air cooled screw chillers
Air – Cooled Screw Chillers: A Comprehensive Overview
Air – cooled screw chillers are widely used in various industries and applications for their ability to provide efficient cooling. They are an essential part of many cooling systems, offering reliable and effective temperature control.
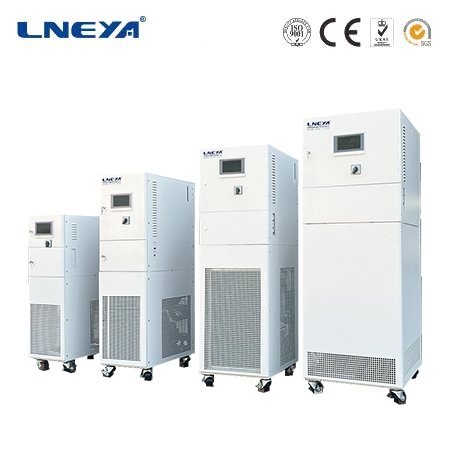
Working Principle
Refrigeration Cycle Basics
Air – cooled screw chillers operate based on the vapor – compression refrigeration cycle. At the heart of this cycle is the screw compressor. The screw compressor takes in low – pressure, low – temperature refrigerant vapor. Inside the compressor, two intermeshing helical screws (rotors) compress the refrigerant. As the refrigerant is compressed, its pressure and temperature increase significantly.
The high – pressure, high – temperature refrigerant vapor then enters the condenser. In an air – cooled chiller, the condenser consists of a series of finned tubes. Ambient air is forced over these tubes by fans. Heat is transferred from the hot refrigerant vapor to the air, causing the refrigerant to condense into a high – pressure liquid.
After leaving the condenser, the high – pressure liquid refrigerant passes through an expansion device, typically an expansion valve. The expansion valve reduces the pressure of the refrigerant, which causes it to expand and cool down rapidly.
Finally, the cold, low – pressure refrigerant enters the evaporator. In the evaporator, the refrigerant absorbs heat from the water or other fluid that needs to be cooled. As the refrigerant absorbs heat, it vaporizes, and the cooled fluid can then be circulated for use in the process. The cycle repeats continuously to maintain the desired cooling effect.
Screw Compressor Operation
The screw compressor in an air – cooled screw chiller has several advantages. It can handle large volumes of refrigerant, making it suitable for medium – to – high – capacity applications. The compression process in a screw compressor is relatively smooth compared to some other types of compressors, such as reciprocating compressors. This results in lower vibration and noise levels. The compressor’s capacity can be adjusted by varying the speed of the rotors or by using slide valves. Slide valves allow for continuous modulation of the compressor’s capacity, which is beneficial for applications where the cooling load varies.
Structure of Air – Cooled Screw Chillers
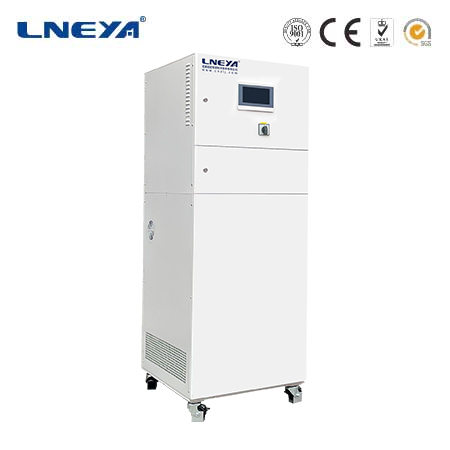
Screw Compressor
The screw compressor is a key component. It is designed to be durable and efficient. The rotors are typically made of high – quality alloy steel to withstand the high pressures and mechanical stresses during operation. The compressor housing is also constructed to be robust, providing a hermetic seal to prevent refrigerant leakage.
Condenser
The condenser in an air – cooled screw chiller is optimized for heat transfer with air. The finned tubes are designed to increase the surface area in contact with the air, enhancing the heat – transfer efficiency. The fans used to blow air over the condenser are carefully selected based on the required air volume and pressure. They are often variable – speed fans, which can adjust the air flow rate according to the cooling load, further improving energy efficiency.
Evaporator
The evaporator is where the heat exchange between the refrigerant and the fluid to be cooled occurs. It can be designed in different configurations, such as shell – and – tube or plate – type. In a shell – and – tube evaporator, the refrigerant usually flows through the tubes, while the fluid to be cooled flows around the tubes in the shell. Plate – type evaporators offer high heat – transfer efficiency in a compact size.
Expansion Device
The expansion device, such as an expansion valve, is crucial for controlling the flow of refrigerant into the evaporator. It ensures that the refrigerant enters the evaporator at the correct pressure and temperature. There are different types of expansion valves, including thermostatic expansion valves (TXV) and electronic expansion valves (EXV). TXV adjusts the refrigerant flow based on the temperature and pressure of the refrigerant at the evaporator outlet, while EXV provides more precise control by using electronic sensors and a controller.
Performance Advantages
Simple Installation
Air – cooled screw chillers are relatively easy to install compared to water – cooled chillers. They do not require a complex water – cooling system, such as a cooling tower and associated water – treatment equipment. This makes them a suitable choice for locations where water is scarce or where the installation of a water – cooling system is not practical.
Low Maintenance Requirements
Since there is no water – cooling system, the maintenance associated with water – related issues, such as scaling, corrosion, and microbiological growth, is eliminated. The main maintenance tasks for air – cooled screw chillers involve regular inspection of the compressor, condenser fins, fans, and refrigerant levels. The relatively simple structure of air – cooled chillers also contributes to easier maintenance.
