chemistry heater
Introduction to Chemistry Heaters
Chemistry heaters are specialized devices that play a crucial role in various chemical applications. They are designed to supply heat energy, which is often a fundamental requirement for initiating and controlling chemical reactions, as well as for sample preparation and other chemical operations. By providing a controlled heat source, these heaters enable chemists to achieve the specific temperature conditions necessary for successful chemical processes.
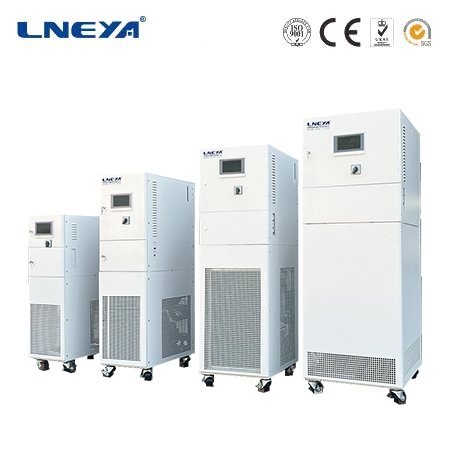
Working Principles
Electric Resistance Heating
Operation
In electric resistance heaters, an electric current is passed through a resistive element. Materials such as nichrome are commonly used for these elements due to their high electrical resistance. According to Joule’s law (Q = I²Rt, where Q is the heat generated, I is the current, R is the resistance, and t is the time), when an electric current flows through the resistive element, heat is produced. For example, in a simple hot plate used in a chemistry laboratory, the heating element is made of a resistive material. When the hot plate is plugged in and the current is switched on, the resistive element heats up, and the heat is transferred to the container placed on the hot plate, such as a beaker containing a chemical solution.
Advantages and Disadvantages
Advantages: Electric resistance heating is relatively simple in design and easy to control. The temperature can be adjusted by changing the amount of electric current flowing through the resistive element. It is also a clean source of heat as it does not produce combustion by – products, which is important in a laboratory or industrial setting where the presence of contaminants can affect chemical reactions.
Disadvantages: It can be energy – intensive, especially for high – temperature applications. The efficiency of heat transfer may be limited in some cases, and there is a risk of overheating if the temperature control mechanism malfunctions.
Induction Heating
Operation
Induction heating works on the principle of electromagnetic induction. A coil carrying an alternating current (AC) is placed near the object to be heated, which is usually a metal container or sample. The alternating magnetic field generated by the coil induces an electric current (eddy current) in the metal object. These eddy currents encounter the resistance of the metal, and according to Joule’s law, heat is generated within the object itself. For instance, in an industrial – scale chemical process where a metal reaction vessel needs to be heated, an induction heating system can be used. The induction coil is wrapped around the reaction vessel, and when the AC current is applied to the coil, the vessel heats up rapidly.
Advantages and Disadvantages
Advantages: Induction heating is highly efficient as the heat is generated directly within the object being heated. It allows for rapid heating and precise temperature control. Since the heating is contact – less (the coil does not need to touch the object), there is less risk of contamination, and it can be used in applications where a clean heating process is essential.
Disadvantages: The equipment for induction heating is relatively complex and expensive compared to some other heating methods. It is mainly suitable for heating metal objects, and its effectiveness depends on the electrical conductivity and magnetic properties of the material being heated.
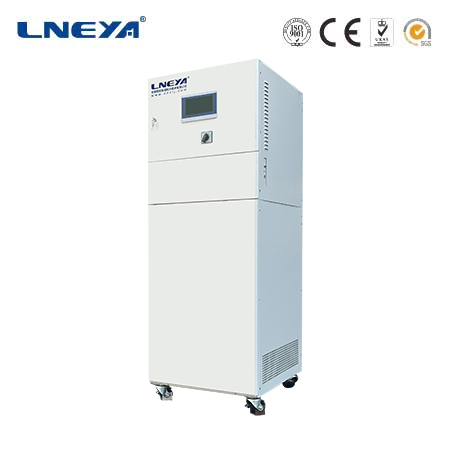
Combustion – Based Heating
Operation
Combustion – based chemistry heaters involve the burning of a fuel, such as natural gas, propane, or alcohol. In a Bunsen burner, which is a common combustion – based heating device in chemistry laboratories, natural gas (usually methane) is mixed with air in the burner tube. The gas – air mixture is ignited at the top of the burner, and the combustion reaction produces a hot flame. This flame can be used to heat glassware, such as test tubes or flasks, containing chemical substances. In industrial settings, large – scale furnaces may use propane or other fuels to heat reaction chambers or to carry out high – temperature chemical processes.
