chiller operation
Introduction
Chillers are indispensable in modern cooling systems, playing a pivotal role in maintaining comfortable indoor environments in buildings, facilitating industrial manufacturing processes, and cooling critical equipment in data centers. The operation of a chiller involves a series of interrelated processes that work in harmony to remove heat from a target medium and transfer it elsewhere. A thorough comprehension of chiller operation is crucial for operators, facility managers, and anyone involved in the maintenance and optimization of cooling systems. This article aims to demystify the intricacies of chiller operation, exploring the underlying principles, key components, operational nuances, and best practices.
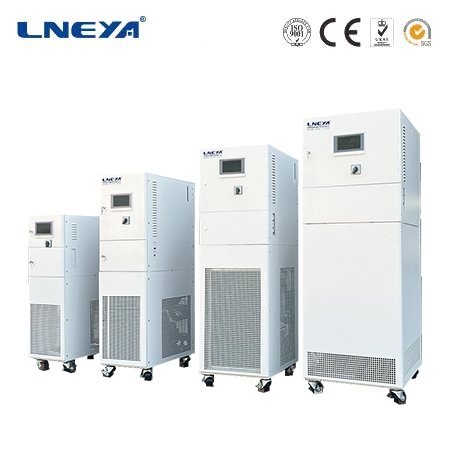
The Refrigeration Cycle: The Foundation of Chiller Operation
At the heart of every chiller’s functionality lies the refrigeration cycle, which consists of four fundamental stages: compression, condensation, expansion, and evaporation. These stages form a continuous loop, enabling the chiller to extract heat from the medium to be cooled and reject it to the environment.
Compression
The refrigeration cycle commences with the compressor. The compressor draws in low – pressure, low – temperature refrigerant gas from the evaporator. Through the application of mechanical energy, it compresses the gas, significantly increasing its pressure and temperature. This compression process is essential as it elevates the energy level of the refrigerant, making it capable of releasing heat in subsequent stages. Different types of compressors, such as reciprocating, scroll, and centrifugal compressors, are employed based on the chiller’s size and application. Each compressor type has its unique operating characteristics and efficiency levels, but all serve the primary function of compressing the refrigerant to initiate the heat – transfer process.
Condensation
Following compression, the high – pressure, high – temperature refrigerant gas enters the condenser. In an air – cooled chiller, fans circulate ambient air over the condenser coils, while in a water – cooled chiller, a secondary water source, often from a cooling tower, flows around the coils. As the hot refrigerant gas comes into contact with the cooler surfaces of the condenser coils, heat transfer occurs. The refrigerant releases its heat to the air or water, causing it to condense back into a liquid state. The efficiency of the condensation process depends on factors such as the temperature difference between the refrigerant and the cooling medium, the surface area of the condenser coils, and the flow rate of the cooling medium. Effective heat rejection in the condenser is vital for maintaining the overall performance of the chiller.
Expansion
The liquid refrigerant then passes through an expansion valve or capillary tube. This component creates a sudden drop in pressure. As the pressure of the refrigerant decreases, its temperature also drops significantly, transforming it into a low – pressure, low – temperature liquid – vapor mixture. The expansion valve plays a critical role in regulating the flow of the refrigerant into the evaporator, ensuring that the refrigerant enters the evaporator at the appropriate rate and condition for efficient heat absorption.
Evaporation
The final stage of the refrigeration cycle is evaporation. The low – pressure, low – temperature refrigerant mixture enters the evaporator. Here, it comes into contact with the medium that needs to be cooled, such as water in an air – conditioning system or a process fluid in an industrial application. The refrigerant absorbs heat from this medium, causing it to evaporate back into a gas. As the refrigerant evaporates, it cools the surrounding medium, which is then circulated back to the point of use. The cooled medium provides the desired cooling effect, whether it’s for maintaining a comfortable room temperature or ensuring the proper operation of industrial equipment. The refrigerant gas then returns to the compressor to restart the cycle.
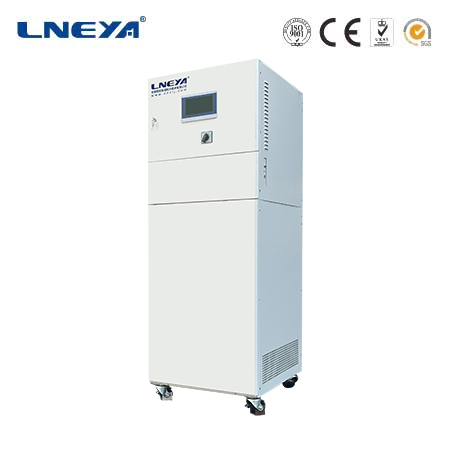
Key Components and Their Operational Roles
Compressors
Compressors are the central component of the chiller system, and their operation directly impacts the chiller’s overall performance and efficiency.
