glycol chilled water system
Glycol chilled water systems have become an integral part of many industries and applications where efficient and reliable cooling is required. By using a mixture of glycol and water as the heat – transfer fluid, these systems offer unique advantages over traditional water – only chilled water systems. The addition of glycol modifies the properties of the water, making it suitable for a wider range of operating conditions.
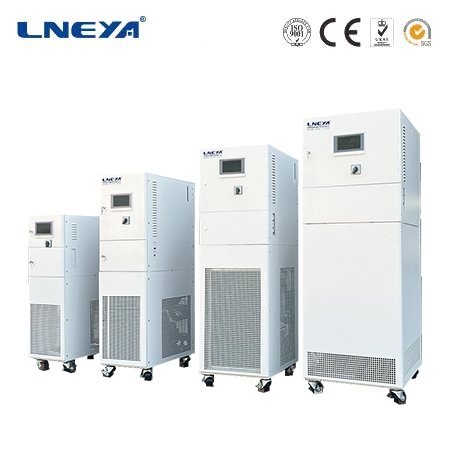
Components of Glycol Chilled Water Systems
Chiller
The chiller is the heart of the glycol chilled water system. It is responsible for removing heat from the glycol – water mixture. There are different types of chillers used in these systems, such as air – cooled and water – cooled chillers.
Air – Cooled Chillers: In an air – cooled chiller for a glycol system, ambient air is used to cool the refrigerant. The refrigerant in the chiller absorbs heat from the glycol – water mixture in the evaporator. The hot refrigerant vapor then travels to the condenser, where it releases heat to the ambient air. Air – cooled chillers are relatively easy to install and maintain, especially in areas where access to a water source for cooling is limited. However, their performance can be affected by high ambient temperatures.
Water – Cooled Chillers: Water – cooled chillers use water as the cooling medium for the refrigerant. They are more efficient in heat rejection compared to air – cooled chillers, especially in warm climates or high – load applications. In a water – cooled chiller, the refrigerant releases heat to the water in the condenser, and the warm water is then typically sent to a cooling tower to dissipate the heat. Water – cooled chillers are commonly used in large – scale industrial and commercial applications where high cooling capacities are required.
Pumps
Pumps are essential components in glycol chilled water systems as they circulate the glycol – water mixture throughout the system. The pump needs to be sized appropriately to overcome the resistance in the pipes and ensure sufficient flow rate. Centrifugal pumps are commonly used in these systems due to their ability to handle large volumes of fluid and provide a relatively constant flow rate over a wide range of operating conditions. The pump’s power consumption and efficiency are important factors to consider, as they can significantly impact the overall energy consumption of the glycol chilled water system.
Heat Exchangers
Heat exchangers play a crucial role in transferring heat between the glycol – water mixture and the fluid or space that needs to be cooled. There are different types of heat exchangers used, such as shell – and – tube heat exchangers and plate – type heat exchangers.
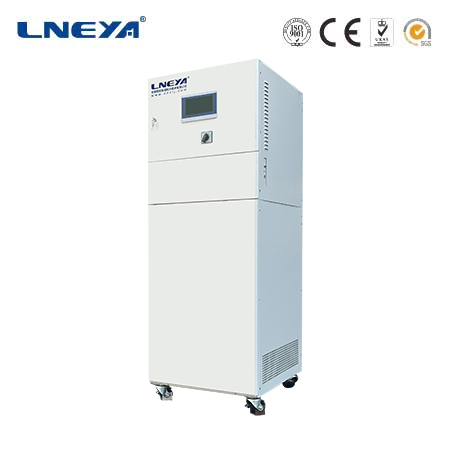
Shell – and – Tube Heat Exchangers: In a shell – and – tube heat exchanger, the glycol – water mixture can flow through either the tubes or the shell, while the fluid being cooled (e.g., air in an air – conditioning application or a process fluid in an industrial setting) flows through the other. The large surface area of the tubes allows for efficient heat transfer. Shell – and – tube heat exchangers are robust and can handle high pressures and temperatures, making them suitable for many industrial applications.
Plate – Type Heat Exchangers: Plate – type heat exchangers consist of a series of thin metal plates with corrugated surfaces. The glycol – water mixture and the fluid being cooled flow between alternate plates. The corrugated surfaces increase the surface area and promote turbulence, enhancing heat transfer efficiency. Plate – type heat exchangers are compact and lightweight, making them a popular choice in applications where space is limited, such as in some commercial buildings or small – scale industrial processes.
Control System
The control system in a glycol chilled water system monitors and regulates the operation of the system. It typically includes temperature sensors, pressure sensors, and a controller.
