chiller cycling
Introduction
Chiller cycling is an important aspect of the operation of chiller systems. It involves the repeated starting and stopping of the chiller unit in response to various factors within the cooling system. Understanding chiller cycling is essential for ensuring the efficient and reliable operation of chillers, as improper cycling can lead to a range of issues, from reduced equipment lifespan to increased energy consumption.
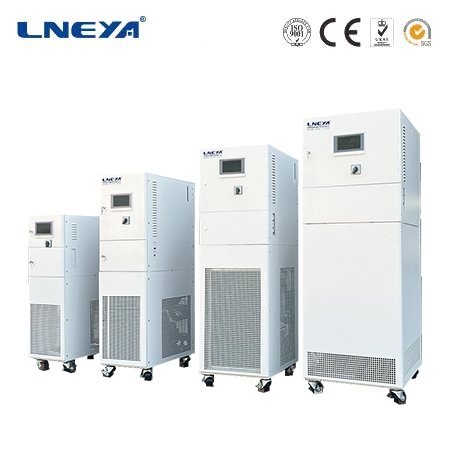
How Chiller Cycling Works
In Vapor – Compression Chillers
Temperature – Based Cycling: In vapor – compression chillers, cycling is often triggered by temperature changes. A thermostat or temperature sensor is installed in the area being cooled or in the coolant loop. When the temperature rises above a setpoint, the chiller is activated. The compressor starts, and the refrigerant begins its cycle of compression, condensation, expansion, and evaporation to remove heat. As the temperature drops and reaches the lower setpoint, the chiller is turned off. For example, in a commercial building’s air – conditioning system, if the indoor temperature setpoint is 25°C and it rises to 26°C, the vapor – compression chiller will start. Once the temperature is cooled back down to 25°C, the chiller will stop.
Pressure – Based Cycling: Pressure sensors can also play a role in chiller cycling. In the refrigerant circuit, high – and low – pressure switches are used. If the pressure in the refrigerant system deviates from the normal operating range, it can trigger the chiller to start or stop. For instance, if the low – pressure side of the refrigerant system drops below a certain value, indicating a potential problem such as low refrigerant charge or a blockage, the chiller may stop to prevent damage to the compressor.
In Absorption Chillers
Heat – Input and Temperature Cycling: Absorption chillers operate based on a heat – driven process. Cycling in these chillers can be related to the availability of the heat source and the temperature of the system. When the heat source, such as waste heat from an industrial process or a natural gas – fired heater, is available and the temperature in the chiller system indicates a need for cooling, the chiller starts. The absorption, generation, condensation, and evaporation processes begin. As the cooling demand is met and the temperature in the system reaches an acceptable level, the chiller stops. For example, in an industrial plant where waste heat is used to power an absorption chiller, if the waste heat is present and the temperature of the process fluid being cooled starts to rise, the chiller will initiate its operation. Once the process fluid is cooled to the desired temperature, the chiller will cycle off.
The Impact of Frequent Chiller Cycling
On Equipment Lifespan
Stress on Compressors: In vapor – compression chillers, the compressor is one of the most critical components affected by frequent cycling. Each time the compressor starts, it experiences a high – inrush current and mechanical stress as it accelerates from rest to operating speed. Frequent starting and stopping can cause wear and tear on the compressor’s bearings, pistons (in reciprocating compressors), and motor windings. Over time, this can lead to premature compressor failure. For example, a reciprocating compressor in a small – scale chiller that cycles frequently may experience increased friction in its pistons and cylinders, resulting in reduced efficiency and eventually a breakdown.
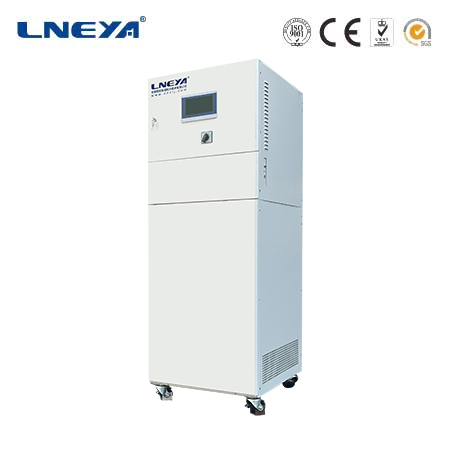
Valve and Component Wear: Other components such as expansion valves, solenoid valves, and check valves are also affected. Expansion valves, which regulate the flow of refrigerant, can experience wear due to the rapid changes in pressure and flow during cycling. Solenoid valves, which control the flow of refrigerant or other fluids in the system, may have their coils overheat or their moving parts wear out from frequent operation. Check valves, which prevent backflow, can also be damaged by the repeated pressure changes associated with cycling. In a water – cooled chiller system, the frequent cycling of the water – regulating valves can lead to leaks and reduced valve lifespan.
