efficient chillers
Introduction
In an era where energy conservation and sustainability are at the forefront, the demand for efficient chillers has never been higher. Chillers are integral to numerous industries, from commercial buildings and data centers to manufacturing plants, as they provide the necessary cooling for comfort, equipment operation, and process control. Efficient chillers not only reduce energy consumption and operational costs but also contribute to a lower environmental impact by minimizing greenhouse gas emissions. This article aims to provide a detailed overview of what makes chillers efficient, the technologies and design features involved, and how to select, operate, and maintain them for optimal performance.
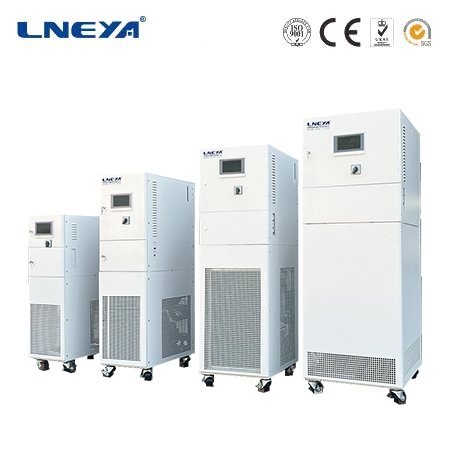
Key Factors Contributing to Chiller Efficiency
Energy – Saving Technologies
Variable – Speed Drives: One of the most significant advancements in chiller efficiency is the use of variable – speed drives (VSDs). VSDs control the speed of the compressor, fans, and pumps in the chiller system. By adjusting the speed based on the cooling demand, VSDs prevent the equipment from running at full capacity when not needed. For example, during periods of low cooling load, such as at night or on weekends, the compressor speed can be reduced, resulting in substantial energy savings. VSDs can also optimize the start – stop process, reducing electrical surges and wear on the components, further enhancing the overall efficiency and lifespan of the chiller.
High – Efficiency Heat Exchangers: The performance of heat exchangers, including condensers and evaporators, greatly impacts chiller efficiency. Advanced heat exchanger designs, such as enhanced – tube and microchannel heat exchangers, maximize the surface area for heat transfer while minimizing pressure drops. Enhanced – tube heat exchangers feature fins or grooves on the tube surface, increasing the contact area with the refrigerant and the cooling medium (air or water). Microchannel heat exchangers, on the other hand, use a series of small channels to improve heat transfer efficiency and reduce refrigerant charge requirements. These high – efficiency heat exchangers enable better heat exchange, allowing the chiller to operate more effectively with less energy consumption.
Smart Control Systems: Modern efficient chillers are equipped with sophisticated smart control systems. These systems use sensors to monitor various operational parameters, such as temperature, pressure, and refrigerant flow, in real – time. Based on the data collected, the control system can optimize the chiller’s operation. For instance, it can adjust the refrigerant flow rate to maintain the ideal temperature in the evaporator, or coordinate the operation of multiple chillers in a system to ensure the most efficient load distribution. Some smart control systems also integrate with building management systems (BMS), enabling centralized control and optimization of the entire building’s cooling and energy usage.
Refrigerant Management
Optimized Refrigerant Charge: The amount of refrigerant in a chiller system is crucial for its efficiency. An improper refrigerant charge, either too much or too little, can lead to reduced performance and increased energy consumption. A low refrigerant charge may cause the compressor to work harder to maintain the desired cooling effect, while an overcharged system can result in higher pressure and reduced heat transfer efficiency. Regular refrigerant level checks and adjustments, based on the manufacturer’s specifications, are essential to ensure optimal performance. Additionally, using high – performance refrigerants with good thermodynamic properties can contribute to better efficiency. For example, some newer refrigerants have lower global warming potential (GWP) and higher coefficient of performance (COP), making them more environmentally friendly and energy – efficient.
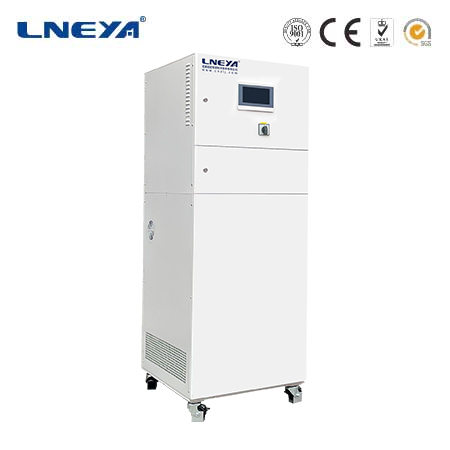
Refrigerant Leak Prevention and Detection: Refrigerant leaks not only lead to a loss of cooling capacity but also have a negative environmental impact and can increase operating costs. Efficient chillers incorporate leak – prevention measures, such as high – quality seals and gaskets, and advanced leak – detection systems. Regular inspections for refrigerant leaks, especially in areas prone to leakage like joints and connections, should be part of the maintenance routine. Early detection of leaks allows for prompt repair, minimizing refrigerant loss and ensuring the chiller operates at peak efficiency.
