glycol water chiller
Glycol water chillers are an important type of cooling equipment used in a wide range of applications. They are designed to cool a process fluid, typically a mixture of glycol and water, which is then used to transfer heat away from a specific process or space. The use of a glycol – water mixture as the heat – transfer fluid gives these chillers unique properties that make them suitable for various industrial and commercial applications.
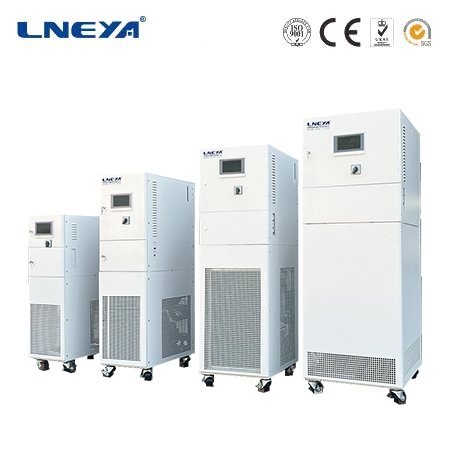
Working Principle of Glycol Water Chillers
Refrigeration Cycle Basics
Glycol water chillers operate on the same fundamental refrigeration cycle as other types of chillers, such as the vapor – compression cycle. The cycle consists of four main components: the compressor, condenser, expansion device, and evaporator.
Compressor: The process starts with the compressor. Low – pressure, low – temperature refrigerant vapor is drawn into the compressor. The compressor then compresses the refrigerant, increasing its pressure and temperature. This process requires energy input, usually in the form of electricity. For example, in a reciprocating compressor, pistons compress the refrigerant vapor within cylinders, raising its pressure and temperature significantly.
Condenser: After compression, the hot, high – pressure refrigerant vapor enters the condenser. In the condenser, heat is transferred from the refrigerant to a cooling medium. In air – cooled glycol water chillers, the cooling medium is ambient air, while in water – cooled models, it is water. As the refrigerant releases heat, it condenses into a high – pressure liquid. The condenser is often designed with a large surface area, such as finned tubes in air – cooled units or shell – and – tube heat exchangers in water – cooled units, to enhance heat transfer.
Expansion Device: The high – pressure liquid refrigerant then passes through an expansion device, such as a thermostatic expansion valve or a capillary tube. The expansion device reduces the pressure of the refrigerant, causing it to expand and cool down. This process is adiabatic, meaning no heat is added or removed from the refrigerant during expansion.
Evaporator: The low – pressure, low – temperature refrigerant enters the evaporator. In the evaporator of a glycol water chiller, the refrigerant absorbs heat from the glycol – water mixture. As the refrigerant absorbs heat, it vaporizes back into a low – pressure vapor, and the cycle repeats. The cooled glycol – water mixture can then be circulated to the process or space that needs to be cooled.
Role of the Glycol – Water Mixture
The glycol – water mixture serves as an intermediate heat – transfer fluid. Glycol, such as ethylene glycol or propylene glycol, is added to water to lower the freezing point of the mixture. This is crucial in applications where the process fluid may be exposed to low temperatures. For example, in a cold storage facility, the glycol – water chiller can cool the glycol – water mixture to temperatures well below the freezing point of pure water. The chilled glycol – water is then circulated through pipes in the cold storage area to maintain the low temperature. The glycol also has a higher heat – capacity than pure water in some cases, which can enhance the heat – transfer efficiency of the system.
Components of a Glycol Water Chiller System
Chiller Unit
The chiller unit houses the key components of the refrigeration cycle, including the compressor, condenser, and expansion device. The design of the chiller unit can vary depending on whether it is air – cooled or water – cooled. In an air – cooled chiller unit, the condenser is designed to transfer heat to the ambient air using fans to force air over the finned – tube heat exchanger. In a water – cooled chiller unit, the condenser transfers heat to a water – based cooling system, often connected to a cooling tower. The chiller unit is also equipped with controls to regulate the operation of the refrigeration cycle, such as temperature and pressure sensors, and a controller to adjust the speed of the compressor and fans (if applicable).
