evaporative chillers
Evaporative Chillers: A Comprehensive Guide
Introduction
In the quest for sustainable and cost – effective cooling solutions, evaporative chillers have emerged as a popular option. These chillers utilize the basic principle of water evaporation, which is a natural and energy – efficient process. By harnessing this principle, evaporative chillers are able to provide cooling in a wide range of applications, from maintaining comfortable indoor environments in commercial buildings to supporting industrial processes. Their operation is based on the fact that when water evaporates, it absorbs heat from its surroundings, thereby reducing the temperature of the air or other substances in contact with it.
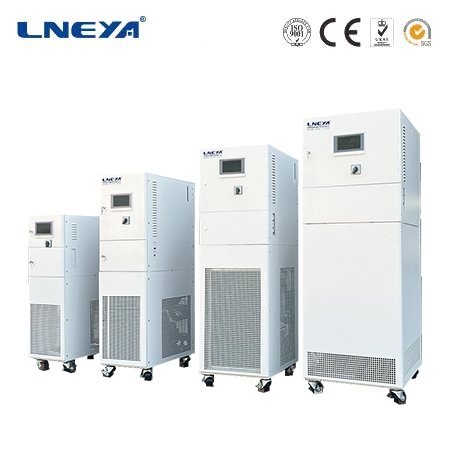
Working Principles of Evaporative Chillers
The Evaporation Process
Heat Absorption during Evaporation: At the heart of an evaporative chiller’s operation is the evaporation of water. When water changes its state from liquid to vapor, it requires energy in the form of heat. This heat is drawn from the surrounding air or the medium with which the water is in contact. In an evaporative chiller, warm air is made to pass over a surface that is saturated with water, such as a wet pad or through a fine water spray. As the air moves across this water – laden surface, the water molecules gain enough energy to evaporate. The energy for this evaporation is sourced from the sensible heat of the air, which causes the air temperature to drop.
Role of Latent Heat of Vaporization: The latent heat of vaporization of water is a crucial factor in the operation of evaporative chillers. It represents the amount of heat energy required to convert a unit mass of water from a liquid to a vapor at a constant temperature. For water, this value is relatively high, meaning that a significant amount of heat can be absorbed during the evaporation process. This property allows evaporative chillers to achieve substantial cooling effects. As the water evaporates, it continuously absorbs heat from the air, resulting in a cooler air stream.
Direct and Indirect Evaporative Cooling
Direct Evaporative Cooling: In direct evaporative cooling systems, the warm air is directly exposed to the water. This can be achieved through the use of wet – pad evaporative coolers. The warm air is forced to pass through pads that are constantly saturated with water. As the air moves through the pads, water evaporates into the air, cooling it. The cooled air is then directly circulated into the space or process that requires cooling. For example, in a greenhouse, direct evaporative coolers can be used to lower the temperature inside. The simplicity of this system makes it cost – effective and easy to install. However, it also has limitations. Since the cooled air has a higher humidity level due to the evaporation process, direct evaporative cooling is most effective in dry climates where the ambient air can readily absorb the additional moisture.
Indirect Evaporative Cooling: Indirect evaporative cooling systems use a heat exchanger to separate the air being cooled from the water evaporation process. The warm air passes through one side of the heat exchanger, while on the other side, a separate air stream or water is cooled by evaporation. The heat from the warm air is transferred through the heat exchanger to the evaporating medium, which cools the air or water on the other side. This cooled air or water can then be used to cool the primary air stream without adding moisture to it. For instance, in a data center, indirect evaporative chillers can be used to cool the air around the servers. The advantage of this system is that it can be used in a wider range of climates, as it allows for better control over the humidity of the cooled air.
Types of Evaporative Chillers
Direct Evaporative Chillers
Wet – Pad Evaporative Coolers: Wet – pad evaporative coolers are one of the most common types of direct evaporative chillers. They consist of a housing that contains water – saturated pads, a fan to draw in warm air, and a water distribution system to keep the pads wet. The pads are typically made of materials such as cellulose or synthetic fibers that have a high surface area and can retain water well. As the fan blows warm air through the pads, water evaporates, cooling the air. These coolers are relatively inexpensive to purchase and operate, making them suitable for small – to – medium – sized applications, such as residential homes, small offices, and some agricultural buildings.
