cooling chiller machine
Introduction to Cooling Chiller Machines
Cooling chiller machines are designed to remove heat from a process fluid, usually water or a water – glycol mixture, and transfer it to a secondary fluid or the environment. They play a vital role in numerous industries and applications where precise temperature control is essential. By maintaining a consistent low temperature, chillers help ensure the proper functioning of equipment, the quality of products, and the comfort of occupants in certain settings.
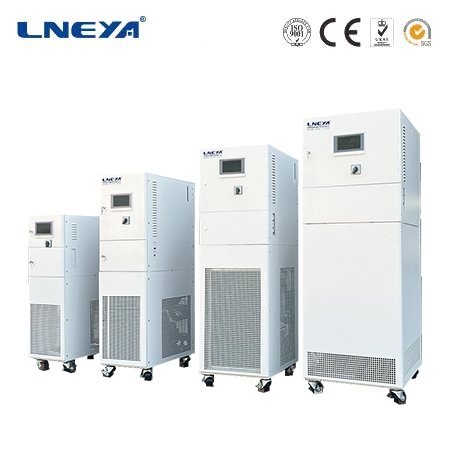
Working Principles
Vapor – Compression Cycle
Compression Stage
In a vapor – compression chiller, the cycle begins with a compressor. The compressor takes in low – pressure, low – temperature refrigerant vapor. As the compressor operates, it compresses the vapor, increasing both its pressure and temperature. This is similar to how a bicycle pump heats up air when it is compressed. For example, in a typical industrial chiller, a reciprocating or screw compressor might be used. The compressor forces the refrigerant through the system, initiating the heat – transfer process.
Condensation Stage
The hot, high – pressure refrigerant vapor then enters the condenser. In an air – cooled condenser, the refrigerant releases heat to the ambient air. Fans are used to enhance the heat – transfer process by blowing air over the condenser coils. In a water – cooled condenser, the refrigerant transfers heat to a water stream. As the refrigerant loses heat, it condenses into a high – pressure liquid. For instance, in a large – scale commercial building’s cooling system, a water – cooled condenser may be used to cool the refrigerant, with the heated water then being sent to a cooling tower for further cooling.
Expansion Stage
The high – pressure liquid refrigerant passes through an expansion valve. The expansion valve suddenly reduces the pressure of the refrigerant. This causes the refrigerant to expand and cool down significantly. It’s analogous to how a spray can gets cold when the liquid inside is suddenly released. The now – cold, low – pressure refrigerant is ready to absorb heat in the next stage.
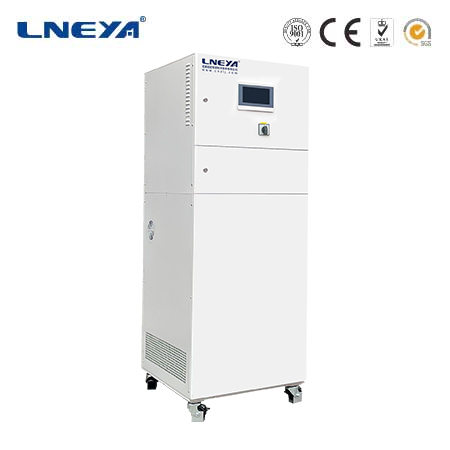
Evaporation Stage
The cold, low – pressure refrigerant enters the evaporator. Here, it comes into contact with the process fluid that needs to be cooled. The refrigerant absorbs heat from the process fluid, causing it to vaporize. In a manufacturing plant, for example, the process fluid (such as water used for cooling machinery) flows through the evaporator, and the refrigerant absorbs the heat from it, cooling the process fluid. The vaporized refrigerant then returns to the compressor to start the cycle again.
Absorption Cycle
Generator and Absorber
Absorption – type chillers operate on a different principle. They use a refrigerant (usually ammonia) and an absorbent (such as water or lithium bromide). Heat is applied to a generator. In the generator, the refrigerant – absorbent solution is heated, causing the refrigerant to separate from the absorbent. The refrigerant vapor then rises and enters the condenser.
In the absorber, the process is reversed. The refrigerant vapor that has passed through the condenser and become a liquid is absorbed back into the absorbent. This absorption process releases heat, which is removed by a cooling medium (usually water).