Reciprocating Compressors: Reciprocating compressors utilize a piston – cylinder arrangement. The piston moves back and forth within the cylinder, drawing in and compressing the refrigerant gas. These compressors are known for their durability and ability to handle a wide range of cooling capacities. However, they can be relatively noisy and may have lower energy efficiency compared to some modern compressor types. Regular maintenance of the piston rings, valves, and lubrication system is essential to ensure smooth operation and prevent wear and tear.
Scroll Compressors: Scroll compressors consist of two interlocking scrolls, one fixed and one orbiting. As the orbiting scroll moves, it creates a series of chambers that gradually decrease in volume, compressing the refrigerant gas. Scroll compressors offer high efficiency, quiet operation, and smooth performance. They are commonly used in smaller to medium – sized chillers. Their design reduces mechanical vibrations and wear, resulting in longer service life and lower maintenance requirements.
Centrifugal Compressors: Centrifugal compressors are typically employed in large – scale industrial and commercial applications that demand high cooling capacities. They operate by using a high – speed impeller to accelerate the refrigerant gas, increasing its pressure. Centrifugal compressors are highly efficient for handling large volumes of refrigerant but may require more complex maintenance and have a higher initial cost. Proper alignment of the impeller and monitoring of vibration levels are crucial for their reliable operation.
Condensers
Condensers are responsible for the heat rejection process in the chiller system.
Air – Cooled Condensers: Air – cooled condensers transfer the heat from the refrigerant to the ambient air. The condenser coils are finned to increase the surface area, enhancing heat – transfer efficiency. Fans blow air over the coils, carrying away the heat. The performance of air – cooled condensers is highly dependent on the ambient air temperature and humidity. In hot and humid conditions, their efficiency may decline due to the reduced temperature difference between the refrigerant and the air. Regular cleaning of the condenser coils to remove dirt, debris, and dust is essential to maintain optimal heat – transfer performance.
Water – Cooled Condensers: Water – cooled condensers use a secondary water source to remove heat from the refrigerant. The water circulates around the condenser coils, absorbing the heat from the refrigerant. The heated water is then either cooled in a cooling tower or discharged, depending on the system design. Water – cooled condensers generally offer higher efficiency compared to air – cooled condensers, as water has a greater heat – transfer capacity than air. However, they require a more complex infrastructure, including cooling towers, pumps, and water – treatment systems. Proper water treatment is necessary to prevent scaling, corrosion, and the growth of microorganisms in the water – cooling system, which can affect the performance and lifespan of the condenser.
Evaporators
Evaporators are where the cooling effect is generated.
Direct – Expansion (DX) Evaporators: In DX evaporators, the refrigerant evaporates directly inside the coils, absorbing heat from the surrounding air or fluid. These evaporators are commonly used in air – conditioning systems. The design of DX evaporators is optimized to maximize the heat – transfer surface area and ensure efficient evaporation of the refrigerant. The refrigerant flow rate and the temperature of the medium being cooled need to be carefully controlled to maintain the desired cooling performance.
Chilled – Water Evaporators: Chilled – water evaporators are used in systems where a secondary water loop is employed to distribute the cooling. The refrigerant in the evaporator cools the water, which is then pumped to various parts of the building or industrial process. Chilled – water evaporators are often larger and more complex than DX evaporators, as they need to handle a larger volume of water. Proper control of the water flow rate, temperature, and refrigerant level in the evaporator is crucial for efficient operation.
Expansion Valves
Expansion valves regulate the flow of the refrigerant from the high – pressure side (condenser) to the low – pressure side (evaporator).
Thermostatic Expansion Valves (TXV): TXVs are the most commonly used type of expansion valve. They use a temperature – sensing bulb located at the outlet of the evaporator to measure the superheat of the refrigerant. Based on the superheat value, the TXV adjusts the flow of the refrigerant to maintain a constant superheat, ensuring efficient evaporation in the evaporator. TXVs provide precise control over the refrigerant flow, which is essential for maintaining stable cooling performance.
