from the air itself, without any external heat input or output to the environment other than the latent heat of vaporization of water. The evaporation cools down the air temperature, creating a pre – cooled air stream.
Effect on Refrigerant Cooling: The pre – cooled air then reaches the condenser of the chiller. Since the air entering the condenser is cooler, it can more effectively extract heat from the refrigerant. In a standard air – cooled chiller, the warm ambient air may not be as efficient in cooling the refrigerant, especially in hot and dry climates. But with adiabatic pre – cooling, the lower – temperature air improves the heat – transfer efficiency in the condenser. As a result, the refrigerant can be cooled more effectively, reducing the work required by the compressor to maintain the desired cooling effect. This leads to energy savings as the compressor doesn’t have to work as hard to compress the refrigerant to achieve the necessary heat rejection.
Refrigeration Cycle Integration
Standard Refrigeration Cycle Components: Adiabatic chillers still rely on the fundamental refrigeration cycle, which consists of a compressor, condenser, expansion valve, and evaporator. The compressor increases the pressure and temperature of the refrigerant vapor. The high – pressure, high – temperature refrigerant then moves to the condenser, where it releases heat to the pre – cooled air. After condensation, the liquid refrigerant passes through the expansion valve, which lowers its pressure and temperature. Finally, the low – pressure refrigerant enters the evaporator, where it absorbs heat from the medium being cooled (such as water in a chilled – water system) and evaporates, thus completing the cycle.
Enhanced Performance due to Adiabatic Pre – Cooling: The adiabatic pre – cooling process seamlessly integrates with the standard refrigeration cycle to boost overall performance. By reducing the temperature of the air entering the condenser, the refrigerant can release heat more efficiently. This results in a lower condensing temperature, which in turn decreases the pressure ratio across the compressor. A lower pressure ratio means that the compressor consumes less energy to compress the refrigerant, leading to significant energy savings. For example, in a hot and dry region, an adiabatic chiller can achieve up to 30 – 50% energy savings compared to a traditional air – cooled chiller.
Types of Adiabatic Chillers
Direct Adiabatic Chillers
Water Spray in Air Path: In direct adiabatic chillers, water is directly sprayed into the air stream that is on its way to the condenser. The water is atomized into fine droplets through nozzles placed in the air intake duct. As the warm air passes through these water droplets, the water evaporates due to the heat in the air. This evaporation process cools the air, and the cooled air then proceeds to the condenser. The simplicity of this design makes direct adiabatic chillers relatively easy to install and maintain.
Suitability for Dry Climates: Direct adiabatic chillers are particularly well – suited for dry climates. In arid regions where the ambient air has a low humidity level and a high capacity to absorb water vapor, the evaporation of water occurs rapidly. This leads to a significant drop in the air temperature entering the condenser. For instance, in desert – like areas, direct adiabatic chillers can effectively lower the air temperature by several degrees Celsius, enhancing the chiller’s efficiency. However, in humid climates, the evaporation rate may be limited, and the effectiveness of direct adiabatic cooling may decrease.
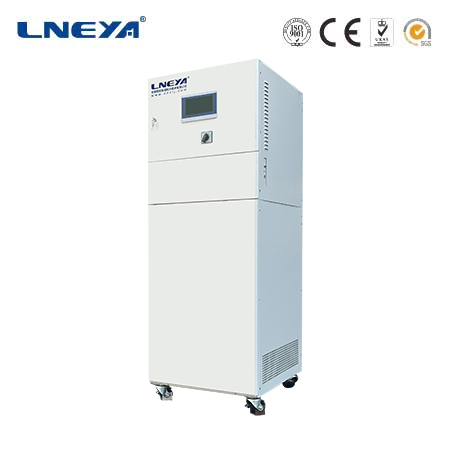
Indirect Adiabatic Chillers
Heat Exchanger – Based Cooling: Indirect adiabatic chillers utilize a heat exchanger to cool the air stream entering the condenser. In this setup, the warm ambient air passes through one side of the heat exchanger. On the other side, a separate water – evaporation process takes place. The heat from the warm air is transferred through the heat exchanger to the water – evaporation chamber. As the water evaporates in this chamber, it cools the air or water on the other side of the heat exchanger, which is then used to cool the air stream going to the condenser. This indirect method ensures that the air being cooled for the condenser does not come into direct contact with the water used for evaporation, which can be beneficial in applications where air quality is a concern.
