chiller lab equipment
Working Principles
Vapor – Compression Refrigeration Cycle
Compressor: The compressor is the core component that initiates the refrigeration process. It draws in low – pressure refrigerant vapor from the evaporator. Through mechanical compression, it increases the pressure and temperature of the refrigerant, converting it into high – pressure, high – temperature vapor. This rise in pressure and temperature is fundamental as it supplies the energy necessary for heat transfer within the system.
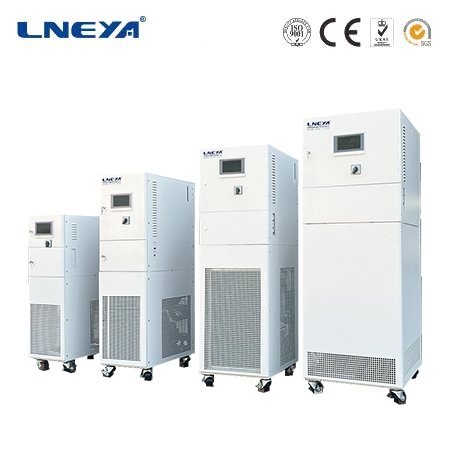
Condenser: The high – pressure, high – temperature refrigerant vapor then enters the condenser. In an air – cooled condenser, heat is directly dissipated into the surrounding air. For water – cooled condensers, heat is transferred to a secondary water source through a heat exchanger. As heat is removed, the refrigerant vapor condenses into a high – pressure liquid.
Expansion Valve: The high – pressure liquid refrigerant passes through the expansion valve. This valve restricts the flow of the refrigerant, causing a substantial drop in pressure. As the pressure decreases, the refrigerant expands, and its temperature drops rapidly, resulting in a low – temperature, low – pressure liquid – vapor mixture.
Evaporator: The low – temperature refrigerant mixture enters the evaporator, where it comes into contact with the process fluid or the equipment that needs to be cooled. Heat from the process fluid is absorbed by the refrigerant, causing the refrigerant to vaporize completely. The cooled process fluid is then recirculated back to the equipment, completing the cooling cycle.
Absorption Refrigeration Cycle (Less Common but Used in Specialized Labs)
Generator: In an absorption chiller, a refrigerant – absorbent solution is heated in the generator. For example, in a water – lithium bromide absorption system, when the solution is heated, the refrigerant (water) vaporizes, leaving the absorbent (lithium bromide) behind.
Condenser: The refrigerant vapor then proceeds to the condenser, where it releases heat and condenses into a liquid, similar to the vapor – compression cycle.
Expansion Valve: The liquid refrigerant passes through an expansion valve, which reduces its pressure and temperature.
Absorber: The low – pressure refrigerant liquid enters the absorber, where it is absorbed by the weak absorbent solution. This absorption process releases heat, which must be removed. The strong absorbent – refrigerant solution is then pumped back to the generator to complete the cycle.
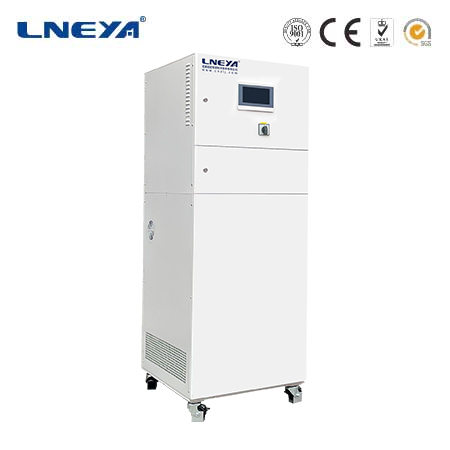
Types of Chiller Lab Equipment
Air – Cooled Chillers
Advantages
They are relatively simple in design and installation. Since they do not require a complex external water – cooling system, they are highly suitable for small – scale laboratories with limited space and infrastructure. Their operation and maintenance are also relatively straightforward as there is no need to manage water – related systems such as cooling towers or deal with water treatment issues.
In terms of initial investment, air – cooled chillers are often more cost – effective. The absence of a secondary water – cooling system reduces the overall equipment cost.
Disadvantages
Their cooling efficiency is significantly affected by ambient temperature. In hot environments, heat dissipation to the air becomes less efficient, which can lead to a substantial reduction in the chiller’s cooling capacity. This may result in unstable cooling performance for laboratory equipment.
They are generally noisier compared to water – cooled chillers due to the operation of cooling fans used for heat dissipation.
Water – Cooled Chillers
Advantages
Water – cooled chillers are more energy – efficient. Water is a better heat – transfer medium than air, enabling more efficient heat transfer in the condenser. This results in a more stable and reliable cooling performance, especially in high – heat – load applications or in high – temperature environments.
They can handle larger cooling capacities, making them suitable for large – scale laboratories with multiple high – power instruments or complex experimental setups.
Disadvantages
They require a cooling tower or a secondary water – cooling system, which increases the complexity of installation and operation. Regular water treatment is necessary to prevent issues such as corrosion, scaling, and biological growth in the water – cooling system.
The initial investment is higher due to the additional components and infrastructure required for the water – cooling system.