Capillary Tubes: Capillary tubes are simple, fixed – orifice expansion devices commonly used in smaller chillers and refrigeration systems. They rely on their length and diameter to create a pressure drop and control the refrigerant flow. Capillary tubes are less expensive and require less maintenance compared to TXVs but offer less precise control over the refrigerant flow.
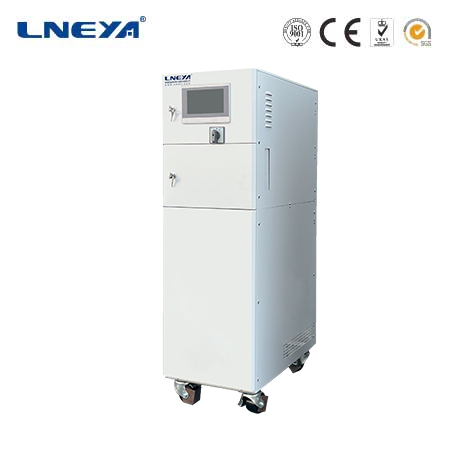
Operational Characteristics of Different Chiller Types
Air – Cooled Chillers
Air – cooled chillers are relatively easy to install and operate, as they do not require a complex water – cooling infrastructure. However, their operation is significantly influenced by ambient air conditions.
Seasonal Variations: During hot summer months, the performance of air – cooled chillers may deteriorate due to the elevated ambient air temperature. The compressor may have to work harder to maintain the desired cooling output, resulting in increased energy consumption. In colder months, the chiller may operate more efficiently, but precautions must be taken to prevent freezing of the condenser coils in extremely low temperatures. Some air – cooled chillers are equipped with 防冻 protection mechanisms, such as electric heaters or variable – speed fans, to address this issue.
Location and Ventilation: The location of the air – cooled chiller is critical for its operation. It should be installed in an area with good ventilation to ensure proper air circulation around the condenser. Obstructions, such as walls or other equipment, can restrict the air flow and reduce the chiller’s efficiency. Additionally, the ambient air quality can affect the performance of the chiller. If the air is dusty or contains contaminants, the condenser coils can become dirty quickly, requiring more frequent cleaning.
Water – Cooled Chillers
Water – cooled chillers offer higher efficiency and cooling capacity but demand more complex operation and maintenance.
Water – Cooling System Management: The operation of water – cooled chillers depends on the proper functioning of the water – cooling system, including the cooling tower, pumps, and water – treatment equipment. Regular monitoring of the water flow rate, temperature, and quality is essential. The water in the system needs to be treated to prevent scaling, corrosion, and the growth of bacteria and algae. This may involve adding chemicals, such as anti – scaling agents and biocides, and performing regular water – quality tests.
Cooling Tower Operation: The cooling tower plays a vital role in the operation of water – cooled chillers. It cools the water that has absorbed heat from the refrigerant in the condenser. Proper operation of the cooling tower includes maintaining the correct water level, ensuring the fan is functioning properly, and cleaning the tower regularly to remove debris and scale. In some cases, the cooling tower may need to be shut down for maintenance or cleaning, which can impact the operation of the chiller. Therefore, it’s important to have a well – planned maintenance schedule to minimize downtime.
Absorption Chillers
Absorption chillers operate on a different principle compared to compression – based chillers. They use a heat source, such as steam, hot water, or natural gas, instead of electricity to drive the refrigeration cycle.
Heat – Source Management: The operation of absorption chillers is highly dependent on the availability and quality of the heat source. The heat source needs to be supplied at the correct temperature and pressure to ensure efficient operation. Fluctuations in the heat – source supply can affect the performance of the chiller. For example, if the temperature of the hot water used as a heat source drops, the cooling capacity of the absorption chiller may decrease.
Solution Circulation: Absorption chillers use a refrigerant – absorbent solution, typically water – lithium bromide. The proper circulation and management of this solution are crucial for the chiller’s operation. The solution needs to be continuously regenerated and maintained at the right concentration. Regular monitoring of the solution’s properties, such as its concentration and pH level, is necessary to ensure the chiller operates efficiently and reliably.
Monitoring and Controlling Operational Parameters
Temperature Monitoring
Temperature is one of the most critical operational parameters in chiller operation.
Refrigerant Temperatures: Monitoring the temperature of the refrigerant at various points in the refrigeration cycle, such as the inlet and outlet of the compressor, condenser, and evaporator, provides valuable insights into the chiller’s performance. Abnormal refrigerant temperatures can indicate issues such as a malfunctioning compressor, a clogged condenser, or an improper refrigerant charge. For example, if the refrigerant temperature at the outlet of the evaporator is too high, it may mean that the evaporator is not absorbing enough heat, which could be due to a low refrigerant flow rate or a dirty evaporator coil.