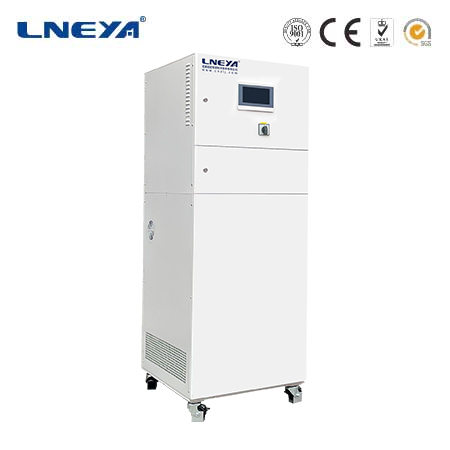
Spray – Type Evaporative Chillers: Spray – type evaporative chillers use a system of nozzles to spray water into the air stream. The water is atomized into fine droplets, which increases the surface area for evaporation. As the warm air passes through the water spray, the water evaporates, cooling the air. This type of chiller can be more effective in cooling large volumes of air compared to wet – pad coolers. They are often used in industrial settings, such as factories and warehouses, where a significant amount of air needs to be cooled. However, they may require more maintenance as the nozzles can become clogged if the water quality is poor.
Indirect Evaporative Chillers
Air – to – Air Indirect Evaporative Chillers: Air – to – air indirect evaporative chillers use a heat exchanger to transfer heat between two air streams. One air stream is the warm air that needs to be cooled, and the other is a separate air stream that is used for the evaporation process. The warm air passes through one side of the heat exchanger, while the evaporative air stream, which is in contact with water, passes through the other side. The heat from the warm air is transferred to the evaporative air stream, cooling the warm air without adding moisture to it. These chillers are suitable for applications where humidity control is important, such as in data centers, hospitals, and some manufacturing processes.
Water – to – Air Indirect Evaporative Chillers: Water – to – air indirect evaporative chillers use water as the intermediate cooling medium. The warm air passes through a heat exchanger, and on the other side of the heat exchanger, water is cooled by evaporation. The cooled water is then used to cool the air through a secondary heat exchanger. This type of chiller can be more efficient in terms of heat transfer and can be used in a variety of applications, including commercial buildings and industrial processes. It also allows for better control over the temperature of the cooled air.
Applications of Evaporative Chillers
Commercial Buildings
Office Buildings: In office buildings, evaporative chillers can be used to provide cooling for the occupied spaces. In regions with dry climates, direct evaporative coolers can be installed to cool the air in individual offices or open – plan work areas. They offer a cost – effective and energy – efficient alternative to traditional air – conditioning systems. In more humid climates, indirect evaporative chillers can be integrated into the building’s HVAC system. These chillers can pre – cool the incoming air, reducing the load on the main air – conditioning units and saving energy.
Retail Spaces: Retail spaces, such as shopping malls and department stores, can also benefit from evaporative chillers. In large retail areas, direct evaporative coolers can be used to create a comfortable shopping environment, especially in areas with high foot traffic. Indirect evaporative chillers can be used in the back – of – house areas, such as storage rooms and staff break rooms, to provide cooling without adding humidity, which could damage inventory or affect the comfort of employees.
Industrial Settings
Manufacturing Plants: Manufacturing plants often have specific temperature and humidity requirements for their production processes. Evaporative chillers can be used to cool equipment, control the temperature in production areas, and maintain the quality of products. For example, in a food and beverage manufacturing plant, evaporative chillers can be used to cool the product during processing and storage. In a textile manufacturing plant, the humidity – control capabilities of indirect evaporative chillers can be used to ensure the proper handling of delicate fabrics.
Warehouses: Warehouses typically require large – scale cooling to protect stored goods from heat damage. Direct evaporative chillers can be used to cool the air in the warehouse, reducing the temperature and preventing spoilage of perishable items. Indirect evaporative chillers can also be used, especially in warehouses where humidity control is crucial, such as those storing electronics or sensitive materials.