Applications in Different Laboratories
Chemical Laboratories
In chemical reactions, especially exothermic reactions, a large amount of heat is generated. Chiller lab equipment is used to remove this excess heat to control the reaction rate. For example, in the synthesis of fine chemicals, precise temperature control is crucial to obtain the desired product purity and yield. The chiller – cooled process fluid can be used to cool the reaction vessels, ensuring that the reaction proceeds under optimal temperature conditions.
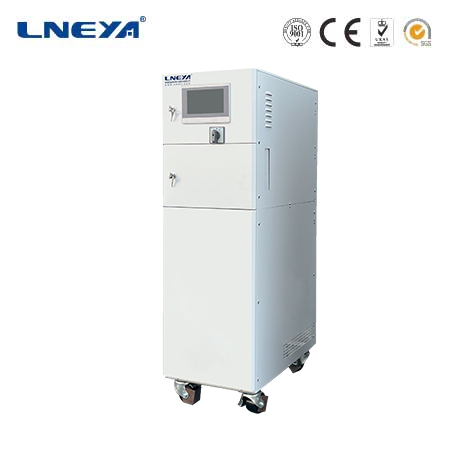
Biological Laboratories
In cell culture experiments, maintaining a constant and appropriate temperature is essential for cell growth and viability. Chillers can cool the incubators, providing a stable thermal environment for cell cultures. They are also used in DNA amplification processes such as polymerase chain reaction (PCR). In PCR, temperature cycling is required, and the chiller – cooled water helps to quickly change and maintain the specific temperatures needed at each step of the process.
Physical Laboratories
In experiments involving high – power lasers or superconducting magnets, these components generate a significant amount of heat during operation. Chiller lab equipment is used to cool these devices to prevent overheating, which could affect their performance and lifespan. For instance, in a synchrotron radiation facility, the high – power X – ray sources need to be cooled effectively, and water – cooled chillers are often employed for this purpose.
Factors to Consider When Choosing Chiller Lab Equipment
Cooling Capacity
It is essential to accurately calculate the total heat load of the laboratory equipment and processes that need to be cooled. This involves considering the heat generated by individual instruments, as well as any additional heat sources in the experimental setup. Select a chiller with a cooling capacity that can meet or slightly exceed the total heat load to ensure efficient and reliable cooling.
Temperature Control Precision
Different experiments have different requirements for temperature control. Some high – precision experiments, such as certain semiconductor material research or ultra – sensitive biological assays, may require the temperature to be controlled within a very narrow range, sometimes as precise as ±0.01°C. Choose a chiller that can achieve the required temperature control accuracy to ensure the success of these experiments.
Energy Efficiency
Energy consumption is an important factor, especially for laboratories that operate 24/7. Consider the energy – efficiency ratio (EER) or coefficient of performance (COP) of the chiller. A higher EER or COP indicates that the chiller can provide more cooling output per unit of energy input, resulting in lower energy costs and reduced environmental impact.
Maintenance Requirements
Look for a chiller with accessible components for routine maintenance tasks. This includes easy – to – replace filters for both the refrigerant and the process fluid side, as well as components that can be easily inspected for signs of wear or damage. Additionally, consider the availability of spare parts and local service providers to ensure minimal downtime in case of equipment failures.
Maintenance of Chiller Lab Equipment
Regular Inspections
Conduct regular visual inspections of the chiller to check for any signs of leaks, unusual vibrations, or abnormal noises. Inspect the refrigerant lines, connections, and the heat – transfer surfaces of the condenser and evaporator.
Filter Replacement
Replace the air filters (for air – cooled chillers) and the water filters (for water – cooled chillers) regularly. Clogged filters can reduce the efficiency of the chiller and may lead to overheating.
Refrigerant Level Check
Periodically check the refrigerant level. Low refrigerant levels can indicate a leak and will also reduce the cooling capacity of the chiller.
Water Treatment (for Water – Cooled Chillers)
For water – cooled chillers, proper water treatment is crucial. This includes maintaining the correct pH level, adding corrosion inhibitors, and preventing the growth of algae and bacteria in the water – cooling system.
In conclusion, chiller lab equipment is an integral part of modern laboratories. Understanding its working principles, types, applications, selection criteria, and maintenance requirements is essential for laboratories to ensure the smooth operation of experiments and the proper functioning of laboratory equipment.
Related recommendations
compact cooling unit
198Compact Cooling Units: Efficient Temperature Control for Space-Constrained Environments Compact cooling units offer a practical solution for cooling in environments where space is at a premium....
View detailsair cooled chiller working
63Air Cooled Chiller Working An air-cooled chiller is a crucial piece of equipment in the field of refrigeration and cooling, widely used in various applications such as commercial buildings, ind...
View detailsmulti stack chillers
248Introduction to Multi-Stack Chillers Multi-stack chillers, such as those offered by Multistack, are innovative HVAC solutions designed for scalability and efficiency. These chillers are particu...
View detailsadiabatic chiller
20Adiabatic Chillers: An In - Depth Exploration Introduction In the pursuit of more energy - efficient and sustainable cooling solutions, adiabatic chillers have emerged as a promising techn...
View details
HelloPlease log in