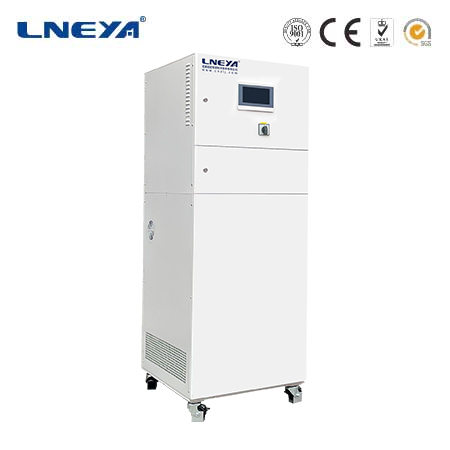
Heat Exchangers
Evaporator Heat Exchanger: The evaporator heat exchanger is where the refrigerant absorbs heat from the glycol – water mixture. It can be a shell – and – tube heat exchanger, where the refrigerant flows through the tubes and the glycol – water mixture flows around the tubes, or a plate – type heat exchanger, which offers high heat – transfer efficiency due to its large surface area and close – spaced plates. The design of the evaporator is optimized to maximize heat transfer between the refrigerant and the glycol – water mixture while minimizing pressure drop in the glycol – water circuit.
Secondary Heat Exchangers (if applicable): In some glycol water chiller systems, there may be secondary heat exchangers. For example, in a system where the glycol – water mixture needs to cool multiple processes or zones, a secondary heat exchanger can be used to transfer heat from the main glycol – water loop to a secondary loop dedicated to a specific process. This can help in isolating different processes and controlling the temperature more precisely.
Pumps
Pumps are essential for circulating the glycol – water mixture throughout the system. A circulation pump is used to move the glycol – water from the chiller unit to the process or space that needs to be cooled and then back to the chiller for re – cooling. The pump needs to be sized appropriately to ensure sufficient flow rate of the glycol – water mixture. The flow rate is important as it affects the heat – transfer efficiency. If the flow rate is too low, the heat transfer between the glycol – water and the process may be insufficient, while a flow rate that is too high can cause excessive pressure drops and energy consumption.
Applications of Glycol Water Chillers
Food and Beverage Industry
Cold Storage and Refrigeration: In the food and beverage industry, glycol water chillers are widely used in cold storage facilities. They are used to maintain low temperatures for storing perishable food items, such as fruits, vegetables, and dairy products. The glycol – water mixture can be cooled to temperatures as low as – 20°C or even lower, depending on the specific requirements. For example, in a large – scale cold storage warehouse for frozen foods, the glycol water chiller system circulates the chilled glycol – water through a network of pipes installed in the walls and ceilings of the storage area to keep the temperature constant.
Beverage Production: In beverage production, glycol water chillers are used in various processes. For instance, in the brewing industry, the glycol – water mixture can be used to cool the wort (the liquid extracted from the mashing process) to the appropriate fermentation temperature. In the production of soft drinks, it can be used to cool the product during bottling or canning to prevent spoilage and maintain the desired taste. The ability to control the temperature precisely using a glycol water chiller is crucial for ensuring the quality and consistency of the beverage products.
Pharmaceutical Industry
Temperature – Sensitive Storage and Production: In the pharmaceutical industry, many drugs and biological products are temperature – sensitive. Glycol water chillers are used to maintain the correct temperature in storage areas for raw materials, intermediate products, and finished drugs. They are also used in pharmaceutical production processes, such as in the cooling of reactors during chemical synthesis or in the lyophilization (freeze – drying) process. Precise temperature control is essential to ensure the stability and efficacy of pharmaceutical products. For example, in a pharmaceutical research laboratory, a glycol water chiller may be used to cool equipment such as centrifuges and incubators that require specific temperature conditions for experiments.