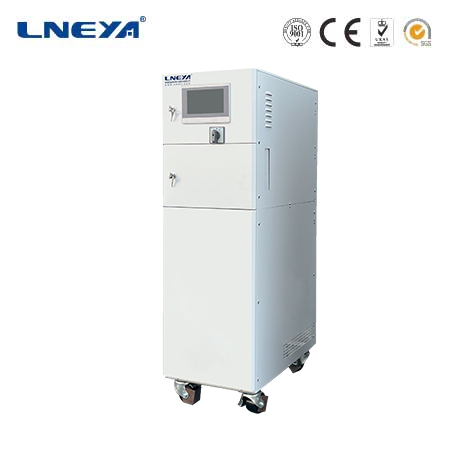
Agricultural Facilities
Greenhouses: Greenhouses need to maintain a suitable temperature and humidity environment for plant growth. Evaporative chillers are widely used in greenhouses to control the temperature. Direct evaporative coolers can be used to lower the temperature inside the greenhouse, providing a more comfortable environment for plants. The increased humidity from the evaporation process can also be beneficial for some plants. Indirect evaporative chillers can be used in greenhouses where precise humidity control is required, such as in the cultivation of certain high – value crops.
Livestock Facilities: In livestock facilities, evaporative chillers can be used to keep animals cool. In hot climates, direct evaporative coolers can be installed in barns to reduce the temperature and improve the comfort of livestock. This can lead to better animal health and productivity. Indirect evaporative chillers can also be used to provide a more controlled cooling environment, especially in areas where humidity management is important for the well – being of the animals.
Advantages of Evaporative Chillers
Energy Efficiency
Lower Power Consumption: Evaporative chillers generally consume less energy compared to traditional compression – based air – conditioning systems. The evaporation process is a natural and energy – efficient way of cooling. In direct evaporative cooling, the only energy required is to operate the fan that moves the air through the system. In indirect evaporative cooling, while there may be additional components such as pumps and fans for the heat – exchanger and evaporation processes, the overall energy consumption is still significantly lower than that of traditional air – conditioners. This energy efficiency can lead to substantial cost savings on electricity bills, especially in applications where the cooling system operates for long periods.
Reduced Compressor Use (in Indirect Systems): In indirect evaporative chillers that are used in combination with other cooling systems, such as a traditional air – conditioning system, the evaporative chiller can pre – cool the air, reducing the load on the compressor of the main system. This means that the compressor does not have to work as hard, consuming less energy. For example, in a commercial building, an indirect evaporative chiller can be used to pre – cool the incoming air, reducing the cooling load on the central air – conditioning unit’s compressor, resulting in energy savings.
Cost – Effectiveness
Lower Initial Cost: Direct evaporative chillers, in particular, have a relatively low initial cost compared to traditional air – conditioning systems. They are simple in design and require fewer components, which makes them more affordable to purchase and install. This makes them an attractive option for small – to – medium – sized businesses and homeowners who are looking for a cost – effective cooling solution. Even indirect evaporative chillers, although more complex, can be more cost – effective in the long run due to their energy – saving capabilities.
Lower Operating Costs: The energy – efficient operation of evaporative chillers also leads to lower operating costs. With reduced electricity consumption, the cost of running the cooling system is significantly reduced. Additionally, the maintenance requirements for evaporative chillers are generally less intensive compared to traditional air – conditioners. For example, wet – pad evaporative coolers only require periodic cleaning of the pads and checking of the water distribution system, which is less costly than the regular maintenance of a traditional air – conditioning compressor.
Environmental Friendliness
Reduced Greenhouse Gas Emissions: The lower energy consumption of evaporative chillers means that they produce fewer greenhouse gas emissions. Since most electricity generation is associated with the release of carbon dioxide and other pollutants, by using less electricity, evaporative chillers contribute to a lower carbon footprint. This makes them a more environmentally friendly option compared to traditional air – conditioning systems. In addition, evaporative chillers do not use refrigerants that can have a negative impact on the ozone layer, such as chlorofluorocarbons (CFCs) and hydrochlorofluorocarbons (HCFCs).
Water Conservation (in Some Cases): In indirect evaporative chillers, the water used for evaporation can be recycled and reused, which can lead to water conservation. In areas where water resources are scarce, this can be an important advantage. Even in direct evaporative cooling, the water consumption can be managed, and in some cases, the water used can be sourced from non – potable or recycled water, reducing the impact on the potable water supply.
Considerations when Using Evaporative Chillers
Water Availability
Direct Evaporative Chillers: Direct evaporative chillers require a continuous supply of water for the evaporation process. In regions where water is scarce or expensive, the use of direct evaporative chillers may be limited. However, as mentioned earlier, in some cases, non – potable or recycled water can be used. It is important to assess the water availability and cost in the area where the chiller will be installed. For example, in an arid region, if the cost of water is high, the operation of a direct evaporative chiller may not be economically viable without proper water management strategies.
