circulating water chiller
Circulating Water Chillers
Circulating water chillers are integral components in numerous systems where maintaining a low and stable water temperature is essential. They are designed to cool water that is then circulated to remove heat from a variety of processes and equipment.
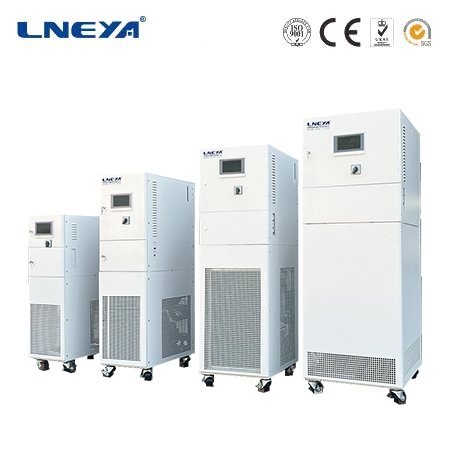
How Circulating Water Chillers Work
Circulating water chillers function based on the well – known refrigeration cycle, which involves four main components: the compressor, condenser, expansion valve, and evaporator.
Compressor: The compressor is the heart of the chiller system. It starts the cycle by drawing in low – pressure refrigerant vapor from the evaporator. Through mechanical compression, it increases the pressure and temperature of the refrigerant. This high – pressure, high – temperature vapor is then directed towards the condenser. The compression process is crucial as it enables the refrigerant to carry and release heat effectively in the subsequent stages of the cycle.
Condenser: In the condenser, the high – pressure, high – temperature refrigerant vapor releases its heat. In air – cooled circulating water chillers, the heat is dissipated into the surrounding air. Fins and fans are used to enhance the heat transfer process. The fins increase the surface area available for heat exchange, and the fans blow air over the fins, carrying away the heat. In water – cooled chillers, the heat is transferred to a secondary water loop. This secondary water may be connected to a cooling tower, where the heat is finally released into the atmosphere. As the refrigerant releases heat, it undergoes a phase change and condenses into a high – pressure liquid.
Expansion Valve: The high – pressure liquid refrigerant then passes through the expansion valve. This valve is designed to suddenly reduce the pressure of the refrigerant. As the pressure drops, the refrigerant expands and cools down substantially. It exits the expansion valve as a low – pressure, low – temperature two – phase mixture, consisting of both liquid and vapor.
Evaporator: In the evaporator, the low – pressure, low – temperature refrigerant comes into contact with the water that needs to be cooled. Heat is transferred from the water to the refrigerant. As the refrigerant absorbs heat, it vaporizes. The now – cooled water is then circulated to the areas or processes that require cooling, such as industrial equipment or air – handling units. The refrigerant, now in vapor form, returns to the compressor to start the cycle anew.
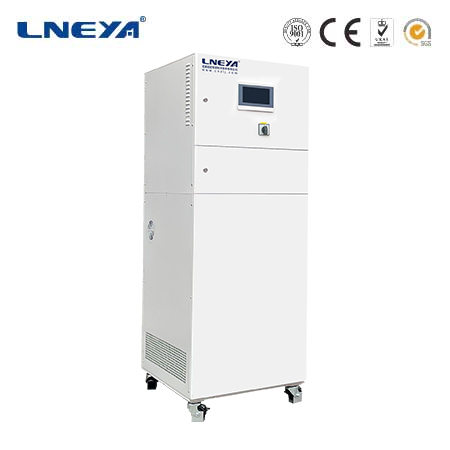
Types of Circulating Water Chillers
Air – Cooled Circulating Water Chillers
Advantages: Air – cooled circulating water chillers are relatively simple in design. They do not require a complex secondary water loop for heat rejection, which simplifies installation. This makes them a popular choice for smaller facilities or locations where access to a reliable water source for cooling is limited. They are also more compact in size compared to some water – cooled counterparts, making them suitable for areas with space constraints. Maintenance of air – cooled chillers can be less involved in terms of not having to deal with water – related issues like scale formation or water treatment.
Disadvantages: However, air – cooled chillers are generally less efficient than water – cooled ones, especially in hot and humid environments. High ambient air temperatures can severely impact their cooling capacity. In such conditions, the air – cooled chiller may struggle to maintain the required low temperatures for effective cooling, potentially leading to reduced performance of the equipment or processes being cooled.