System Design and Integration
Proper Sizing and Matching: Selecting the right – sized chiller for the application is fundamental to efficiency. An oversized chiller will frequently cycle on and off, wasting energy during the start – up process and leading to increased wear on components. On the other hand, an undersized chiller will struggle to meet the cooling demand, operating continuously at maximum capacity and consuming more energy. In addition to sizing the chiller correctly, ensuring that all components, such as pumps, fans, and heat exchangers, are properly matched to the chiller’s capacity is essential. This harmonious integration of components allows for smooth operation and optimal energy utilization.
Thermal Insulation: Adequate thermal insulation in the chiller system helps minimize heat losses. Insulating refrigerant pipes, tanks, and other components reduces the amount of heat that the chiller has to remove from the system, thereby reducing the workload and energy consumption. High – quality insulation materials, such as fiberglass, polyurethane foam, or mineral wool, are commonly used. Good insulation also helps maintain the temperature of the refrigerant, ensuring more consistent and efficient operation.
Types of Efficient Chillers
Air – Cooled Efficient Chillers
Design and Features: Air – cooled chillers are popular due to their ease of installation and minimal requirement for a complex water – cooling infrastructure. Modern efficient air – cooled chillers feature high – efficiency fans with variable – speed controls to adjust the air flow based on the cooling load. They also incorporate advanced fin – and – tube heat exchanger designs with enhanced surface areas for better heat transfer. Some models are equipped with dual – circuit compressors, which can operate independently or in combination, allowing for more precise control of the cooling capacity and improved energy efficiency under varying load conditions.
Advantages and Limitations: The main advantage of air – cooled efficient chillers is their simplicity and flexibility. They can be easily installed in outdoor locations, making them suitable for retrofit projects or applications where water – cooling is not feasible. However, their efficiency can be affected by ambient air conditions. In hot and humid environments, the performance of air – cooled chillers may decline as the temperature difference between the refrigerant and the air decreases, requiring the compressor to work harder. Additionally, the fans in air – cooled chillers can generate noise, which may be a concern in some settings.
Water – Cooled Efficient Chillers
Design and Features: Water – cooled chillers generally offer higher efficiency compared to air – cooled models. They use a secondary water source, typically from a cooling tower, to remove heat from the refrigerant in the condenser. Efficient water – cooled chillers often feature high – efficiency condensers with optimized tube arrangements and advanced water – side heat – transfer enhancements. Variable – speed pumps are commonly used to control the water flow rate, ensuring that the chiller operates at the most efficient point. Some water – cooled chillers also incorporate heat – recovery systems, which capture and reuse the heat rejected by the chiller for other purposes, such as heating domestic water or pre – heating process fluids, further increasing the overall efficiency of the system.
Advantages and Limitations: The primary advantage of water – cooled efficient chillers is their higher cooling capacity and better performance in hot environments. Water has a higher heat – carrying capacity than air, allowing for more effective heat rejection. However, water – cooled chillers require a more complex infrastructure, including cooling towers, pumps, and water – treatment systems. The maintenance of these additional components can be more involved and costly. There is also a risk of water – related issues, such as scaling, corrosion, and biological growth, which can affect the performance and lifespan of the chiller if not properly managed.
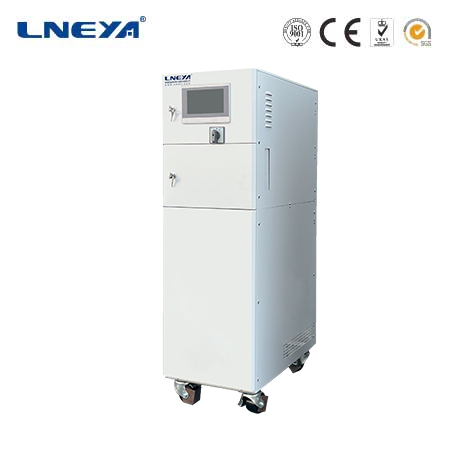
Absorption Efficient Chillers
Design and Features: Absorption chillers operate on a different principle compared to compression – based chillers. They use a heat source, such as steam, hot water, or natural gas, instead of electricity to drive the refrigeration cycle. Efficient absorption chillers feature advanced absorber and generator designs that optimize the absorption and desorption processes of the refrigerant – absorbent solution. They often incorporate heat – recovery mechanisms within the system to maximize the utilization of the heat source. Some models also have intelligent control systems that adjust the operation of the chiller based on the available heat source and the cooling demand, ensuring efficient operation.