Flexible Installation Location
They can be installed in a variety of locations, both indoors and outdoors. As long as there is sufficient space for air circulation around the condenser, the chiller can be placed in areas that are convenient for the application. This flexibility is beneficial for retrofitting existing facilities or for applications where the available space is limited.
Applications
Commercial Buildings
In commercial buildings, air – cooled screw chillers are commonly used for air – conditioning systems. They can provide chilled water to air – handling units, which then cool and dehumidify the air in the building. This is essential for creating a comfortable indoor environment for occupants. For example, in large office buildings, shopping malls, and hotels, air – cooled screw chillers can handle the significant cooling loads required to maintain a pleasant temperature throughout the building.
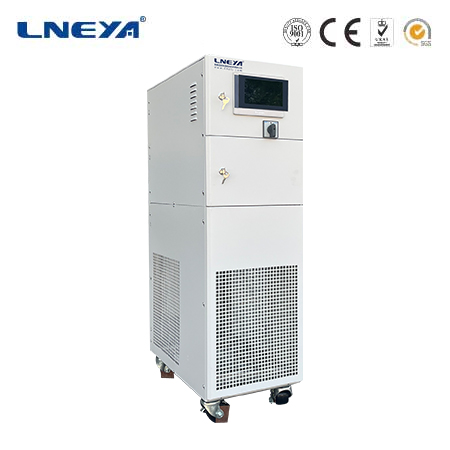
Industrial Applications
In industrial settings, air – cooled screw chillers are used to cool various processes and equipment. In the food and beverage industry, they can be used to cool products during production, storage, and transportation. For instance, in a brewery, the chiller can cool the beer during fermentation and storage to maintain the desired taste and quality. In manufacturing plants, air – cooled screw chillers can be used to cool machinery, such as injection – molding machines in the plastics industry. This helps to prevent overheating of the equipment and ensures smooth operation.
Data Centers
Data centers generate a large amount of heat due to the operation of servers and other electronic equipment. Air – cooled screw chillers can be used to cool the air – conditioning systems in data centers. Maintaining a low and stable temperature in data centers is crucial for the reliable operation of servers and to extend their lifespan. The ability of air – cooled screw chillers to provide efficient cooling in a relatively compact footprint makes them a viable option for data center cooling.
Choosing an Air – Cooled Screw Chiller
Cooling Capacity
Determining the appropriate cooling capacity is essential. The cooling capacity of a chiller is measured in tons of refrigeration (TR) or kilowatts (kW). It is important to accurately calculate the cooling load of the application. Factors such as the size of the space, the heat generated by equipment, and the number of occupants need to be considered. Choosing a chiller with too little capacity will result in insufficient cooling, while a chiller with too much capacity may lead to inefficient operation and higher energy costs.
Energy Efficiency
Energy – efficient air – cooled screw chillers can significantly reduce operating costs over time. Look for chillers with high energy – efficiency ratios (EER) or coefficient of performance (COP) values. Newer models often incorporate advanced technologies, such as variable – speed drives for compressors and fans. These technologies can adjust the chiller’s operation based on the actual cooling load, improving energy efficiency.
Noise Level
In some applications, such as in noise – sensitive areas like hospitals or residential buildings, the noise level of the chiller is an important consideration. Air – cooled screw chillers with low – noise fans and well – insulated compressor housings can be selected to minimize noise pollution. Manufacturers often provide noise – level specifications for their products, which can be used to make an informed decision.
Maintenance of Air – Cooled Screw Chillers
Regular Cleaning
The condenser fins should be cleaned regularly to remove dirt, dust, and debris. This improves heat transfer efficiency. Cleaning can be done using a brush or a compressed – air blower. In dirty environments, more frequent cleaning may be required.
Refrigerant Level Check
Periodically check the refrigerant level in the chiller. Low refrigerant levels can indicate a leak, which should be repaired promptly. Over – charging or under – charging the refrigerant can also affect the chiller’s performance and energy efficiency.
Component Inspection
Inspect the compressor, fans, and other components regularly for signs of wear, damage, or abnormal operation. Check the belts (if applicable) for proper tension and signs of cracking. The electrical components, such as wiring and controls, should also be inspected to ensure safe and proper operation.
In conclusion, air – cooled screw chillers are versatile and reliable cooling devices. Understanding their working principle, structure, performance advantages, applications, selection criteria, and maintenance requirements is crucial for effectively utilizing them in various cooling applications.
Related recommendations
cooling chiller machine
202Cooling Chiller Machines: Efficient Temperature Control for Diverse Applications Cooling chiller machines are critical components in HVAC systems, designed to provide precise temperature contro...
View details40 ton chiller
16A 40 - ton chiller is a substantial cooling system designed to remove a significant amount of heat from a space or process. The "40 - ton" rating refers to its cooling capacity, where 1 ton of coo...
View detailsprocess heaters
190The Role and Importance of Process Heaters in Industrial Processes Process heaters play a critical role in a wide range of industries, from petrochemical to food processing. They are used to ma...
View details1.5 ton water chiller
172Introduction to 1.5 Ton Water ChillersA 1.5 ton water chiller is an industrial cooling system designed to remove heat from various processes, providing a cooling capacity of 18,000 BTU/HR. These c...
View details
HelloPlease log in