chiller engineering
Chiller engineering is a specialized field within mechanical and HVAC (Heating, Ventilation, and Air Conditioning) engineering. It focuses on the design, development, installation, and maintenance of chiller systems, which are essential for removing heat from a process or space and providing cooling. Chillers are used in a wide variety of applications, from industrial processes to commercial buildings and even some residential settings. The engineering aspects of chillers ensure that these systems operate efficiently, reliably, and cost – effectively.
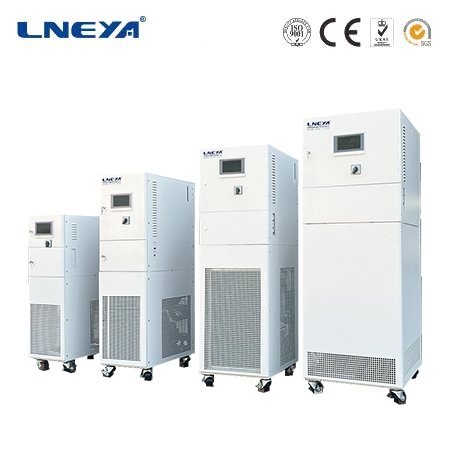
Fundamental Refrigeration Principles in Chiller Engineering
Vapor – Compression Refrigeration Cycle
The most common refrigeration cycle used in chiller engineering is the vapor – compression cycle. This cycle consists of four main components: the compressor, condenser, expansion device, and evaporator.
Compressor: The cycle starts with the compressor. Low – pressure, low – temperature refrigerant vapor is drawn into the compressor. The compressor then compresses the refrigerant, increasing its pressure and temperature. This process requires energy input, usually in the form of electricity. For example, in a reciprocating compressor, pistons compress the refrigerant vapor within cylinders.
Condenser: After compression, the hot, high – pressure refrigerant vapor enters the condenser. In the condenser, heat is transferred from the refrigerant to a cooling medium. In air – cooled chillers, the cooling medium is ambient air, while in water – cooled chillers, it is water. As the refrigerant releases heat, it condenses into a high – pressure liquid. The condenser is typically designed with a large surface area, often in the form of finned tubes in air – cooled models or shell – and – tube heat exchangers in water – cooled models, to enhance heat transfer.
Expansion Device: The high – pressure liquid refrigerant then passes through an expansion device, such as a thermostatic expansion valve or a capillary tube. The expansion device reduces the pressure of the refrigerant, causing it to expand and cool down. This process is adiabatic, meaning no heat is added or removed from the refrigerant during expansion.
Evaporator: The low – pressure, low – temperature refrigerant enters the evaporator. In the evaporator, the refrigerant absorbs heat from the process fluid (usually water in a chiller system) that needs to be cooled. As the refrigerant absorbs heat, it vaporizes back into a low – pressure vapor, and the cycle repeats. The evaporator can also be a shell – and – tube or plate – type heat exchanger, depending on the application.
Absorption Refrigeration Cycle (Less Common but Notable)
Another refrigeration cycle used in some chiller applications is the absorption cycle. This cycle uses a heat source (such as steam, hot water, or natural gas combustion) instead of a compressor to drive the refrigeration process.
Absorber: In an absorption chiller, a refrigerant (usually water in a water – lithium bromide system) is absorbed by a absorbent (lithium bromide solution in this case). This absorption process releases heat.
Generator: The rich absorbent – refrigerant solution is then pumped to the generator, where it is heated. The heat causes the refrigerant to vaporize from the solution. The high – pressure refrigerant vapor then passes through a condenser, similar to the vapor – compression cycle, where it condenses and releases heat.
Expansion and Evaporation: After condensation, the high – pressure liquid refrigerant passes through an expansion device and then enters the evaporator, where it absorbs heat and vaporizes. The weak absorbent solution from the generator is returned to the absorber to complete the cycle. Absorption chillers are often used in applications where there is a readily available waste heat source, such as in some industrial plants or combined – heat – and – power (CHP) systems.
