chillers uk
Chillers in the UK: A Comprehensive Guide
Chillers play a vital role in the United Kingdom across a wide range of industries and applications. They are used to remove heat from a process or space, providing a means to maintain a desired low temperature. This is crucial for ensuring the proper functioning of equipment, product quality, and human comfort.
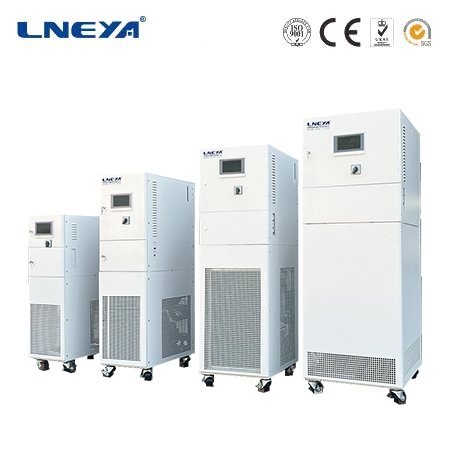
Types of Chillers in the UK
Air – Cooled Chillers
Operation and Characteristics: Air – cooled chillers in the UK operate on the vapor – compression refrigeration cycle. A compressor raises the pressure and temperature of the refrigerant. The hot refrigerant vapor then enters a condenser, where ambient air, forced by fans, cools it down, causing the refrigerant to condense. After passing through an expansion device, the cold refrigerant absorbs heat in the evaporator from the fluid or space to be cooled. These chillers are popular in the UK due to their relatively simple installation. They do not require a complex water – cooling infrastructure, making them suitable for locations where water availability is limited or where the installation of a water – cooled system is not practical, such as in some small – to – medium – sized commercial buildings.
Applications: In the UK, air – cooled chillers are commonly used in office buildings, restaurants, and small industrial facilities. They can provide sufficient cooling for air – conditioning systems in these buildings, maintaining a comfortable indoor environment. For example, in a small business office in London, an air – cooled chiller can effectively cool the space during hot summer months.
Water – Cooled Chillers
Operation and Characteristics: Water – cooled chillers use water as the cooling medium in the condenser. The refrigerant, after being compressed, releases heat to the water in the condenser. The warm water is then circulated to a cooling tower, where it dissipates heat to the atmosphere through evaporation and is cooled for reuse. Water – cooled chillers are more energy – efficient than air – cooled ones in the UK climate, especially in large – scale applications. They can achieve lower condensing temperatures, resulting in better overall system performance. However, they require a cooling tower and water – treatment system, which increases the initial installation cost and maintenance complexity.
Applications: In large industrial plants, such as those in the manufacturing and chemical sectors in the UK, water – cooled chillers are widely used. They can handle high cooling loads, which are typical in these industries. For instance, in a pharmaceutical manufacturing facility in the Midlands, water – cooled chillers are used to cool the production processes, ensuring the quality and stability of pharmaceutical products.
Absorption Chillers
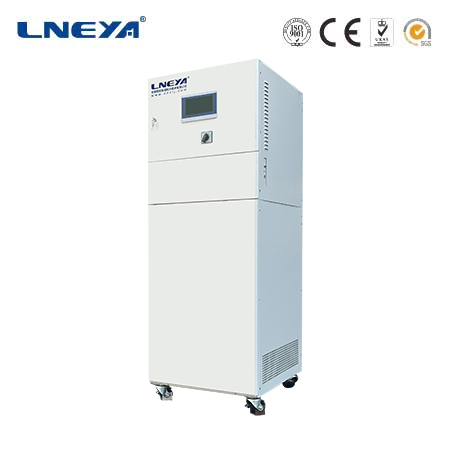
Operation and Characteristics: Absorption chillers in the UK operate using a heat source, such as steam, hot water, or natural gas, instead of a compressor. A refrigerant (usually water in a lithium – bromide – water system or ammonia in an ammonia – water system) is absorbed into a solution. When the solution is heated, the refrigerant is released and goes through the evaporation and condensation processes to provide cooling. These chillers are beneficial in the UK where there is an available waste – heat source, such as in combined heat and power (CHP) plants. They can be a more environmentally friendly option as they reduce the reliance on electricity – driven compressors.
Applications: In some UK hospitals and large commercial buildings with CHP systems, absorption chillers are used. The waste heat from the CHP system can be harnessed to power the absorption chiller, providing cooling for the building’s air – conditioning and other processes. This helps to improve the overall energy efficiency of the facility.
Energy – Efficiency Regulations in the UK
The Impact of Regulations on Chiller Selection
In the UK, energy – efficiency regulations have a significant impact on the selection of chillers. The government has implemented various policies to reduce energy consumption and carbon emissions. For example, the Energy – related Products (ErP) Directive sets minimum energy – efficiency requirements for a wide range of products, including chillers. Chillers sold in the UK must meet these standards. This means that buyers are more likely to choose energy – efficient models, such as those with high Seasonal Energy Efficiency Ratio (SEER) or Coefficient of Performance (COP) values.