Versatility in Different Climates: Indirect adiabatic chillers offer greater versatility in terms of climate adaptability. They can be effective in both dry and humid climates. In humid climates, the indirect nature of the cooling process allows for better control over the amount of moisture added to the air. By carefully managing the heat – transfer process in the heat exchanger, the chiller can still achieve a significant reduction in the air temperature entering the condenser. For example, in coastal areas with high humidity, indirect adiabatic chillers can maintain their efficiency by adjusting the heat – exchanger design and the water – evaporation rate.
Applications of Adiabatic Chillers
Commercial Buildings
Office Buildings: In large office buildings, adiabatic chillers can play a crucial role in providing cooling for the occupied spaces. The energy – efficient operation of adiabatic chillers can lead to substantial cost savings on electricity bills. For example, in a multi – story office building in a hot climate, an adiabatic chiller can cool the water used in the building’s HVAC system. The pre – cooled air from the adiabatic process helps in reducing the load on the chiller’s compressor, making the cooling process more efficient. This not only saves energy but also extends the lifespan of the chiller components.
Retail Spaces: Retail spaces, such as shopping malls and department stores, often require large – scale cooling systems. Adiabatic chillers can be installed to cool the vast indoor areas. The ability of adiabatic chillers to adapt to changing cooling loads, especially in areas with variable occupancy like retail spaces, is an advantage. During peak shopping hours, when the cooling demand is high, the adiabatic chiller can operate efficiently to maintain a comfortable temperature for customers and employees. Additionally, the lower operating costs associated with adiabatic chillers can contribute to the overall profitability of the retail business.
Industrial Facilities
Manufacturing Plants: Manufacturing plants often have specific temperature and humidity requirements for their production processes. Adiabatic chillers can be used to cool equipment, control the temperature in production areas, and maintain the quality of products. For example, in a food and beverage manufacturing plant, adiabatic chillers can be used to cool the product during processing and storage. In a plastics manufacturing plant, adiabatic chillers can cool the molds in injection – molding machines, ensuring the proper shaping of plastic parts. The energy – saving features of adiabatic chillers are also attractive for industrial facilities, as they can reduce overall energy costs, which is a significant expense in manufacturing operations.
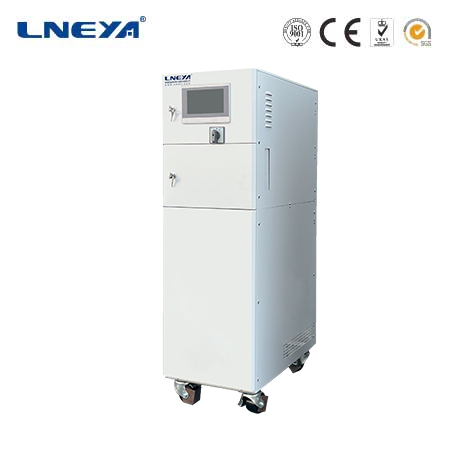
Data Centers: Data centers generate a large amount of heat due to the continuous operation of servers and other electronic equipment. Adiabatic chillers are becoming increasingly popular in data centers. The pre – cooled air from the adiabatic process can be used to cool the air around the servers more effectively. This helps in preventing server overheating, which can lead to hardware failures and data loss. In addition, the energy – efficiency of adiabatic chillers can reduce the high electricity costs associated with running data centers. Some data centers in hot regions have reported significant savings in energy consumption after switching to adiabatic chillers.
Institutional and Healthcare Facilities
Hospitals and Clinics: In the healthcare sector, maintaining the right temperature and humidity levels is crucial for patient well – being and the integrity of medical supplies. Hospitals can use adiabatic chillers to cool operating rooms, intensive care units, and pharmacy storage areas. The energy – efficient operation of adiabatic chillers can also contribute to cost savings in healthcare facilities, which can then be redirected towards patient care. For example, in a large hospital, an adiabatic chiller can provide reliable cooling for the sensitive medical equipment and ensure a comfortable environment for patients and medical staff.