Water – Cooled Circulating Water Chillers
Advantages: Water – cooled circulating water chillers offer higher efficiency due to the superior heat – transfer properties of water. Water has a much higher heat capacity than air, allowing it to absorb and transfer more heat per unit volume. This makes water – cooled chillers ideal for large – scale applications where a consistent and high – capacity cooling is essential. They can maintain a more stable cooling performance even in challenging environmental conditions. Additionally, water – cooled chillers are well – suited for applications where the waste heat can be effectively utilized, such as in some industrial processes where the heat from the secondary water loop can be repurposed.
Disadvantages: Water – cooled chillers are more complex systems as they require a secondary water loop. This adds to the installation cost and complexity, as well as the need for proper water treatment. The secondary water loop is prone to issues such as scale formation, corrosion, and biological growth if not properly maintained. These problems can reduce the efficiency of the chiller and may even cause damage to the equipment over time. Moreover, water – cooled chillers typically require more space for the installation of the cooling tower or other heat – rejection components.
Applications of Circulating Water Chillers
Industrial Applications
Manufacturing Processes: In manufacturing industries, precise temperature control is crucial for various processes. Circulating water chillers are used to cool process fluids. In a plastic injection molding plant, for example, they cool the molds to ensure consistent product quality. The circulating water chiller maintains a stable temperature, preventing the plastic from warping or developing defects during the molding process. In metalworking, the chillers cool cutting tools, reducing heat – related wear and tear and improving the accuracy of the machining operations.
Chemical and Pharmaceutical Industries: In the chemical and pharmaceutical industries, many reactions and processes require strict temperature control. Circulating water chillers are used to cool reactors, distillation columns, and storage tanks. In pharmaceutical manufacturing, they help maintain the correct temperature for drug synthesis and storage of temperature – sensitive medications. In chemical plants, they ensure that chemical reactions occur within the optimal temperature range, enhancing product yield and quality.
Data Centers
Server Cooling: Data centers house a large number of servers that generate a massive amount of heat. Circulating water chillers are used to cool the air in the data center, ensuring that the servers operate within the recommended temperature range. High – density data centers, in particular, rely on circulating water cooling systems to effectively remove the heat generated by the servers. The chilled water is typically circulated through air – side economizers or direct – expansion cooling units that cool the air before it enters the server racks. This helps in maintaining the reliability and performance of the servers, as overheating can lead to system failures, data loss, and reduced lifespan of the equipment.
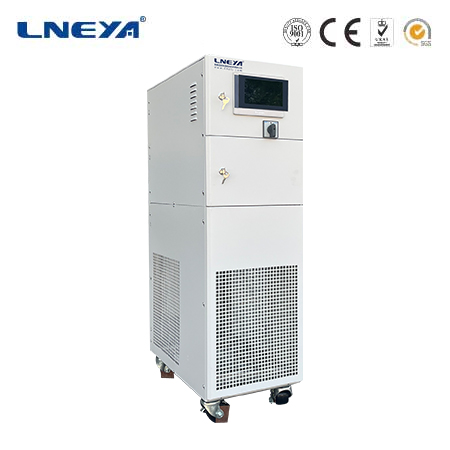
Food and Beverage Industry
Food Processing: In food processing plants, circulating water chillers are used for various purposes. They cool the water used in meat processing to prevent spoilage, and they control the temperature during the production of dairy products, such as cheese and yogurt. In the production of beverages like beer and soft drinks, the chillers are used to cool the product during bottling and storage, maintaining its quality and flavor.
Cold Storage: Cold storage facilities for food and beverages rely on circulating water chillers to maintain low temperatures. Whether it’s storing fresh produce, frozen foods, or perishable ingredients, the chillers ensure that the temperature remains within the appropriate range to prevent spoilage and extend the shelf – life of the products.
Installation, Maintenance, and Selection of Circulating Water Chillers
Installation
Location and Placement: When installing a circulating water chiller, the location is important. For air – cooled chillers, they should be placed in an area with good air circulation to facilitate heat dissipation. They should be away from heat – generating equipment and obstructions that could impede the flow of air. Water – cooled chillers need to be installed near a reliable water source, and the cooling tower should be placed in an area where it can effectively release heat into the atmosphere. In industrial settings, the chiller should be located close to the equipment or processes it will be cooling to minimize the length of the water pipes and reduce heat losses.