The UK’s commitment to reducing greenhouse gas emissions under the Paris Agreement also influences the chiller market. Manufacturers are encouraged to develop more energy – efficient and environmentally friendly chiller technologies. This has led to the development of chillers with advanced features like variable – speed drives, which can adjust the chiller’s operation based on the actual cooling load, improving energy efficiency.
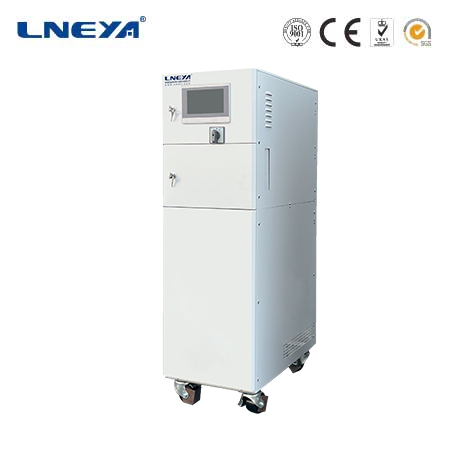
Energy – Labeling and Certification
Chillers in the UK are required to have energy – labels that provide information about their energy consumption and efficiency. The energy – label ranges from A (the most energy – efficient) to G (the least energy – efficient). This labeling system helps consumers and businesses make informed decisions when choosing a chiller. Additionally, there are certifications such as the BREEAM (Building Research Establishment Environmental Assessment Method) in the UK. Buildings that use energy – efficient chillers can score higher in BREEAM assessments, which is important for sustainable building design and operation.
Choosing the Right Chiller in the UK
Cooling Capacity Requirements
Calculating the correct cooling capacity is crucial when choosing a chiller in the UK. Factors such as the size of the space to be cooled, the heat generated by equipment, and the number of occupants need to be considered. For a commercial building in the UK, a detailed heat – load calculation should be performed. If the cooling capacity of the chosen chiller is too low, it will not be able to meet the cooling demand, resulting in discomfort or equipment overheating. On the other hand, if the capacity is too high, the chiller will operate inefficiently, leading to higher energy costs.
Cost – Effectiveness
Cost is an important consideration. In the UK, the initial purchase cost of a chiller is just one aspect. The long – term operating costs, including energy consumption and maintenance, should also be factored in. Energy – efficient chillers may have a higher upfront cost but can save significant amounts on energy bills over their lifespan. Additionally, the cost of maintenance, which includes regular servicing, replacement of parts, and potential repairs, should be considered. Some chillers may require more frequent maintenance or have higher – cost replacement parts, which can impact the overall cost – effectiveness.
Maintenance and After – Sales Service
Reliable maintenance and after – sales service are essential. In the UK, choosing a chiller from a manufacturer or supplier with a good reputation for after – sales support is advisable. This includes the availability of spare parts, prompt response to service requests, and the ability to provide technical support. Regular maintenance, such as cleaning the condenser coils in air – cooled chillers or checking the water – treatment system in water – cooled chillers, is necessary to ensure optimal performance and extend the lifespan of the chiller.
Maintenance of Chillers in the UK
Regular Cleaning and Inspection
For air – cooled chillers, the condenser fins should be cleaned regularly to remove dirt, dust, and debris. This improves heat transfer efficiency. In the UK’s often – variable climate, which can include dusty conditions in some areas, more frequent cleaning may be required. Water – cooled chillers need regular inspection of the cooling tower to prevent the growth of algae and other contaminants. The condenser tubes should also be checked for signs of scaling or corrosion.
Refrigerant Management
Monitoring and managing the refrigerant in chillers is crucial in the UK. Refrigerant leaks can not only affect the performance of the chiller but also contribute to environmental pollution. Regular checks for refrigerant levels and signs of leaks should be carried out. In the UK, there are regulations regarding the handling and disposal of refrigerants, and proper compliance is necessary.
Component Maintenance
The components of the chiller, such as the compressor, fans, and pumps, should be maintained regularly. In the UK, the compressor, being a critical component, may require periodic oil changes and inspection for wear and tear. The fans in air – cooled and water – cooled chillers should be checked for proper operation and balanced rotation. Electrical components, including wiring and controls, should also be inspected to ensure safe and proper functioning.
In conclusion, the chiller market in the UK is diverse, with a range of types, manufacturers, and regulations. Understanding these aspects is essential for businesses and consumers in the UK to make informed decisions when choosing, installing, and maintaining chillers to meet their cooling needs efficiently and sustainably.
Related recommendations
dc air conditioning
159DC Air Conditioning: Technology, Efficiency, and Applications DC air conditioning systems are integral to maintaining comfortable and efficient environments in various applications, from reside...
View detailssmall water chillers
194Small Water Chillers: Versatility in Cooling Solutions Introduction to Small Water ChillersSmall water chillers are essential in providing precise temperature control in confined spaces where t...
View detailsprocess heaters
13Process heaters are industrial equipment designed to raise the temperature of a process fluid, gas, or solid. They play a crucial role in numerous industries by providing the necessary heat for ch...
View detailsoil heater system
252Oil Heater System: Technology, Applications, and Efficiency Oil heater systems are widely used in industries such as chemical, petrochemical, and pulp-and-paper for maintaining process temperat...
View details
HelloPlease log in