Advantages and Disadvantages
Advantages: Combustion – based heating can provide high – temperature heat sources, which are useful for many chemical reactions that require elevated temperatures. It can be cost – effective, especially when the cost of fuel is relatively low. In some cases, it may be easier to implement in areas where an electrical infrastructure is limited.
Disadvantages: Combustion produces by – products, such as carbon dioxide, water vapor, and in some cases, pollutants like carbon monoxide or nitrogen oxides. These by – products need to be properly vented to avoid contamination of the chemical environment and to ensure safety. The temperature control in combustion – based heating may not be as precise as in some electric – based heating methods.
Types of Chemistry Heaters
Hot Plates
Design and Features
Hot plates are one of the most common types of chemistry heaters. They typically consist of a flat, heated surface, often made of ceramic or metal. The heating element is usually embedded beneath the surface. Many hot plates have adjustable temperature controls, allowing users to set the desired temperature. Some advanced hot plates may also have features such as magnetic stirring capabilities. In these models, a magnetic stir bar placed inside the container on the hot plate can be rotated by a magnetic field generated by the hot plate, which helps in mixing the chemical solution while heating.
Applications
In a laboratory, hot plates are used for a variety of purposes. They can be used to heat solutions during chemical reactions, such as in the synthesis of organic compounds. For example, when preparing a buffer solution, a hot plate can be used to dissolve salts and other components more quickly by heating the water in which they are being dissolved. Hot plates are also useful for evaporating solvents from a solution, a common process in chemical analysis.
Heating Mantles
Design and Features
Heating mantles are designed to fit around round – bottomed flasks or other glassware. They are usually made of a heat – resistant material, such as fiberglass, with an embedded heating element. Heating mantles provide a more uniform heating distribution around the glassware compared to some other heating methods. They often come with temperature controllers that can be adjusted to maintain a specific temperature. Some heating mantles are also designed to be compatible with different sizes of glassware, with adjustable straps or a flexible design.
Applications
Heating mantles are commonly used in organic chemistry laboratories for reflux reactions. In a reflux setup, a round – bottomed flask containing a reaction mixture is placed inside the heating mantle. The heating mantle provides the necessary heat to keep the reaction mixture at a specific temperature, and the condenser attached to the flask allows the vapors to condense and return to the flask, ensuring that the reaction proceeds without loss of reactants or products. Heating mantles are also used in distillation processes, where they heat the flask containing the liquid mixture to be distilled.
Laboratory Ovens
Design and Features
Laboratory ovens are enclosed chambers that can be heated to a specific temperature. They usually have a well – insulated body to minimize heat loss. Laboratory ovens can reach a wide range of temperatures, from relatively low temperatures for drying samples to high temperatures for sintering or annealing processes. They are equipped with temperature controllers, which can be set to maintain a constant temperature within the oven. Some laboratory ovens also have fans to ensure uniform heat distribution inside the chamber.
Applications
Laboratory ovens are used for drying chemical samples. For example, in analytical chemistry, solid samples need to be dried to a constant weight before further analysis. The oven provides a controlled environment to remove moisture from the samples. In materials science, laboratory ovens are used for heat – treating materials. For instance, annealing of metals or ceramics in a laboratory oven can change their physical properties, such as improving the ductility of metals or enhancing the strength of ceramics.