Design Aspects of Chiller Engineering
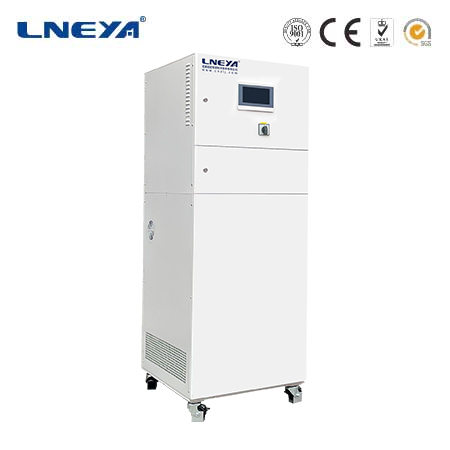
Cooling Load Calculations
One of the first steps in chiller engineering design is accurately calculating the cooling load. The cooling load is the amount of heat that needs to be removed from the space or process to maintain the desired temperature.
Sensible Heat Load: Sensible heat is the heat that causes a change in temperature without a change in phase. Factors contributing to the sensible heat load include the heat generated by equipment, lighting, and the occupants in a building. In an industrial process, the heat generated by machinery and chemical reactions also contributes to the sensible heat load. For example, in a data center, the servers generate a significant amount of sensible heat that needs to be removed by the chiller system.
Latent Heat Load: Latent heat is the heat involved in a phase change, such as the heat required to evaporate water (humidity control). In a building, the latent heat load is mainly due to the moisture brought in by ventilation air and the moisture generated by occupants. In some industrial processes, such as in food processing where there may be significant evaporation or condensation, latent heat loads are also important to consider.
Calculation Methods: Engineers use various methods to calculate cooling loads. In building applications, the ASHRAE (American Society of Heating, Refrigerating and Air – Conditioning Engineers) Handbook provides detailed procedures. These methods take into account factors like building orientation, insulation, internal heat gains, and outdoor climate conditions. In industrial applications, process engineers work closely with mechanical engineers to determine the heat loads based on the specific process requirements.
Chiller Type Selection
Based on the cooling load calculations and other factors, engineers select the appropriate type of chiller.
Air – Cooled vs. Water – Cooled Chillers: Air – cooled chillers are generally more suitable for smaller – scale applications or in locations where water is scarce. They are simpler in design as they do not require a complex water – cooling system. However, their cooling efficiency can be limited by high ambient air temperatures. Water – cooled chillers, on the other hand, are more energy – efficient, especially in large – scale applications. They use water as a heat – transfer medium between the refrigerant and the environment, often requiring a cooling tower. But they are more complex and require a reliable water source.
Centrifugal, Reciprocating, and Scroll Compressor – Based Chillers: Centrifugal chillers are typically used for large – scale applications where high cooling capacities are required. They offer high efficiency at full load but may have reduced efficiency at part – load. Reciprocating chillers are suitable for smaller – to – medium – sized applications and can handle a wide range of cooling loads. Scroll compressors are often used in smaller chillers due to their compact size, quiet operation, and relatively high efficiency.
System Integration
Chiller systems need to be integrated with other components in a cooling system.
Piping and Ductwork Design: The design of piping for the refrigerant, chilled water, and condenser water (in water – cooled chillers) is crucial. Pipes need to be sized correctly to ensure proper flow rates and minimize pressure drops. In addition, ductwork for air – cooled chillers or in HVAC systems that use the chilled water needs to be designed to distribute the cooled air or water evenly.
Controls and Monitoring Systems: Chiller systems are equipped with controls to regulate the operation of the chiller and other components. These controls can include temperature sensors, pressure sensors, and variable – speed drives for compressors and fans. Monitoring systems are also installed to track the performance of the chiller, such as measuring energy consumption, refrigerant pressures, and temperatures. Advanced control systems can optimize the operation of the chiller based on real – time data, improving energy efficiency and system reliability.