On Energy Consumption
Increased Start – Up Energy: Starting a chiller requires a significant amount of energy. The compressor, in particular, draws a large inrush current during start – up. Frequent cycling means that this high – energy start – up process occurs more often. For example, a chiller that cycles on and off every 10 minutes will consume more energy in start – up operations compared to a chiller that has a more stable, continuous operation. This increased start – up energy consumption can lead to higher overall energy bills for the facility using the chiller.
Inefficient Operation at Part – Load: When a chiller cycles frequently, it may not have enough time to reach its optimal operating efficiency. Chillers are designed to operate most efficiently at a certain load level. Frequent cycling can cause the chiller to spend more time at part – load conditions, where its efficiency is lower. In addition, the system may not have time to stabilize, and the components may not reach their ideal operating temperatures and pressures, further reducing energy efficiency. A large – scale industrial chiller that cycles frequently may operate at only 60 – 70% of its maximum efficiency during each cycle, compared to 80 – 90% efficiency when operating continuously at a stable load.
Causes of Chiller Cycling Issues
Improper Thermostat Settings
Incorrect Setpoints: If the thermostat setpoints are too close together, the chiller will cycle more frequently. For example, if the cooling setpoint is set at 24°C and the cut – off setpoint is set at 23.5°C in a commercial building’s chiller system, the chiller will turn on and off more often as the temperature in the building fluctuates within this narrow range. This can be easily adjusted by widening the temperature differential between the setpoints, such as setting the cooling setpoint at 24°C and the cut – off setpoint at 22.5°C.
Thermostat Malfunction: A faulty thermostat can also cause cycling problems. If the thermostat is not accurately sensing the temperature, it may send incorrect signals to the chiller, causing it to start or stop at inappropriate times. For instance, a thermostat that has a calibration error may think the temperature is higher than it actually is, leading to the chiller cycling on when it is not necessary. In such cases, the thermostat needs to be calibrated or replaced.
Refrigerant – Related Problems
Low Refrigerant Charge: A low refrigerant charge in the chiller system can cause cycling issues. When there is not enough refrigerant, the chiller may not be able to remove heat effectively. The system pressure may drop, and the chiller may cycle on and off in an attempt to maintain the desired temperature. For example, in a vapor – compression chiller, if the refrigerant charge is low, the evaporator may not be able to absorb heat properly, and the compressor may overheat, leading to frequent cycling. Adding the correct amount of refrigerant, as specified by the manufacturer, can solve this problem.
Refrigerant Contamination: Contaminated refrigerant can also affect chiller cycling. If the refrigerant contains impurities such as moisture, non – condensable gases, or dirt, it can cause problems with the heat – transfer process and the operation of the compressor and other components. The presence of moisture can lead to corrosion in the system, and non – condensable gases can increase the pressure in the condenser, both of which can cause the chiller to cycle more frequently. Refrigerant recovery, purification, or replacement may be necessary to address this issue.
Cooling Load Problems
Over – Sizing or Under – Sizing of the Chiller: If the chiller is over – sized for the cooling load, it will reach the desired temperature quickly and cycle off. Then, as the heat builds up slowly in the space or process being cooled, the chiller will cycle back on. This results in frequent cycling. On the other hand, an under – sized chiller will struggle to meet the cooling load and may cycle continuously in an attempt to cool the area. For example, in a data center, if a chiller is over – sized for the heat generated by the servers, it will cycle on and off frequently. Proper sizing of the chiller, based on accurate load calculations, is essential to prevent such cycling problems.