Advantages and Limitations: The main advantage of absorption chillers is their ability to use waste heat or low – cost heat sources, making them an attractive option in industries where such heat is available, such as power plants or manufacturing facilities. They also have a lower electrical demand compared to compression – based chillers, which can be beneficial in areas with high electricity costs or limited electrical capacity. However, absorption chillers have a lower coefficient of performance (COP) compared to modern compression – based chillers, meaning they require more heat input to produce the same amount of cooling. They also require more complex maintenance due to the handling of the refrigerant – absorbent solution and the need to manage the heat – source system.
Applications of Efficient Chillers
Commercial Buildings
Office Buildings: In office buildings, efficient chillers are essential for maintaining a comfortable indoor environment for occupants. They cool the air – conditioning systems, providing conditioned air to offices, meeting rooms, and common areas. Smart control systems in these chillers can adjust the cooling output based on occupancy patterns, time of day, and outdoor temperature, ensuring energy savings without sacrificing comfort. Additionally, the integration of efficient chillers with other building systems, such as ventilation and lighting, through a BMS allows for comprehensive energy management and optimization.
Hotels and Resorts: Hotels and resorts rely on efficient chillers to cool guest rooms, restaurants, spas, and other facilities. Energy – efficient chillers not only reduce operating costs but also contribute to a more sustainable operation, which is increasingly important to environmentally conscious guests. Some hotels use heat – recovery chillers to provide hot water for guest use, further enhancing the energy efficiency of the overall system. The quiet operation of certain efficient chiller models is also crucial in hotel settings to ensure a peaceful environment for guests.
Industrial Applications
Manufacturing Plants: In manufacturing, efficient chillers play a vital role in cooling various processes and equipment. For example, in metalworking, they cool cutting tools and machinery to prevent overheating and extend their lifespan. In the food and beverage industry, chillers are used for cooling food products during processing, storage, and transportation. Efficient chillers with precise temperature control capabilities are essential in pharmaceutical manufacturing to ensure the quality and stability of drugs. The ability to operate efficiently under varying load conditions is particularly important in industrial settings, where the cooling demand can fluctuate significantly throughout the production cycle.
Data Centers: Data centers require a constant supply of cool air to maintain the optimal operating temperature of servers and other IT equipment. Efficient chillers are critical for data center operations, as they consume a significant portion of the facility’s energy. High – efficiency chillers with advanced control systems can precisely match the cooling demand, reducing energy waste. Some data centers also use free – cooling techniques in conjunction with efficient chillers, where outside air is used to cool the data center during cooler months, further enhancing energy savings.
Selecting Efficient Chillers
Cooling Capacity Requirements
Calculation Methods: Determining the appropriate cooling capacity of a chiller is the first step in the selection process. The cooling capacity is usually measured in tons of refrigeration (TR) or kilowatts (kW). To calculate the required cooling capacity, factors such as the size of the area to be cooled, the number of heat – generating devices, the occupancy rate, and the ambient temperature need to be considered. Different calculation methods, such as the load calculation method based on the heat gain from the building envelope, internal loads (lights, equipment, people), and ventilation requirements, can be used. It’s important to account for peak cooling loads and potential future growth when sizing the chiller to ensure it can meet the cooling demand effectively.
Load Variation Consideration: In addition to the peak cooling load, understanding the load variation throughout the year is crucial. Some applications may have significant seasonal or daily fluctuations in cooling demand. Selecting a chiller with variable – capacity control, such as a chiller with a variable – speed compressor or multiple compressors that can be staged on and off, allows the chiller to operate efficiently at different load levels. This helps avoid the inefficiencies associated with oversized chillers running at partial load or undersized chillers struggling to meet the demand.
Energy – Efficiency Ratings
Industry Standards and Certifications: Look for chillers that meet or exceed industry – recognized energy – efficiency standards. Certifications such as Energy Star (in the United States) or the European Union’s Ecodesign directive provide a benchmark for energy – efficient products. These certifications ensure that the chiller has been tested and meets specific energy – efficiency criteria. Chillers with higher energy – efficiency ratings typically consume less electricity, resulting in lower operating costs over the long term. Additionally, some regions offer incentives or rebates for the installation of energy – efficient chillers, making them even more cost – effective.