Equipment Selection in Chiller Engineering
Compressor Selection
The compressor is a critical component in a chiller, and its selection depends on several factors.
Capacity and Efficiency: The compressor needs to have sufficient capacity to handle the cooling load of the chiller. Different types of compressors have different efficiency characteristics. For example, variable – speed compressors can adjust their speed based on the cooling load, improving energy efficiency at part – load conditions. Centrifugal compressors are known for their high efficiency at full load, while reciprocating compressors may be more suitable for applications with variable load requirements.
Reliability and Maintenance: Compressors should be reliable and easy to maintain. Some compressors, such as scroll compressors, have fewer moving parts, which can lead to higher reliability and lower maintenance requirements. In addition, the availability of spare parts and the ease of servicing the compressor are important considerations.
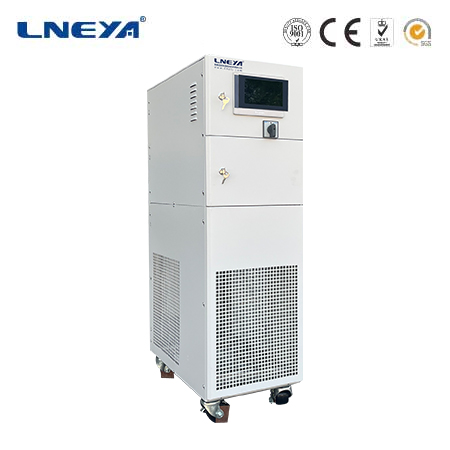
Heat Exchanger Selection
Heat exchangers, including condensers and evaporators, are essential for heat transfer in a chiller system.
Type and Material: There are different types of heat exchangers, such as shell – and – tube, plate – type, and finned – tube. The selection depends on factors like the application, heat – transfer requirements, and space limitations. For example, plate – type heat exchangers are known for their high heat – transfer efficiency and compact size, making them suitable for some applications where space is limited. The material of the heat exchanger is also important. In corrosive environments, materials like stainless steel or titanium may be used to ensure long – term durability.
Heat – Transfer Coefficient and Pressure Drop: The heat – transfer coefficient of the heat exchanger determines how effectively heat is transferred. Engineers need to select a heat exchanger with an appropriate heat – transfer coefficient to meet the cooling requirements. At the same time, the pressure drop across the heat exchanger should be minimized to reduce energy consumption.
Refrigerant Selection
The choice of refrigerant in a chiller is crucial for its performance and environmental impact.
Thermodynamic Properties: Refrigerants should have suitable thermodynamic properties, such as a high latent heat of vaporization, low boiling point, and high critical temperature. Different refrigerants have different performance characteristics. For example, R – 410A is a common refrigerant in air – conditioning and small – to – medium – sized chiller applications due to its good thermodynamic properties and relatively low environmental impact.
Environmental Impact: With increasing environmental awareness, the environmental impact of refrigerants is a major consideration. Refrigerants with high ozone – depletion potential (ODP) and high global – warming potential (GWP) are being phased out. For example, chlorofluorocarbons (CFCs) and hydrochlorofluorocarbons (HCFCs) have been largely replaced by hydrofluorocarbons (HFCs) and more recently by hydrofluoroolefins (HFOs), which have lower GWP values.
Installation and Commissioning of Chiller Systems
Installation Process
The installation of a chiller system involves several steps.
Site Preparation: The installation site needs to be properly prepared. This includes ensuring a stable foundation for the chiller unit, especially for large – scale chillers. In the case of water – cooled chillers, the location of the cooling tower needs to be carefully planned to ensure proper water circulation and ventilation.
Piping and Electrical Connections: Piping for the refrigerant, chilled water, and condenser water (if applicable) needs to be installed according to the design specifications. The pipes should be properly insulated to prevent heat transfer and energy losses. Electrical connections for the compressor, fans, and control systems need to be made correctly, following electrical safety codes.