Indirect Evaporative Chillers: While indirect evaporative chillers generally require less water compared to direct ones, they still need a water source for the evaporation process. In areas with water shortages, the water – recycling capabilities of indirect evaporative chillers can be an advantage. However, proper water treatment may be required to prevent scale formation and corrosion in the system, which can add to the operational complexity.
Humidity Control
Direct Evaporative Chillers: One of the main limitations of direct evaporative chillers is that they increase the humidity of the air. In humid climates or in applications where low humidity is required, such as in some manufacturing processes or storage of certain materials, direct evaporative cooling may not be suitable. In such cases, additional de – humidification measures may be needed, which can add to the cost and complexity of the system.
Indirect Evaporative Chillers: Indirect evaporative chillers offer better humidity control as they can cool the air without adding moisture. However, in some cases, if the heat – exchanger is not properly designed or maintained, there may be a small amount of moisture transfer. It is important to ensure that the indirect evaporative chiller is designed and operated in a way that meets the humidity requirements of the application.
Maintenance Requirements
Water – Related Components: Both direct and indirect evaporative chillers have water – related components that require regular maintenance. In direct evaporative chillers, the water – distribution system, such as the nozzles in spray – type chillers or the water pumps in wet – pad coolers, need to be checked for proper operation. The pads in wet – pad coolers need to be cleaned or replaced periodically to prevent clogging and ensure efficient evaporation. In indirect evaporative chillers, the heat – exchanger and the water – evaporation chamber need to be inspected for scale formation, corrosion, and proper heat transfer. The water treatment system, if used, also requires regular monitoring and adjustment.
Fan and Motor Components: The fans and motors in evaporative chillers, which are responsible for moving the air through the system, also need to be maintained. Regular checks of the fan blades for damage, motor lubrication, and electrical connections are necessary to ensure smooth operation. If the fan or motor malfunctions, it can affect the cooling performance of the chiller.
Future Trends in Evaporative Chillers
Technological Advancements
Improved Water Management Systems: Future evaporative chillers are likely to see advancements in water management systems. This may include the development of more efficient water – recycling technologies, such as advanced filtration and purification systems, to further reduce water consumption. Smart sensors and control systems may also be used to optimize the water usage based on the ambient conditions and the cooling load. For example, a sensor – based system could adjust the water flow rate in a direct evaporative chiller according to the humidity and temperature of the incoming air.
Enhanced Heat – Transfer Materials and Designs: Research is ongoing to develop more efficient heat – transfer materials and designs for evaporative chillers. The use of advanced materials in the heat exchanger, such as nanocomposites or high – performance polymers, could further improve the heat – transfer efficiency of indirect evaporative chillers. In direct evaporative chillers, new designs for wet – pads or water – spray systems may be developed to increase the evaporation rate and the uniformity of the cooled air. For example, new geometric designs for wet – pads could increase the surface area available for evaporation, improving the cooling performance.
Increased Adoption and Policy Support
Growing Awareness of Energy Efficiency: As the awareness of energy efficiency and environmental sustainability continues to increase, the demand for evaporative chillers is expected to grow. Businesses, institutions, and homeowners are becoming more conscious of the environmental impact of their energy – consuming devices, including cooling systems. This growing awareness will drive the adoption of evaporative chillers as a more sustainable and energy – efficient alternative to traditional cooling systems. For example, more commercial building owners may choose evaporative chillers to meet their cooling needs, especially in regions with suitable climate conditions.
Related recommendations
chiller manufacturers in usa
32The chiller manufacturing industry in the United States is a dynamic and integral part of the global cooling technology landscape. Chillers are essential devices for maintaining optimal temperatur...
View detailsrefrigeration unit ton
177Refrigeration Unit Ton: Understanding Cooling Capacity Measurements The "refrigeration unit ton," often abbreviated as RT, is a traditional unit of measurement for the cooling capacity of refri...
View detailschillers capacity
208Chiller Capacity: A Fundamental Aspect of Industrial Cooling Systems Chiller capacity is a critical parameter in the design and operation of industrial cooling systems. It defines the cooling o...
View detailsthermal oil heating system
133Thermal oil heating systems, also known as hot oil systems, are engineered to transfer heat generated by a furnace or other heat sources to process fluids in various industrial applications. These...
View details
HelloPlease log in