Coefficient of Performance (COP) and Energy – Efficiency Ratio (EER): The COP and EER are important metrics for evaluating the energy efficiency of chillers. The COP is the ratio of the cooling output to the energy input at a specific operating condition, while the EER is a similar ratio but measured under different test conditions. A higher COP or EER indicates a more energy – efficient chiller. When comparing different chiller models, it’s important to consider these metrics along with the actual operating conditions of the application, as the efficiency of a chiller can vary depending on factors such as the ambient temperature, load profile, and refrigerant type.
Cost – Benefit Analysis
Initial Purchase Cost: The upfront cost of the chiller is an important consideration, but it should not be the sole determining factor. While more energy – efficient chillers may have a higher initial purchase price, they can offer significant savings in operating costs over their lifespan. It’s important to compare the purchase prices of different chiller models along with their energy – efficiency ratings and expected operating costs. A cost – benefit analysis can help determine the payback period, which is the time it takes for the energy savings to offset the additional upfront cost of the more efficient chiller.
Long – Term Operating and Maintenance Costs: In addition to the initial purchase cost, consider the long – term operating and maintenance costs of the chiller. Energy – efficient chillers typically have lower electricity consumption, reducing the ongoing operating costs. However, some advanced features, such as variable – speed drives or complex control systems, may require more specialized maintenance. It’s important to factor in the cost of regular maintenance, including component replacement, refrigerant recharge, and system cleaning, as well as any potential repair costs over the chiller’s lifespan. Choosing a chiller from a reputable manufacturer with a good track record for reliability and ease of maintenance can help minimize these costs.
Maintenance for Sustained Efficiency
Regular Inspections
Component Checks: Regularly inspect all the components of the chiller, including the compressor, condenser, evaporator, expansion valve, fans, and pumps. Look for signs of wear, damage, leaks, or abnormal vibrations. Check the refrigerant lines for any signs of corrosion or leakage, and inspect the electrical connections for tightness and signs of overheating. Cleaning the condenser and evaporator coils regularly to remove dirt, debris, and dust is essential for maintaining optimal heat – transfer efficiency. A dirty coil can reduce the chiller’s performance and increase energy consumption.
Lubrication and Fluid Checks: For compressors and other moving parts, check the lubrication levels and the condition of the lubricating oil. Replace the oil according to the manufacturer’s recommendations to ensure smooth operation and prevent excessive wear. In water – cooled chillers, monitor the water quality, including the pH level, hardness, and chlorine content. Add the necessary water – treatment chemicals to prevent scaling, corrosion, and the growth of microorganisms in the water – cooling system. Regularly check the water flow rate and pressure to ensure proper operation of the pumps and heat exchangers.
Performance Monitoring and Optimization
Data Collection and Analysis: Continuously monitor the chiller’s performance by collecting data on operational parameters such as temperature, pressure, refrigerant flow, and energy consumption. Analyzing this data can help identify trends and potential issues early. For example, a gradual increase in compressor power consumption may indicate a problem with the refrigerant charge or a malfunctioning component. Some advanced chiller control systems can automatically collect and analyze data, providing real – time insights and alerts to operators.
System Tuning and Adjustment: Based on the performance data analysis, make necessary adjustments to the chiller system. This may include adjusting the refrigerant flow rate, optimizing the fan or pump speed, or calibrating the temperature sensors. Regularly tuning the chiller can help maintain its efficiency and ensure it operates at the optimal point under different load conditions. Additionally, consider retrofitting the chiller with energy – saving upgrades, such as installing variable – speed drives or upgrading the control system, to further enhance its performance over time.
Related recommendations
portable heater temperature control
220Portable Heater Temperature Control: Ensuring Comfort and Safety Portable heaters are widely used in homes, offices, workshops, and other settings where localized heating is required. Effective...
View detailschiller 300 tr
172Understanding Chiller 300 TR A chiller with a capacity of 300 tons of refrigeration (TR) is a significant piece of equipment used in various industries for cooling purposes. It operates on the ...
View detailsindustrial process cooling
104Industrial Process Cooling: A Comprehensive GuideI. IntroductionIndustrial process cooling refers to the set of techniques and systems employed to remove heat generated during various industrial m...
View detailsWhat are the steps for stopping a small water chiller?
802What are the steps for stopping a small water chiller? Stop the small chiller and enter normal shutdown, emergency shutdown, automatic shutdown, and long-term shutdown stop modes. ...
View details
HelloPlease log in