chiller temperature controller
Chiller Temperature Controller: Precision Temperature Management
Chiller temperature controllers play a vital role in maintaining the efficiency and effectiveness of chiller systems. These systems are designed to regulate the temperature of a chiller, ensuring that it operates within the desired parameters for optimal cooling. The chiller temperature controller monitors and adjusts various parameters, including flow rates, pressure, and refrigerant temperature, to maintain the set temperature points.
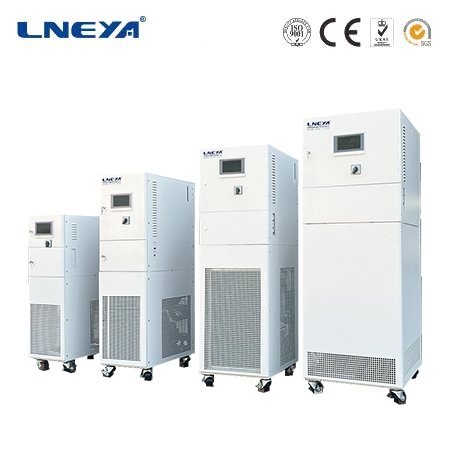
Principles of Chiller Temperature Control
The basic principle of a chiller temperature controller involves monitoring the temperature of the chilled water loop and the condenser water loop. Sensors are installed to detect the flow and return temperatures of both loops. The chiller also monitors the pressure of the evaporator and condenser. By measuring the temperature and pressure of the refrigerant, the operation can be plotted on pressure-enthalpy charts, allowing for precise control of the refrigeration cycle.
Components of a Chiller Temperature Controller
Key components of a chiller temperature controller include:
Flow Sensors: These sensors are connected to both the chilled water and condenser water circuits to ensure adequate water flow is maintained.
Temperature Sensors: Sensors are placed on the incoming and outgoing water in the chilled water loop and the condenser water loop to monitor temperature changes.
Pressure Sensors: These sensors measure the pressure in the evaporator and condenser to ensure optimal operating conditions.
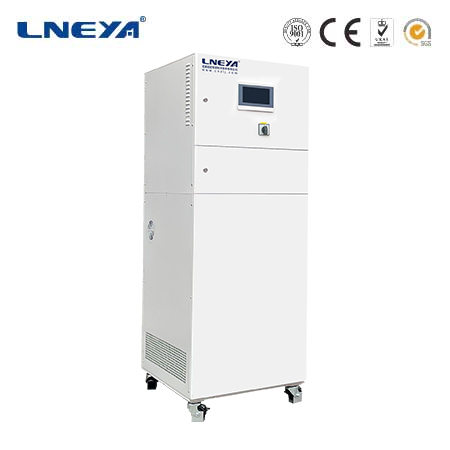
Refrigerant Temperature Sensors: Sensors are used to measure the suction line temperature, discharge line temperature, and liquid line temperature of the refrigerant.
Control Actuators: These are used to adjust the operation of the chiller, such as changing the position of vein guides in centrifugal chillers to control the capacity.
Applications of Chiller Temperature Controllers
Chiller temperature controllers are used in a variety of applications where precise temperature control is essential:
HVAC Systems: In commercial buildings, chillers provide essential cooling effects by counterbalancing heat from internal and external sources.
Industrial Processes: In manufacturing facilities and chemical plants, chillers cool machinery, control ambient temperatures, and ensure optimal conditions for production.
Data Centers: Chillers are crucial for maintaining precise temperature control to prevent overheating of sensitive electronic equipment.
Best Practices for Chiller Temperature Control
Best practices for chiller temperature control include:
System Sizing: It’s important to size the chiller and other system components appropriately to match the cooling demand while avoiding over-sizing, which can lead to inefficiencies.
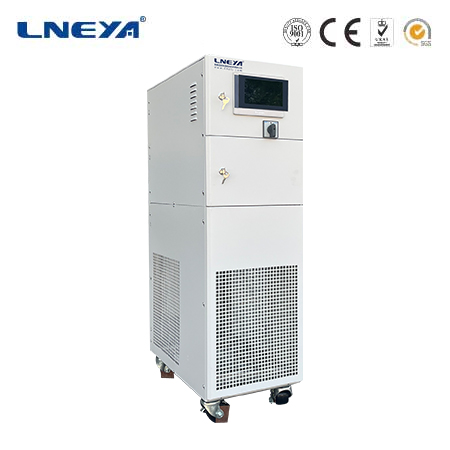
Energy Efficiency: Designing for energy efficiency involves selecting high-efficiency equipment, optimizing flow rates, and implementing variable speed operation of pumps and compressors.
Sustainability: Sustainable design principles can be incorporated by using environmentally friendly refrigerants and implementing energy recovery strategies.
Maintenance: Regular maintenance is essential for ensuring the chiller operates efficiently and reliably. This includes inspecting and cleaning the condenser coils, checking refrigerant levels, and verifying the operation of safety controls and sensors.
Market Trends in Chiller Temperature Control
The market for chiller systems is growing, driven by the need for energy-efficient cooling solutions and advancements in technology. Product features such as energy efficiency, expandability, compact design, low environmental impact, and wireless technology are crucial for market success. There is also a growing focus on using low global warming potential (GWP) refrigerants, such as HFOs or natural refrigerants like CO2.
In conclusion, chiller temperature controllers are essential for precise temperature management in various industries. By understanding the principles, applications, and best practices for chiller temperature control, operators can ensure efficient and reliable operation of their cooling systems. As the market for chiller systems continues to grow, there is an increasing focus on energy efficiency and sustainability, driving innovation in the design and operation of these critical components.
Related recommendations
thermal liquid heating system
231Introduction to Thermal Liquid Heating Systems Thermal liquid heating systems, also known as hot oil or heat transfer fluid systems, are engineered to transfer heat generated from a central hea...
View detailsHow to deal with abnormal flow rate of the circulating pump of the refrigerated chiller?
682How to deal with abnormal flow rate of the circulating pump of the refrigerated chiller? Abnormal flow rate of the circulating pump of the freezer may lead to a decrease in cooling effe...
View details1.5 ton water chiller
170Introduction to 1.5 Ton Water ChillersA 1.5 ton water chiller is an industrial cooling system designed to remove heat from various processes, providing a cooling capacity of 18,000 BTU/HR. These c...
View detailsefficient heating and cooling systems
28Efficient Heating and Cooling SystemsIn today's world, where energy conservation and environmental sustainability are of utmost importance, efficient heating and cooling systems have become a nec...
View details
HelloPlease log in