Temperature Sensors: Temperature sensors are placed at various points in the system, such as at the inlet and outlet of the chiller, heat exchanger, and the area being cooled. These sensors measure the temperature of the glycol – water mixture and send the data to the controller.
Pressure Sensors: Pressure sensors are used to monitor the pressure of the glycol – water mixture in the system. Maintaining the correct pressure is important for the proper operation of the pumps and to prevent issues such as cavitation.
Controller: The controller receives the data from the sensors and uses it to control the operation of the chiller, pumps, and other components. For example, if the temperature of the glycol – water mixture at the outlet of the heat exchanger is too high, the controller may increase the cooling capacity of the chiller or adjust the speed of the pump to increase the flow rate.
Working Principle of Glycol Chilled Water Systems
The working principle of glycol chilled water systems is based on the heat – transfer process. The glycol – water mixture, acting as the heat – transfer fluid, absorbs heat from the fluid or space that needs to be cooled. This can be in a commercial building’s air – conditioning system, where the warm air is cooled by passing over a heat exchanger through which the glycol – water mixture flows. The heated glycol – water mixture then travels to the chiller.
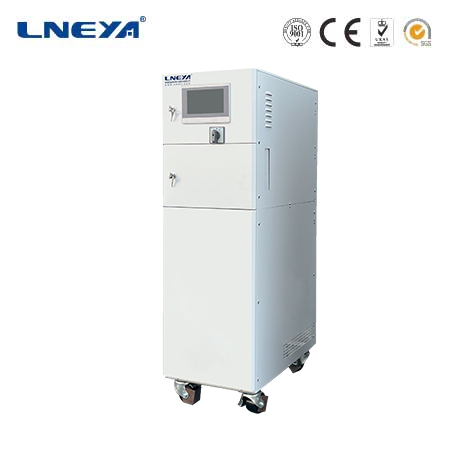
In the chiller, the refrigerant in the evaporator absorbs heat from the glycol – water mixture, causing the refrigerant to evaporate. The heat is then transferred to the condenser, where it is released to the cooling medium (either air or water, depending on the type of chiller). After being cooled in the chiller, the glycol – water mixture is pumped back to the heat exchanger to repeat the cycle. The addition of glycol to the water helps in maintaining the fluid’s liquid state even at low temperatures, preventing freezing and ensuring continuous operation of the system.
Types of Glycol Used in Chilled Water Systems
Ethylene Glycol
Ethylene glycol is one of the most commonly used glycols in chilled water systems. It has excellent antifreeze properties, which is why it is widely employed in applications where the system may be exposed to cold temperatures. A solution of ethylene glycol and water can have a significantly lower freezing point compared to pure water. For example, a 30% ethylene glycol – water solution has a freezing point of around -15°C (5°F), and a 50% solution can have a freezing point as low as -37°C (-35°F). However, ethylene glycol is toxic if ingested, so proper safety measures need to be in place to prevent leaks and spills.
Propylene Glycol
Propylene glycol is another option for use in chilled water systems. It also has antifreeze properties and is less toxic than ethylene glycol, making it a safer choice in applications where there is a risk of human or environmental exposure. For instance, in some food and beverage applications or in systems where the glycol – water mixture may come into contact with the environment, propylene glycol is preferred. The freezing – point depression properties of propylene glycol are similar to those of ethylene glycol, although the exact freezing points for the same concentrations may vary slightly.
Applications of Glycol Chilled Water Systems
Food and Beverage Industry
In the food and beverage industry, glycol chilled water systems are used at various stages of production, storage, and distribution. During food processing, these systems can be used to cool products quickly, preventing spoilage and maintaining quality. For example, in a meat processing plant, the carcasses can be cooled using a glycol – chilled water system to inhibit the growth of bacteria. In the beverage industry, glycol – cooled water is used to cool the product during bottling and canning processes. In cold storage warehouses, glycol – chilled water systems help maintain the low temperatures required to preserve the freshness of fruits, vegetables, and dairy products.
Data Centers
Data centers generate a large amount of heat due to the operation of servers and other electronic equipment. Glycol chilled water systems are used to remove this heat and maintain the optimal temperature for the servers. By circulating the glycol – water mixture through heat exchangers that are in contact with the server racks, the heat is absorbed and transferred to the chiller. This helps prevent servers from overheating, which can lead to performance degradation and hardware failures. The ability of glycol – chilled water systems to operate in a wide temperature range is particularly beneficial in data centers, as they can ensure reliable cooling even in environments with fluctuating ambient temperatures.