Industrial Manufacturing
Plastic Injection Molding: In plastic injection molding, the molds need to be cooled rapidly to solidify the plastic material. Glycol water chillers can provide the necessary cooling. The chilled glycol – water is circulated through channels in the molds, removing heat from the plastic and allowing it to solidify into the desired shape. This helps in reducing the cycle time of the injection – molding process and improving the quality of the plastic products.
Metalworking: In metalworking processes, such as machining and metal casting, heat is generated. Glycol water chillers can be used to cool the cutting tools or the molds in metal casting. For example, in a metal – cutting operation, the chilled glycol – water can be sprayed or circulated around the cutting tool to reduce the temperature, preventing tool wear and improving the surface finish of the machined part.
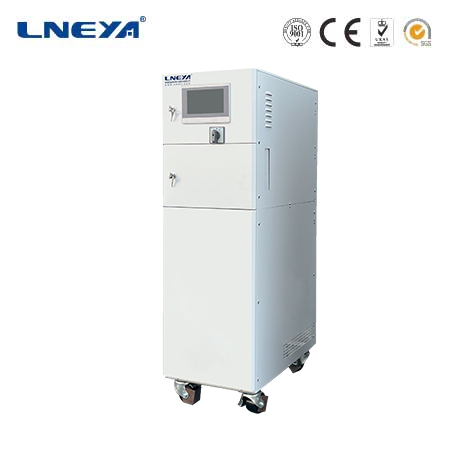
Advantages of Glycol Water Chillers
Low – Temperature Operation
One of the main advantages of glycol water chillers is their ability to operate at low temperatures. The addition of glycol to water lowers the freezing point of the heat – transfer fluid, allowing the chiller to cool the glycol – water mixture to temperatures well below 0°C. This makes them suitable for applications where traditional water – based cooling systems would freeze, such as in cold storage facilities or in industrial processes that require sub – zero temperatures.
Freeze Protection
The glycol – water mixture provides excellent freeze protection. In outdoor applications or in facilities where the ambient temperature can drop below the freezing point of water, the glycol in the mixture prevents the fluid from freezing in the pipes and heat exchangers. This helps in avoiding damage to the cooling system, such as burst pipes, which can be costly to repair.
Corrosion Inhibition (with Proper Additives)
When properly formulated, the glycol – water mixture can also offer corrosion inhibition. Some glycols, especially when combined with appropriate corrosion inhibitors, can protect the metal components of the chiller system, such as pipes, pumps, and heat exchangers, from rust and corrosion. This extends the lifespan of the equipment and reduces maintenance costs.
Disadvantages of Glycol Water Chillers
Lower Heat – Transfer Efficiency (compared to pure water in some cases)
Although glycol has some beneficial properties, in some cases, the addition of glycol to water can slightly reduce the heat – transfer efficiency compared to using pure water. Glycol has a lower thermal conductivity than water, which means that heat transfer between the glycol – water mixture and the process or the refrigerant may not be as efficient as with pure water. However, this can be mitigated through proper system design, such as using larger heat – transfer surfaces or optimizing the flow rate.
Higher Cost of the Heat – Transfer Fluid
Glycol is more expensive than water. The cost of the glycol – water mixture, especially when using high – quality glycols, can be a significant factor, especially for large – scale applications. Additionally, over time, the glycol – water mixture may need to be replaced or replenished, adding to the operational costs.
Environmental Concerns (depending on the type of glycol)
Some types of glycol, such as ethylene glycol, can be toxic to the environment if released. Although propylene glycol is generally considered less toxic, proper handling and disposal of the glycol – water mixture are still required. In industrial applications, spills or leaks of the glycol – water mixture need to be managed carefully to prevent environmental contamination.