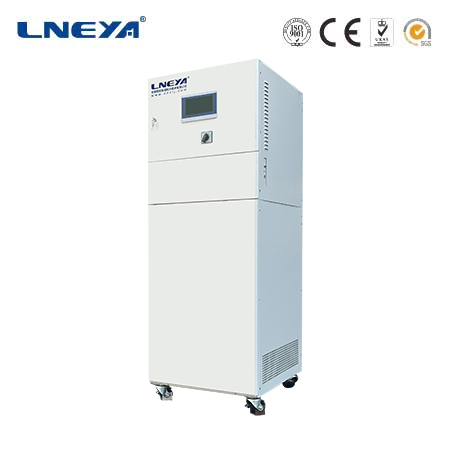
Applications in Chemistry
Chemical Reactions
Initiation and Control
Chemistry heaters are essential for initiating many chemical reactions. For example, in an endothermic reaction, heat needs to be supplied to break the bonds of the reactants and start the reaction. In the synthesis of ammonia through the Haber – Bosch process, high temperatures (around 400 – 500 °C) are required. Industrial – scale heaters, such as large – capacity furnaces, are used to provide the necessary heat. In a laboratory, a hot plate or heating mantle can be used to initiate reactions like the esterification reaction between an alcohol and a carboxylic acid. The heat helps in increasing the reaction rate by providing the activation energy required for the reaction to occur.
Heaters also play a crucial role in controlling the rate of chemical reactions. By adjusting the temperature, chemists can either speed up or slow down a reaction. In a polymerization reaction, precise temperature control using a heater is necessary to ensure the formation of polymers with the desired molecular weight and structure.
Reaction Optimization
In chemical research, heaters are used to optimize reaction conditions. Different reactions may have different optimal temperature ranges for maximum yield. For example, in the production of a particular pharmaceutical compound, chemists may conduct experiments at various temperatures using chemistry heaters to determine the temperature at which the reaction gives the highest yield of the desired product while minimizing the formation of by – products.
Sample Preparation
Drying Samples
As mentioned earlier, laboratory ovens are commonly used for drying chemical samples. In environmental analysis, soil or water samples may need to be dried before analysis to remove moisture that could interfere with the analytical techniques. In pharmaceutical manufacturing, active pharmaceutical ingredients (APIs) need to be dried to a specific moisture content to ensure their stability and quality.
Dissolving and Mixing
Hot plates are often used for dissolving solid chemicals in a solvent. In a biochemistry laboratory, when preparing solutions for enzyme assays, hot plates can be used to dissolve substrates or co – factors more quickly. The magnetic stirring feature of some hot plates also helps in thorough mixing of the components, ensuring a homogeneous solution.
Maintenance of Chemistry Heaters
Regular Cleaning
Surface Cleaning
For hot plates and heating mantles, regular cleaning of the heating surface is important. Chemical spills on the surface of a hot plate can not only affect its appearance but also potentially react with the heating element or cause uneven heating. A clean, non – abrasive cloth can be used to wipe the surface when the hot plate is cool. For heating mantles, any residue on the inner surface that comes in contact with the glassware should be removed to prevent contamination of the reaction mixture.
Oven Interior Cleaning
Laboratory ovens should be cleaned regularly to remove any residue from previous samples. This can be done using a mild detergent and water solution, followed by thorough rinsing and drying. Residue left in the oven can affect the temperature distribution and may also decompose or react with new samples being placed in the oven.
Component Checks
Heating Element Inspection
In all types of chemistry heaters, the heating element should be inspected regularly. For electric resistance heating elements, signs of wear, such as cracks or discoloration, should be checked. If a heating element is damaged, it may not heat evenly or may stop working altogether. In induction heaters, the induction coil should be checked for any signs of damage or loose connections. In combustion – based heaters, the burner should be inspected for proper fuel flow and combustion efficiency.
Temperature Controller Checks
The temperature controllers in chemistry heaters need to be calibrated regularly to ensure accurate temperature settings. Over time, the sensors in the temperature controller may drift, leading to inaccurate temperature readings. Calibration involves comparing the temperature reading on the controller with a known – accurate thermometer and adjusting the controller settings if necessary.