Plumbing and Electrical Connections: Proper plumbing connections are essential for circulating water chillers. The water inlet and outlet pipes should be correctly sized and connected to ensure a smooth flow of water. In water – cooled chillers, the secondary water loop also needs to be properly installed, with appropriate valves and fittings. Electrically, the chiller should be connected to a power source with the correct voltage and current rating. In industrial applications, where higher voltages may be involved, qualified electricians should handle the electrical installation to ensure safety and proper functioning.
Maintenance
Refrigerant Management: Regularly checking the refrigerant levels is crucial. Leaks in the refrigerant system can lead to reduced cooling capacity and increased energy consumption. Detection and repair of refrigerant leaks should be part of a routine maintenance schedule. Additionally, ensuring that the refrigerant used is environmentally friendly and compliant with relevant regulations is important.
Component Inspection: The compressor, condenser, evaporator, expansion valve, and other components of the chiller should be inspected regularly for signs of wear, damage, or blockages. Dirty condenser coils, for example, can significantly reduce the heat – transfer efficiency of the chiller. In air – cooled chillers, the fins of the condenser can accumulate dirt, dust, and debris over time, which restricts the air flow and reduces the cooling capacity. Regular cleaning of the condenser coils, either by mechanical means or using appropriate cleaning agents, is necessary to maintain optimal performance. The compressor, being the most critical component of the chiller, should also be checked for signs of abnormal vibration, noise, or increased energy consumption, which could indicate mechanical problems.
Water Treatment (for Water – Based Systems): In water – cooled circulating water chillers, proper water treatment is essential. Water treatment helps prevent scale formation, corrosion, and the growth of bacteria and algae in the water loops. Scale formation on the heat – transfer surfaces of the condenser or evaporator can act as an insulator, reducing the efficiency of heat transfer. Corrosion can damage the pipes and other components of the water loop, leading to leaks and costly repairs. Regular testing of the water quality and addition of appropriate water treatment chemicals, such as scale inhibitors, corrosion inhibitors, and biocides, are necessary to maintain the integrity of the system and ensure long – term efficient operation.
Selection
Cooling Capacity Requirements: The first step in selecting a circulating water chiller is to accurately determine the cooling capacity required. This involves calculating the amount of heat that needs to be removed from the process or equipment. Factors such as the type of process, the volume of water to be cooled, and the desired temperature drop need to be considered. In industrial applications, the cooling load may vary depending on the production rate and the specific requirements of the manufacturing process.
Type of Chiller: The choice between an air – cooled and water – cooled chiller depends on several factors. If water is scarce or expensive, or if space is limited, an air – cooled chiller may be a more suitable option. However, for large – scale applications with high cooling demands and where energy efficiency is a priority, a water – cooled chiller may be the better choice. The operating environment, such as ambient air temperature and humidity, also plays a role in the selection process.
Energy Efficiency: Energy – efficient chillers can significantly reduce operating costs over time. Look for chillers with high – efficiency ratings, such as the Energy Efficiency Ratio (EER) or the Coefficient of Performance (COP). Newer chiller models often incorporate advanced technologies to improve energy efficiency, such as variable – speed drives for the compressor and fans, which can adjust the operation of the chiller based on the actual cooling load.
Reliability and Serviceability: Consider the reliability of the chiller brand and the availability of spare parts and after – sales service. A reliable chiller will have fewer breakdowns, reducing downtime in industrial or data center applications. Good after – sales service ensures that any issues can be quickly resolved, minimizing the impact on the operation of the facility.
In conclusion, circulating water chillers are vital for maintaining proper temperature control in a wide range of applications. Their efficient operation, versatility, and ability to handle large cooling loads make them a preferred choice in industrial, data center, and food and beverage settings. Understanding their operation, types, applications, and maintenance requirements is key to ensuring their optimal performance and longevity.
Related recommendations
How to handle the malfunction of the evaporator chiller?
792How to handle the malfunction of the evaporator chiller? 1. Exhaust when the pressure is high. There may be a problem with heat dissipation. When the high and low pressure of the...
View detailsstorage chiller
215Introduction to Storage Chillers Storage chillers are essential in maintaining optimal temperatures for the storage of various products across different industries. These chillers are designed ...
View detailscirculation chiller
24Circulation ChillersCirculation chillers are integral components in systems where maintaining a controlled and cool temperature of a circulating fluid is of utmost importance. They are designed t...
View detailschilled glycol cooling system
241Chilled Glycol Cooling System: An Overview A chilled glycol cooling system is an industrial refrigeration setup that circulates a mixture of glycol and water to control and maintain specific te...
View details
HelloPlease log in