Educational Institutions: Universities and schools can benefit from adiabatic chillers to cool their buildings. In large university campuses, multiple adiabatic chillers can be installed to cool classrooms, libraries, and dormitories. The use of adiabatic chillers not only reduces the environmental impact of the educational institution but also helps in saving on energy costs, which can be used for other educational purposes. For instance, a university can invest the money saved on energy bills in upgrading its educational resources or research facilities.
Advantages of Adiabatic Chillers
Energy Efficiency
Reduced Compressor Work: As mentioned earlier, the adiabatic pre – cooling process in adiabatic chillers reduces the temperature of the air entering the condenser. This leads to a lower condensing temperature and a decreased pressure ratio across the compressor. With a lower pressure ratio, the compressor has to work less to compress the refrigerant. Studies have shown that adiabatic chillers can achieve energy savings of up to 30 – 50% compared to traditional air – cooled chillers, especially in hot and dry climates. This energy efficiency not only benefits the environment by reducing greenhouse gas emissions but also saves money for the users in terms of lower electricity bills.
Optimized Heat Transfer: The pre – cooled air in adiabatic chillers enables more efficient heat transfer in the condenser. The enhanced heat – transfer process ensures that the refrigerant can release heat more effectively, which is essential for the overall cooling performance of the chiller. By improving the heat – transfer efficiency, adiabatic chillers can operate at a higher coefficient of performance (COP), indicating better energy efficiency. For example, the design of the heat – exchanger surfaces in the condenser can be optimized to take full advantage of the pre – cooled air, further enhancing the heat – transfer process.
Cost Savings
Lower Energy Bills: The significant energy savings achieved by adiabatic chillers directly translate into lower energy bills. For commercial and industrial users, this can result in substantial cost savings over the lifespan of the chiller. In addition, the reduced energy consumption can also lead to lower demand charges from utility companies, further reducing operating costs. For example, a large manufacturing plant that switches to adiabatic chillers can save thousands of dollars annually on its energy bills.
Potential for Lower Maintenance Costs: The more efficient operation of adiabatic chillers can also lead to lower maintenance costs. Since the compressor and other components are not working as hard as in traditional chillers, there is less wear and tear. This can reduce the frequency of maintenance and repair requirements, saving both time and money for the owner or operator of the chiller. For instance, the reduced stress on the compressor can extend its lifespan, reducing the need for costly compressor replacements.
Environmental Benefits
Reduced Greenhouse Gas Emissions: The energy – efficient operation of adiabatic chillers means that they consume less electricity. Since most electricity generation in many regions is associated with greenhouse gas emissions, the reduced energy consumption of adiabatic chillers leads to a lower carbon footprint. By using adiabatic chillers, businesses and institutions can contribute to global efforts to reduce greenhouse gas emissions and combat climate change. For example, a data center that switches to adiabatic chillers can significantly reduce its carbon emissions, making it a more environmentally friendly operation.
Water Conservation (in Indirect Adiabatic Chillers): In indirect adiabatic chillers, the water used for the evaporation process is isolated from the air stream being cooled for the condenser. This allows for better water management and potential water conservation. In areas where water resources are scarce, the ability to use water more efficiently in the cooling process is an important environmental benefit. For example, in a region facing water shortages, an industrial facility using indirect adiabatic chillers can reduce its water consumption compared to traditional water – cooled chillers.
Considerations when Using Adiabatic Chillers
Water Usage
Direct Adiabatic Chillers: In direct adiabatic chillers, a significant amount of water is required for the evaporation process. The water consumption can be a concern, especially in regions with limited water resources. However, in some cases, the water used can be sourced from non – potable or recycled water, reducing the impact on the potable water supply. It is important to carefully assess the water availability and cost in the area where the direct adiabatic chiller will be installed. For example, in a factory located in an arid region, the use of treated wastewater for the direct adiabatic chiller can be a viable option.