Component Assembly: The chiller components, such as the compressor, heat exchangers, and expansion devices, need to be assembled and installed in the correct sequence. In some cases, pre – assembled chiller units may be delivered to the site, but still require proper connection and alignment.
Commissioning Procedures
Commissioning is a crucial step to ensure that the chiller system operates as designed.
System Checks: Before starting the chiller, a series of system checks are performed. This includes checking the refrigerant charge, ensuring proper lubrication of moving parts, and verifying the integrity of the piping and electrical systems.
Performance Testing: The chiller is then started, and performance testing is carried out. This involves measuring parameters such as refrigerant pressures, temperatures, flow rates of chilled water and condenser water (if applicable), and power consumption. The performance of the chiller is compared to the design specifications, and any adjustments are made as necessary.
Control System Calibration: The control system of the chiller needs to be calibrated. Temperature and pressure sensors are calibrated to ensure accurate readings, and the control algorithms are adjusted to optimize the operation of the chiller under different load conditions.
Maintenance and Troubleshooting in Chiller Engineering
Regular Maintenance Requirements
Regular maintenance is essential to keep chiller systems operating efficiently and reliably.
Component Inspection and Cleaning: Components such as the compressor, heat exchangers, and fans need to be inspected regularly. In air – cooled chillers, the condenser fins may need to be cleaned to remove dirt and debris, which can impede heat transfer. In water – cooled chillers, the condenser tubes may need to be cleaned to prevent scale formation. The compressor oil should be checked and changed according to the manufacturer’s recommendations.
Refrigerant Management: The refrigerant charge needs to be monitored regularly. Leaks in the refrigerant system should be detected and repaired promptly. In addition, the quality of the refrigerant should be checked, and any contaminants should be removed.
Control System Maintenance: The control system components, such as sensors and controllers, need to be maintained. Sensors should be calibrated periodically to ensure accurate readings, and software updates for the control system may be required to improve performance and functionality.
Troubleshooting Common Issues
Chiller systems may encounter various problems over time.
Low Cooling Capacity: If a chiller has low cooling capacity, possible causes could include a low refrigerant charge, a dirty condenser or evaporator, a malfunctioning compressor, or a problem with the expansion device. Engineers use diagnostic tools, such as pressure gauges and thermometers, to identify the root cause of the problem.
High Energy Consumption: High energy consumption in a chiller may be due to inefficient operation of the compressor, improper control settings, or a dirty heat exchanger. Adjusting the control settings, cleaning the heat exchanger, or servicing the compressor may help to reduce energy consumption.
Noisy Operation: Noisy operation can be caused by issues such as unbalanced fans, worn – out compressor bearings, or loose components. Identifying and addressing the source of the noise is important to ensure the long – term reliability of the chiller and to maintain a comfortable environment.
Conclusion
Chiller engineering is a complex and multifaceted field that combines knowledge of thermodynamics, heat transfer, fluid mechanics, and control systems. From the fundamental refrigeration principles to the design, installation, and maintenance of chiller systems, every aspect is crucial in providing efficient and reliable cooling solutions. By understanding the key elements of chiller engineering, engineers and facility managers can make informed decisions to optimize the performance of chiller systems, whether in industrial, commercial, or residential applications.
Related recommendations
large environmental chamber
184Introduction to Large Environmental Chambers Large environmental chambers are engineered to simulate various environmental conditions for testing the performance, reliability, and durability of...
View detailswater cooling and heating machine
180Water Cooling and Heating Machines: Versatile Temperature Control Solutions Water cooling and heating machines, commonly referred to as chillers, play a critical role in maintaining optimal tem...
View detailsprocess heaters
189The Role and Importance of Process Heaters in Industrial Processes Process heaters play a critical role in a wide range of industries, from petrochemical to food processing. They are used to ma...
View detailsheater for laboratory
15Heaters for LaboratoriesIn the realm of scientific research and experimentation, maintaining the correct temperature is often a fundamental requirement. Laboratory heaters play a pivotal role in ...
View details
HelloPlease log in