Condenser and Evaporator
Similar to vapor – compression chillers, the condenser in an absorption chiller cools and condenses the refrigerant vapor into a liquid. The cold, low – pressure refrigerant liquid then enters the evaporator. In the evaporator, it absorbs heat from the process fluid, just like in a vapor – compression chiller. The vaporized refrigerant then returns to the absorber to complete the cycle. Absorption – type chillers are often used in applications where waste heat or a low – grade heat source is available, such as in some industrial processes or in buildings with access to solar – generated heat.
Types of Cooling Chiller Machines
Air – Cooled Chillers
Operation and Design
Air – cooled chillers use ambient air as the cooling medium for the condenser. They consist of a compressor, an evaporator, and an air – cooled condenser. The hot refrigerant vapor from the compressor is directed to the condenser, where fans blow air over the condenser coils. The air absorbs the heat from the refrigerant, cooling it down and causing it to condense. The cold refrigerant then flows through the expansion valve and into the evaporator, where it cools the process fluid.
These chillers are relatively simple in design and do not require a complex water – supply infrastructure. They are often used in small – to – medium – sized applications where water conservation is a concern or where a water – cooling system is not feasible, such as in some rooftop installations.
Advantages and Disadvantages
Advantages: They are easy to install and maintain as they do not have water – related components like water – cooled chillers. They are also more portable in some cases. Air – cooled chillers are a good option in areas where water is scarce or expensive.
Disadvantages: Their cooling efficiency can be affected by high ambient air temperatures. In hot climates, the air may not be able to absorb as much heat from the refrigerant, reducing the overall cooling performance. They also tend to be noisier due to the operation of the fans.
Water – Cooled Chillers
Operation and Components
Water – cooled chillers use water as the cooling medium for the condenser. They typically have a compressor, an evaporator, and a water – cooled condenser. The hot refrigerant vapor from the compressor enters the condenser, where it transfers heat to the water flowing through the condenser coils. The heated water is then usually sent to a cooling tower, where it releases heat to the atmosphere and cools down before being recirculated through the condenser.
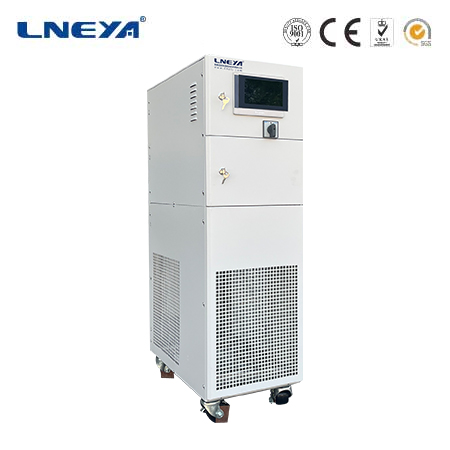
Water – cooled chillers are available in different configurations, such as shell – and – tube and plate – type heat exchanger designs. Shell – and – tube chillers have a shell with a bundle of tubes inside. The refrigerant is usually on the shell – side, while the water (both the process water and the cooling water) flows through the tubes. Plate – type heat exchanger chillers use a series of thin, corrugated metal plates to transfer heat between the refrigerant and the water.
Benefits and Drawbacks
Benefits: Water – cooled chillers are generally more efficient than air – cooled chillers, especially in hot and humid environments. Water has a higher heat – capacity than air, allowing it to absorb more heat per unit volume. They also tend to operate more quietly as they do not rely on large fans for heat dissipation.
Drawbacks: They require a reliable water source and a system for treating and disposing of the heated water. There is also a risk of water – related issues such as leaks, corrosion, and scale formation in the condenser coils, which can affect the chiller’s performance and lifespan.
Absorption – Type Chillers
Unique Features and Operation
As mentioned earlier, absorption – type chillers use a refrigerant – absorbent pair and heat input to operate. They are unique in that they can use low – grade heat sources, such as waste heat from industrial processes, solar – heated water, or even natural gas combustion heat. This makes them an attractive option in applications where energy efficiency and the use of alternative energy sources are important.
The operation of absorption – type chillers involves the separation and absorption of the refrigerant, as well as the heat – transfer processes in the condenser and evaporator. The control of the heat input and the flow of the refrigerant – absorbent solution is crucial for the proper functioning of these chillers.
Suitability and Considerations
Suitability: They are suitable for applications where electricity is scarce or expensive, but a heat source is available. They can also be used in environmentally – sensitive areas as they may use more natural refrigerants and consume less electricity compared to vapor – compression chillers. Absorption – type chillers are often used in large – scale commercial buildings, hospitals, and some industrial facilities.