Indirect Adiabatic Chillers: Indirect adiabatic chillers generally require less water compared to direct adiabatic chillers. The water used for evaporation is in a closed – loop system, and the amount of water lost through evaporation is relatively small. However, proper water treatment is still necessary to prevent scale formation and corrosion in the water – evaporation chamber and the heat exchanger. For example, in an indirect adiabatic chiller used in a commercial building, regular water treatment can ensure the long – term performance of the chiller and prevent any issues related to water quality.
Maintenance Requirements
Water – Related Components: Both direct and indirect adiabatic chillers have water – related components that require regular maintenance. In direct adiabatic chillers, the water spray nozzles need to be cleaned regularly to prevent clogging. In indirect adiabatic chillers, the heat exchanger and the water – evaporation chamber need to be inspected and maintained to ensure proper heat transfer and water evaporation. The water treatment system, if used, also requires regular monitoring and adjustment to maintain water quality. For example, in a direct adiabatic chiller used in an industrial plant, the water spray nozzles may need to be cleaned weekly to ensure consistent performance.
Refrigeration Cycle Components: In addition to the water – related components, the standard refrigeration cycle components (compressor, condenser, expansion valve, and evaporator) of adiabatic chillers need to be maintained as in any other chiller system. Regular checks of refrigerant levels, compressor performance, and heat – exchanger cleanliness are essential to ensure optimal operation. For example, the compressor in an adiabatic chiller should be serviced annually to check for any signs of wear and to ensure proper lubrication.
Environmental Impact of Water Treatment Chemicals (if used)
Chemical Usage and Disposal: In some cases, water treatment chemicals may be used in adiabatic chillers to prevent corrosion and scale formation. These chemicals need to be carefully managed to minimize their environmental impact. The disposal of used water treatment chemicals should follow local environmental regulations. For example, if a strong acid or base is used for water treatment, proper neutralization and disposal methods must be employed to avoid polluting water sources.
Alternative Water Treatment Methods: There is a growing interest in using more environmentally friendly water treatment methods in adiabatic chillers. For example, some manufacturers are exploring the use of natural substances or advanced filtration techniques to treat the water used in the chiller. These alternative methods can reduce the use of potentially harmful chemicals and contribute to a more sustainable operation of the adiabatic chiller.
Future Trends in Adiabatic Chillers
Technological Advancements
Improved Water Management Systems: Future adiabatic chillers are likely to see advancements in water management systems. This may include the development of more efficient water – recycling technologies to further reduce water consumption. For example, new membrane – based water – recovery systems could be integrated into adiabatic chillers to capture and reuse the evaporated water. Additionally, smart sensors and control systems may be used to optimize the water usage based on the ambient conditions and the cooling load.
Enhanced Heat – Transfer Materials and Designs: Research is ongoing to develop more efficient heat – transfer materials and designs for adiabatic chillers. The use of advanced materials in the heat exchanger, such as nanocomposites or high – performance polymers, could further improve the heat – transfer efficiency of the chiller. Additionally, innovative designs for the adiabatic pre – cooling section may be developed to optimize the evaporation process and reduce energy consumption even further. For example, new geometric designs for the water – spray nozzles in direct adiabatic chillers could improve the evaporation rate and the uniformity of the cooled air.
Related recommendations
thermal oil heating system
66Thermal Oil Heating Systems: A Comprehensive OverviewI. IntroductionA thermal oil heating system is a closed - loop system that utilizes thermal oil (also known as heat - transfer oil) as the medi...
View detailsmedical chillers
208Medical Chillers: High-Precision Temperature Control Solutions Medical chillers play a critical role in the healthcare industry, providing precise temperature control for medical equipment, lab...
View detailschiller capacity tons
192Understanding Chiller Capacity in Tons Chiller capacity is a critical parameter in the specification and selection of chillers for HVAC systems. It refers to the cooling capacity of a chiller, ...
View detailswater chiller temperature range
271Water Chiller Temperature Range: Balancing Efficiency and Performance Water chillers are an essential component of many heating, ventilation, and air conditioning (HVAC) systems, providing reli...
View details
HelloPlease log in