Fluctuating Cooling Load: A rapidly fluctuating cooling load can also cause chiller cycling issues. In some industrial processes, the heat load may vary significantly during different production stages. If the chiller system is not equipped to handle these rapid changes in load, it will cycle on and off. For instance, in a plastic injection – molding factory, the cooling load may change drastically when the injection process starts and stops. Installing a variable – speed drive on the chiller’s compressor or using a more advanced control system can help the chiller adapt to the fluctuating load and reduce cycling.
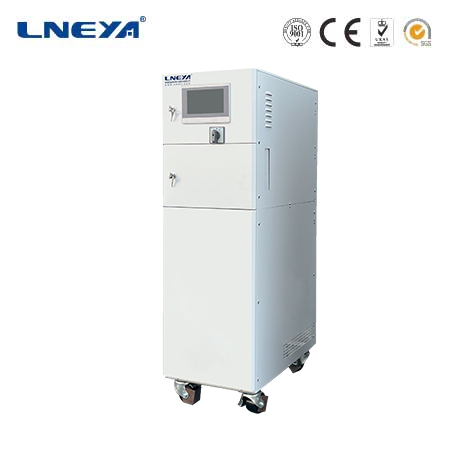
Solutions to Chiller Cycling Problems
Adjusting Thermostat Settings
Optimizing Setpoints: As mentioned earlier, adjusting the thermostat setpoints can significantly reduce chiller cycling. By widening the temperature differential between the cooling setpoint and the cut – off setpoint, the chiller will not cycle as frequently. However, it is important to ensure that the adjusted setpoints still maintain a comfortable or suitable temperature for the application. In a residential air – conditioning system, increasing the temperature differential from 1°C to 2 – 3°C can reduce cycling without sacrificing too much comfort.
Using Smart Thermostats: Smart thermostats can also be a solution. These thermostats can learn the cooling patterns of the space or process and adjust the setpoints accordingly. They can also be connected to other sensors in the building, such as occupancy sensors, to further optimize the chiller’s operation. For example, a smart thermostat in an office building can detect when the building is unoccupied and adjust the chiller’s setpoints to a more energy – efficient level, reducing cycling during non – working hours.
Addressing Refrigerant Issues
Refrigerant Charge Check and Adjustment: Regularly checking the refrigerant charge in the chiller system is crucial. Using proper refrigerant – charging equipment, technicians can measure the refrigerant level and add or remove refrigerant as needed. It is important to follow the manufacturer’s specifications for the correct refrigerant charge. In a commercial refrigeration chiller, if the refrigerant charge is found to be low, a technician can carefully add the appropriate amount of refrigerant to restore proper operation and reduce cycling.
Refrigerant Purification or Replacement: If the refrigerant is contaminated, it may need to be purified or replaced. Refrigerant purification can involve using special filtration equipment to remove impurities such as moisture and dirt. In cases where the contamination is severe, refrigerant replacement may be the best option. For example, in a chiller system that has been exposed to water due to a leak in the cooling tower, the refrigerant may be contaminated with moisture. In such cases, refrigerant replacement is often necessary to ensure the proper functioning of the chiller and reduce cycling.
Managing the Cooling Load
Proper Chiller Sizing: Accurate load calculations are essential for proper chiller sizing. By considering factors such as the size of the space, the heat – generating equipment, and the insulation, engineers can determine the appropriate chiller capacity. In a new construction project, a detailed load calculation should be carried out before selecting a chiller. If an existing chiller is over – sized or under – sized, it may be possible to adjust the system by adding or removing components, or in some cases, replacing the chiller with a more appropriately sized unit.
Load Balancing and Control: For applications with fluctuating cooling loads, load – balancing and control strategies can be implemented. Variable – speed drives on the chiller’s compressor and pumps can adjust the system’s capacity according to the load. In addition, using multiple chillers in parallel and controlling their operation based on the load can also help. For example, in a large shopping mall, multiple chillers can be installed, and a control system can be used to turn on or off the chillers as the cooling load changes throughout the day, reducing cycling of individual chillers.
The Importance of Cycling Control in Chiller Operation
Energy Efficiency
Reducing Unnecessary Cycling: By effectively controlling chiller cycling, energy efficiency can be significantly improved. Reducing unnecessary start – up operations and ensuring that the chiller operates at its optimal load for longer periods can lead to substantial energy savings. A well – controlled chiller system can operate at a higher efficiency, reducing the overall energy consumption of the facility. In a large industrial complex, proper cycling control of the chillers can result in a 10 – 20% reduction in energy consumption over a year.