Maintenance of Glycol Water Chillers
Fluid Monitoring and Maintenance
Regularly monitor the glycol – water mixture. Check the concentration of glycol in the mixture, as it can change over time due to evaporation or leaks. The correct glycol concentration is crucial for maintaining the freezing point and heat – transfer properties of the mixture. If the glycol concentration is too low, the mixture may be at risk of freezing, while if it is too high, it can affect the heat – transfer efficiency. Also, check for any signs of contamination in the glycol – water mixture, such as the presence of dirt, debris, or biological growth. In case of contamination, the mixture may need to be filtered or replaced.
Component Inspection
Inspect the components of the chiller system regularly. Check the compressor for proper operation, looking for signs of wear, leaks, or abnormal noises. The condenser and evaporator heat exchangers should be inspected for dirt, scale, or corrosion. Dirt or scale on the heat – exchanger surfaces can reduce the heat – transfer efficiency. In air – cooled condensers, clean the finned – tube surfaces to ensure proper air circulation. In water – cooled condensers, check for any signs of water leaks or blockages in the water – side. Also, inspect the pumps for proper operation, including checking the impeller for wear and ensuring that the pump is providing the correct flow rate.
Control System Calibration
Calibrate the control system of the glycol water chiller regularly. The temperature and pressure sensors in the control system need to be accurate to ensure proper operation of the chiller. If the sensors are not calibrated correctly, the chiller may not cool the glycol – water mixture to the desired temperature or may operate inefficiently. Any software updates for the control system should also be installed to improve performance and functionality.
Choosing the Right Glycol Water Chiller
Cooling Capacity Requirements
Determine the cooling capacity needed for your application. Calculate the heat load that the chiller needs to handle. This includes considering factors such as the heat generated by the process, the ambient temperature, and the desired temperature of the glycol – water mixture. For example, in a large – scale food processing plant, the heat load from the various production processes, such as cooking, baking, and refrigeration, needs to be accurately calculated to select a glycol water chiller with sufficient cooling capacity.
Temperature Range
Consider the temperature range required for your application. Different applications may need the glycol – water mixture to be cooled to different temperatures. If your process requires very low temperatures, make sure the chiller is capable of achieving and maintaining those temperatures. Some glycol water chillers are designed specifically for low – temperature applications, while others may be more suitable for moderate – temperature cooling.
Type of Glycol and Fluid Handling
Decide on the type of glycol to use. Ethylene glycol and propylene glycol are the most common types. Consider factors such as toxicity, cost, and performance. If environmental concerns are a priority, propylene glycol may be a better choice. Also, ensure that the chiller system is compatible with the type of glycol you choose. The materials of construction of the pipes, heat exchangers, and pumps should be resistant to the glycol – water mixture to prevent corrosion and ensure long – term operation.
Conclusion
Glycol water chillers are versatile cooling systems with unique properties that make them suitable for a wide range of applications, especially those requiring low – temperature operation and freeze protection. Understanding their working principle, components, applications, advantages, disadvantages, maintenance requirements, and selection criteria is essential for industries to effectively utilize these chillers. By carefully considering these factors, businesses can choose the right glycol water chiller for their specific needs, ensuring efficient cooling and reliable operation.
Related recommendations
types of temperature controller
226Types of Temperature Controllers: Ensuring Precision in Temperature Control Temperature control is critical in a wide array of industries, from manufacturing to medical applications. The precis...
View detailsglycol chillers for sale
13Introduction Glycol chillers are an important type of cooling equipment available in the market. They are designed to efficiently remove heat from a process or space using a coolant mixture pr...
View detailsefficient heating and cooling systems
29Efficient Heating and Cooling SystemsIn today's world, where energy conservation and environmental sustainability are of utmost importance, efficient heating and cooling systems have become a nec...
View detailsprocess heaters
13Process heaters are industrial equipment designed to raise the temperature of a process fluid, gas, or solid. They play a crucial role in numerous industries by providing the necessary heat for ch...
View details
HelloPlease log in