Cooled – Medium Temperatures: The temperature of the medium being cooled, such as the chilled water in an air – conditioning system or the process fluid in an industrial application, also requires close monitoring. Maintaining the correct cooled – medium temperature is essential for meeting the cooling requirements of the application. If the temperature deviates from the set point, the control system can adjust the operation of the chiller, such as by changing the compressor speed or the refrigerant flow rate, to bring the temperature back to the desired level.
Pressure Monitoring
Pressure monitoring is equally important in chiller operation.
High – Side and Low – Side Pressures: The high – side pressure (in the condenser) and the low – side pressure (in the evaporator) are key indicators of the chiller’s performance. A significant increase in high – side pressure may indicate a problem with the condenser, such as poor heat transfer due to dirty coils or a malfunctioning fan. A low low – side pressure could suggest a refrigerant leak, a clogged expansion valve, or insufficient refrigerant charge. By continuously monitoring these pressures, operators can detect potential issues early and take corrective actions.
Differential Pressure: The differential pressure between the high – side and low – side of the chiller is also an important parameter. It reflects the pressure drop across the expansion valve and the refrigerant flow resistance in the system. An abnormal differential pressure can indicate problems with the expansion valve or the refrigerant piping. For example, a high differential pressure may mean that the expansion valve is not opening properly, restricting the refrigerant flow.
Refrigerant Flow and Level Monitoring
Refrigerant Flow: Monitoring the refrigerant flow rate is crucial for ensuring the efficient operation of the chiller. An improper refrigerant flow can lead to poor cooling performance, increased energy consumption, and potential damage to the chiller components. Some chillers are equipped with flow meters to measure the refrigerant flow rate. If the flow rate is too low, it may be due to a clogged filter, a malfunctioning expansion valve, or a refrigerant leak. If the flow rate is too high, it could indicate a problem with the control system or an oversized expansion valve.
Refrigerant Level: Maintaining the correct refrigerant level is essential for the proper operation of the chiller. A low refrigerant level can result in reduced cooling capacity, increased compressor wear, and potential compressor damage. On the other hand, an overcharged refrigerant system can also cause problems, such as high – side pressure spikes and reduced efficiency. Regularly checking the refrigerant level using sight glasses or pressure – temperature relationships is an important part of chiller operation and maintenance.
Control Systems
Modern chillers are equipped with advanced control systems to monitor and regulate their operation.
Thermostats and Temperature Controllers: Thermostats and temperature controllers are used to set and maintain the desired temperature of the cooled medium. They can be either mechanical or electronic and are often integrated with the chiller’s control system. These devices sense the temperature of the medium and send signals to the control system, which then adjusts the chiller’s operation to maintain the set temperature.
Variable – Speed Drives: Variable – speed drives are commonly used to control the speed of the compressor and fans in chillers. By adjusting the speed of these components, the chiller can match the cooling demand more precisely, resulting in energy savings. For example, during periods of low cooling demand, the compressor speed can be reduced, reducing the energy consumption of the chiller. Variable – speed drives are controlled by the chiller’s control system based on input from various sensors, such as temperature and pressure sensors.
Building Management Systems (BMS) Integration: Many chillers can be integrated with building management systems. This allows for centralized control and monitoring of the chiller along with other building systems, such as ventilation and lighting. Through BMS integration, facility managers can optimize the operation of the chiller based on the overall energy consumption and comfort requirements of the building. They can also receive real – time alerts and perform remote diagnostics, improving the efficiency and reliability of the chiller operation.
Related recommendations
3 ton water chiller
843 Ton Water Chiller: A Detailed IntroductionA 3 - ton water chiller is a device designed to remove heat from water, providing a continuous supply of chilled water for various applications. The "3 ...
View detailschiller temperature controller
231Chiller Temperature Controller: Precision Temperature Management Chiller temperature controllers play a vital role in maintaining the efficiency and effectiveness of chiller systems. These syst...
View detailsmedical chillers
224Medical Chillers: High-Precision Temperature Control Solutions Medical chillers play a critical role in the healthcare industry, providing precise temperature control for medical equipment, lab...
View detailsheating cooling system
280Introduction to Heating and Cooling Systems Heating and cooling systems play a vital role in ensuring the comfort and well-being of occupants in buildings while also managing energy consumption...
View details
HelloPlease log in