Safety Precautions
Ventilation
Combustion – based heaters, such as Bunsen burners, produce combustion by – products. Proper ventilation is essential to remove these by – products, especially in a laboratory or industrial setting. In a laboratory, fume hoods should be used when working with Bunsen burners to ensure that harmful gases are safely vented out of the working area.
Overheating Protection
All chemistry heaters should have some form of overheating protection. In electric heaters, this may be in the form of a thermal cut – off switch that automatically turns off the heater if the temperature exceeds a certain limit. Operators should also be trained to recognize signs of overheating, such as unusual odors or excessive heat, and take appropriate action, such as turning off the heater and allowing it to cool down.
Choosing the Right Chemistry Heater
Temperature Range Requirements
Determining the Required Temperature
The first step in choosing a chemistry heater is to determine the temperature range required for the application. Different chemical reactions and sample preparation processes have different temperature needs. For example, a simple evaporation process may only require a temperature of around 50 – 80 °C, which can be easily achieved with a basic hot plate. However, a high – temperature reaction like the calcination of metal oxides may require temperatures in the range of 800 – 1200 °C, which would necessitate a laboratory oven or a specialized high – temperature furnace.
Selecting a Heater with the Appropriate Range
Once the required temperature range is known, a heater that can cover that range should be selected. It is important to note that the heater should be able to maintain the desired temperature within an acceptable tolerance. Some heaters may have a wide temperature range but may not be very accurate in maintaining a specific temperature. For applications where precise temperature control is crucial, such as in pharmaceutical synthesis, a heater with a high – precision temperature controller should be chosen.
Power Requirements
Calculating the Power Needed
The power requirement of a chemistry heater depends on factors such as the volume of the sample or reaction mixture, the desired heating rate, and the type of heating method. For example, heating a large – volume reaction mixture in a round – bottomed flask using a heating mantle will require more power compared to heating a small test tube on a hot plate. The power needed can be calculated using the formula Q = mcΔT/t, where Q is the heat energy required, m is the mass of the substance being heated, c is the specific heat capacity of the substance, ΔT is the change in temperature, and t is the time over which the heating is to occur. Once the heat energy is calculated, the power (P = Q/t) can be determined, and a heater with an appropriate power rating can be selected.
Considering Energy Efficiency
In addition to meeting the power requirements, energy efficiency should also be considered. Induction heaters, for example, are generally more energy – efficient compared to electric resistance heaters in some applications as they generate heat directly within the object being heated. Choosing an energy – efficient heater can not only save on energy costs but also be more environmentally friendly.
Application – Specific Needs
Type of Chemical Process
The type of chemical process being carried out also influences the choice of heater. For reactions that require a gentle and uniform heating, such as in some delicate organic syntheses, a heating mantle may be a better choice. For applications where rapid heating and precise temperature control are needed, such as in some analytical techniques, an induction heater or a high – precision hot plate may be more suitable.
Safety and Compatibility
Safety is a crucial factor. If the chemical process involves flammable or volatile substances, a heater with proper safety features, such as spark – proof construction or overheating protection, should be selected. Compatibility with the materials being used is also important. For example, if the reaction vessel is made of a non – magnetic material, an induction heater may not be suitable.
Related recommendations
water bath machine
33Water bath machines have become an indispensable tool in many fields, especially in laboratories and certain industrial processes. Their ability to provide a controlled and stable thermal environm...
View detailscirculating water chiller
14Circulating Water ChillersCirculating water chillers are integral components in numerous systems where maintaining a low and stable water temperature is essential. They are designed to cool water...
View detailsheat and cooling units
155Introduction to Heat and Cooling Units Heat and cooling units are devices designed to regulate indoor temperatures, providing comfort and maintaining optimal conditions for various activities. ...
View detailschiller 7 kw
300Understanding 7 kW Chillers A 7 kW chiller is a versatile piece of equipment that provides cooling capacities suitable for a variety of applications. With a cooling power equivalent to 7 kilowa...
View details
HelloPlease log in