Industrial Processes
In industrial processes, glycol chilled water systems are used for a variety of purposes. In the plastics industry, for example, they can be used to cool molds during the injection – molding process. Maintaining the correct temperature in the molds is crucial for producing high – quality plastic parts. In the chemical industry, glycol – chilled water systems can be used to control the temperature of chemical reactions. Some reactions are exothermic and require cooling to proceed safely and efficiently. The glycol – water mixture can absorb the heat generated by the reaction, preventing overheating and ensuring the reaction proceeds as intended.
Advantages of Glycol Chilled Water Systems
Extended Operating Temperature Range
The addition of glycol to water significantly extends the operating temperature range of the chilled water system. As mentioned earlier, glycol – water mixtures have lower freezing points, allowing the system to operate in cold environments without the risk of the fluid freezing and causing damage to the components. This is especially important in applications where the system may be exposed to sub – zero temperatures, such as in outdoor cooling systems or in industrial processes in cold regions.
Corrosion Protection (with Additives)
Glycol – based chilled water systems can be formulated with corrosion inhibitors. Metals in the system, such as copper, iron, and aluminum, can corrode when in contact with water. The corrosion inhibitors in the glycol – water mixture form a protective film on the metal surfaces, preventing or reducing the rate of corrosion. This helps to extend the lifespan of the system components, including pipes, heat exchangers, and pumps, and ensures the reliable operation of the system over a long period.
Improved Heat – Transfer Characteristics
Glycol has certain heat – transfer properties that, when combined with water, can enhance the overall heat – transfer efficiency of the system. Although the specific heat capacity of glycol is lower than that of water, the mixture can still effectively transfer heat between the components of the system. The presence of glycol can also affect the viscosity of the fluid, which can have an impact on the flow characteristics and heat – transfer rates. In some cases, the optimized formulation of the glycol – water mixture can lead to better heat – transfer performance compared to using water alone.
Considerations for Glycol Chilled Water Systems
Glycol Concentration
Determining the appropriate glycol concentration in the water is crucial. A higher glycol concentration provides better freeze protection but also increases the viscosity of the fluid. Higher viscosity can lead to increased pumping power requirements and reduced heat – transfer efficiency. On the other hand, a lower glycol concentration may not offer sufficient freeze protection in cold environments. The optimal glycol concentration depends on the lowest expected temperature in the system’s operating environment, the required heat – transfer performance, and the pumping capabilities of the system. Specialized software or tables are often used to calculate the appropriate glycol concentration for a given set of conditions.
Fluid Compatibility
The glycol – water mixture needs to be compatible with the materials used in the system components. Some materials may react with glycol or the additives in the mixture, leading to degradation or corrosion. For example, certain types of plastics may be affected by glycol over time. It is important to select materials that are compatible with the glycol – water mixture to ensure the long – term integrity of the system. Manufacturers of glycol – based fluids often provide guidelines on material compatibility to help in the system design process.
Maintenance
Regular maintenance is essential for the proper operation of glycol chilled water systems. Maintenance tasks include checking the glycol concentration and the quality of the fluid. Over time, the glycol concentration may change due to evaporation or leaks, and the fluid may become contaminated with impurities. The system components, such as the chiller, pumps, and heat exchangers, also need to be inspected regularly for signs of wear, corrosion, or damage. The control system should be calibrated periodically to ensure accurate temperature and pressure regulation. In addition, any leaks in the system should be repaired promptly to prevent the loss of the glycol – water mixture and potential environmental contamination.
In conclusion, glycol chilled water systems are versatile and efficient cooling solutions for a wide range of applications. Understanding their components, working principle, types of glycol used, applications, advantages, and considerations is crucial for designing, operating, and maintaining these systems effectively. As industries continue to demand reliable and energy – efficient cooling, glycol chilled water systems are likely to play an increasingly important role in meeting these requirements.
Related recommendations
chiller 3 kw
46All You Need to Know About 3 - kW ChillersWhat is a 3 - kW Chiller?A 3 - kW chiller is a cooling device with a nominal cooling capacity of 3 kilowatts. It is designed to remove heat from a specifi...
View detailspropylene glycol for chiller
240Propylene Glycol for Chiller Systems: An In-Depth Analysis Understanding Propylene Glycol in Chillers Propylene glycol is a popular fluid used in chiller systems, particularly for its effect...
View detailscompact cooling unit
196Compact Cooling Units: Efficient Temperature Control for Space-Constrained Environments Compact cooling units offer a practical solution for cooling in environments where space is at a premium....
View detailsheating and cooling machine
200Heating and Cooling Machines: Comfort and Efficiency for Every Space Heating and cooling machines are the backbone of thermal comfort in various environments. These systems, also known as HVAC ...
View details
HelloPlease log in