Optimizing Part – Load Performance: Cycling control also helps in optimizing the chiller’s part – load performance. By adjusting the chiller’s operation based on the actual cooling load, the system can operate more efficiently even at part – load conditions. Advanced control systems can ensure that the chiller’s components, such as the compressor and fans, operate at the most efficient speed and capacity, reducing energy waste.
Equipment Longevity
Minimizing Component Stress: Proper cycling control minimizes the stress on chiller components. By reducing the frequency of start – up and shutdown, the wear and tear on components such as compressors, valves, and motors are decreased. This can extend the lifespan of the chiller and its components, reducing the need for frequent maintenance and replacement. For example, a chiller with effective cycling control may have a compressor lifespan that is 2 – 3 years longer than a chiller with excessive cycling.
Preventing Premature Failure: Cycling control also helps in preventing premature failure of the chiller system. By maintaining stable operating conditions and reducing the risk of overheating or other operational problems associated with improper cycling, the overall reliability of the chiller is enhanced. This is particularly important in applications where continuous cooling is critical, such as in data centers and hospitals.
Maintenance and Monitoring for Effective Chiller Cycling
Regular Equipment Inspections
Component Checks: Regular inspections of chiller components are essential for ensuring proper cycling. Technicians should check the compressor for signs of wear, leaks, and abnormal noise. Expansion valves, solenoid valves, and other valves should be inspected for proper operation and any signs of damage. The condenser and evaporator coils should be checked for fouling, which can affect heat transfer and lead to cycling problems. In a monthly maintenance check of a chiller, a technician may notice that the expansion valve is not opening and closing properly, which can be corrected before it causes significant cycling issues.
Thermostat and Sensor Calibration: Thermostats and temperature sensors should be calibrated regularly to ensure accurate temperature sensing. Pressure sensors, if used for cycling control, should also be calibrated. Incorrectly calibrated sensors can lead to improper cycling. For example, a thermostat that is miscalibrated by 1°C can cause the chiller to cycle more frequently than necessary. Calibration can be done using standard calibration equipment and following the manufacturer’s guidelines.
Performance Monitoring
Data Logging: Installing data – logging equipment to monitor the chiller’s performance can provide valuable insights into cycling behavior. Data such as temperature, pressure, energy consumption, and cycling frequency can be logged over time. By analyzing this data, operators can identify trends and potential problems. For example, if the data shows that the chiller is cycling more frequently during a particular time of day, it may indicate a problem with the cooling load or a component malfunction.
Remote Monitoring: Remote monitoring systems allow operators to monitor the chiller’s performance from a central location. This is particularly useful for large – scale installations or for facilities with multiple chillers. Remote monitoring can provide real – time alerts if there are any cycling – related issues, such as excessive cycling or abnormal operating conditions. For example, a facility manager can receive an alert on their mobile device if a chiller in a remote data center starts cycling more frequently than normal, allowing for quick intervention.
In conclusion, chiller cycling is a complex but important aspect of chiller operation. By understanding how cycling works, its impacts, the causes of cycling problems, and the solutions available, operators can ensure the efficient, reliable, and long – lasting performance of chiller systems.
Related recommendations
What are the steps for stopping a small water chiller?
791What are the steps for stopping a small water chiller? Stop the small chiller and enter normal shutdown, emergency shutdown, automatic shutdown, and long-term shutdown stop modes. ...
View detailsWhat is the maintenance and inspection of a 200 ton chiller?
801What is the maintenance and inspection of a 200 ton chiller? 1. Check the stability of voltage and current 2. Regularly inspect the compressor The necessary acceptance tes...
View detailswater cooled chiller types
225Types of Water Chillers Water chillers are categorized based on the type of compressor and the refrigeration cycle they use: Centrifugal Chillers: These chillers use a centrifugal compressor...
View detailsheater lab
201Laboratory Heaters: Types, Applications, and Safety Laboratory heaters are essential for maintaining precise temperature control in various scientific applications. They are used for a wide ran...
View details
HelloPlease log in