Considerations: They are generally more complex in design and require careful control of the heat source and the absorption process. The initial cost of installation can be higher, and they may have a lower cooling capacity compared to some vapor – compression systems, especially in smaller sizes.
Applications of Cooling Chiller Machines
Manufacturing Industry
Plastic Manufacturing
In plastic injection molding, cooling chiller machines are essential. The hot plastic injected into the molds needs to be cooled rapidly to solidify into the desired shape. Chillers provide the necessary cold water or coolant to cool the molds. Precise temperature control is crucial to ensure the dimensional accuracy and quality of the plastic products. If the cooling process is not properly regulated, the plastic may warp or have other defects.
In plastic extrusion, chillers are also used. The extruded plastic needs to be cooled to set its shape. The cooling rate can affect the physical properties of the plastic, such as its strength and flexibility. Chillers help in maintaining a consistent cooling rate, resulting in high – quality plastic products.
Metalworking
In metalworking processes like machining and metal casting, chillers are used to cool cutting tools and the metal workpieces. In machining, the cutting tools generate heat due to friction with the metal. Cooling the tools with chilled water or coolant helps in extending their lifespan by reducing wear and tear. It also improves the surface finish of the machined parts.
In metal casting, chillers are used to control the solidification rate of the molten metal. By cooling the molds or the metal itself at a specific rate, the grain structure of the cast metal can be optimized, leading to stronger and more reliable metal components.
Food and Beverage Industry
Brewing
In the brewing industry, chillers play a crucial role at various stages. During fermentation, yeast generates heat as it consumes sugars to produce alcohol. Chillers are used to maintain the optimal fermentation temperature, which is essential for the flavor and quality of the beer. Different strains of yeast have different optimal temperature ranges, and chillers help in keeping the temperature within these ranges.
After fermentation, the beer is often cooled to a lower temperature for conditioning and storage. Chillers are used to achieve and maintain these low temperatures, which helps in clarifying the beer and improving its stability.
Dairy Production
In dairy plants, chillers are used to cool milk immediately after collection. This helps in preventing spoilage and maintaining the freshness of the milk. The chilled milk can then be further processed or stored. In the production of dairy products like ice cream, chillers are used to cool the mixture during the freezing process to achieve the desired texture and consistency.
Chillers are also used in the storage of dairy products. Refrigerated display cases and storage rooms rely on chillers to maintain the low temperatures required to keep dairy products fresh and safe for consumption.
Data Centers
Heat Dissipation
Data centers generate a significant amount of heat due to the continuous operation of servers and other electronic equipment. Cooling chiller machines are used to remove this heat and keep the servers at a safe operating temperature. High – efficiency chillers are crucial in data centers to prevent hardware failures and data loss.
The heat generated by servers can cause the components to overheat, leading to reduced performance and potential damage. Chillers help in maintaining a stable temperature environment, ensuring the reliable operation of the data center. Some data centers also use free – cooling techniques in combination with chillers. Free – cooling involves using outside air or other natural cooling sources when the temperature is suitable, reducing the load on the chillers and saving energy.
Maintenance of Cooling Chiller Machines
Refrigerant Management
Refrigerant Level Checks
Regularly checking the refrigerant level in a chiller is essential. A low refrigerant level can indicate a leak in the system. If the refrigerant level is low, the cooling capacity of the chiller will be reduced. A professional technician should be called to identify and repair the leak. Once the leak is fixed, the refrigerant can be recharged to the proper level.
Different types of chillers use different refrigerants, and it’s important to use the correct refrigerant specified by the manufacturer. Using the wrong refrigerant can not only affect the performance of the chiller but also violate environmental regulations.
Refrigerant Quality Monitoring
In addition to level checks, the quality of the refrigerant should be monitored. Over time, the refrigerant can become contaminated with moisture, non – condensable gases, or other impurities. These contaminants can reduce the efficiency of the chiller and cause damage to the components. Refrigerant quality can be checked using specialized testing equipment, and if necessary, the refrigerant can be purified or replaced.
Component Inspections
Compressor Inspection
The compressor is a critical component of a chiller. Regular inspections should be carried out to check for signs of wear, such as unusual noises or vibrations. The oil level in the compressor should also be monitored and changed according to the manufacturer’s recommendations. A well – maintained compressor is essential for the efficient operation of the chiller.
If the compressor is not functioning properly, it can lead to reduced cooling capacity, increased energy consumption, or even complete system failure. Visual inspections can be complemented by using diagnostic tools to check the electrical components and mechanical parts of the compressor.
Heat Exchanger Inspection
Both the condenser and evaporator heat exchangers should be inspected regularly. In air – cooled condensers, the coils should be checked for dirt, dust, and debris accumulation. These can reduce the air flow and heat – transfer efficiency. Cleaning the coils with a brush or compressed air can improve the performance of the condenser.
In water – cooled condensers and evaporators, the tubes or plates should be inspected for leaks, corrosion, and scale formation. Scale can act as an insulator, reducing the heat – transfer efficiency. Regular cleaning using appropriate cleaning agents can prevent scale build – up. If there are leaks in the heat exchanger, they should be repaired promptly to avoid refrigerant loss and reduced cooling performance.
Water Quality Control (for Water – Cooled Chillers)
Scale and Corrosion Control
In water – cooled chillers, the quality of the water is of utmost importance. Water with high mineral content can cause scale formation on the heat exchanger surfaces. Scale acts as an insulator, reducing the heat – transfer efficiency of the chiller. To prevent scale formation, water treatment chemicals such as anti – scale agents are added to the water. Additionally, the water may need to be softened to reduce the mineral content.
Corrosion is also a concern, especially if the water contains dissolved oxygen or other corrosive substances. Corrosion inhibitors are added to the water to protect the metal components of the chiller from rust and degradation. Regular water testing is necessary to monitor the water quality and ensure that the treatment chemicals are at the appropriate levels.
Biological Growth Prevention
The warm, moist environment in a water – cooled chiller can promote the growth of bacteria, algae, and other microorganisms. These organisms can clog the heat exchanger channels and reduce the water flow, as well as cause corrosion. To prevent biological growth, biocides are added to the water. Regular cleaning of the cooling tower (if applicable) and the water distribution system can also help in preventing the build – up of biological contaminants.
Choosing the Right Cooling Chiller Machine
Cooling Capacity Requirements
Calculating Load
The first step in choosing a cooling chiller machine is to calculate the cooling load. The cooling load is the amount of heat that needs to be removed from the process fluid or the space to be cooled. It depends on factors such as the size of the area, the heat generated by equipment, the number of occupants (in some cases), and the desired temperature.
For industrial applications, the heat generated by machinery, production processes, and lighting needs to be considered. In a data center, the heat generated by servers, power supplies, and other electronic equipment is a major factor in determining the cooling load. There are various methods and formulas available to calculate the cooling load accurately.
Sizing the Chiller
Once the cooling load is determined, the chiller should be sized accordingly. It’s important to choose a chiller with a cooling capacity that can meet or slightly exceed the calculated load. If the chiller is undersized, it will not be able to cool the process fluid or space effectively, leading to overheating and reduced performance. On the other hand, if the chiller is oversized, it may cycle on and off frequently, reducing its efficiency and lifespan.
Energy Efficiency
Efficiency Ratings
Look for chillers with high energy – efficiency ratings. In many countries, there are energy – efficiency standards and ratings for chillers, such as the Energy Efficiency Ratio (EER) and the Coefficient of Performance (COP). The EER is the ratio of the cooling capacity of the chiller (in British Thermal Units per hour – Btu/h) to the electrical power input (in watts) at a specific operating condition. The COP is a similar measure but is often used for chillers operating under different conditions.
Higher EER and COP values indicate more energy – efficient chillers. Energy – efficient chillers can save significant amounts of energy over their lifespan, reducing operating costs. Some advanced chillers also have features like variable – speed drives, which can adjust the speed of the compressor and other components based on the cooling load, further improving energy efficiency.
Related recommendations
temperature chiller
206Understanding Temperature Chillers Temperature chillers are mechanical devices designed to remove heat from a fluid, maintaining a desired temperature for various applications. They are widely ...
View detailslaboratory water heater
125Introduction to Laboratory Water HeatersLaboratory water heaters, commonly known as water baths, are crucial for providing a stable temperature environment in scientific laboratories. They are use...
View detailstemp chamber
166Temperature chambers, often referred to as thermal chambers, are specialized enclosures designed to create controlled thermal environments. These chambers enable precise temperature simulations ra...
View detailssmall chiller price
165Small Chiller Price Overview Small chillers are essential in various applications, from commercial to industrial settings, providing precise temperature control. The price of these chillers is ...
View details
HelloPlease log in