high temp controller
High Temp Controller: Regulating Extreme Temperatures in Industrial Processes
Introduction
High temp controllers are specialized temperature control devices engineered to operate and maintain temperatures in applications where standard controllers would fail due to the high heat. They are crucial in industries such as manufacturing, food processing, and chemical engineering, where processes often require temperatures exceeding the limits of conventional control systems.
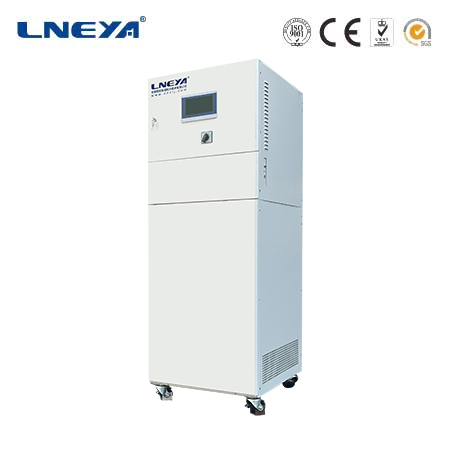
Key Features of High Temp Controllers
High temp controllers are designed with several key features to ensure reliable operation in extreme conditions:
High-Temperature Sensors: These controllers use sensors that can withstand and accurately measure high temperatures.
Robust Construction: They are built with materials that can resist heat and are often housed in protective enclosures.
Advanced Control Algorithms: Some high temp controllers employ sophisticated algorithms that can handle the nonlinear characteristics of high-temperature processes.
Applications
High temp controllers are used in a variety of applications, including:
Kilns and Ovens: In ceramics, glass, and metalworking industries, these controllers maintain consistent temperatures for quality control.
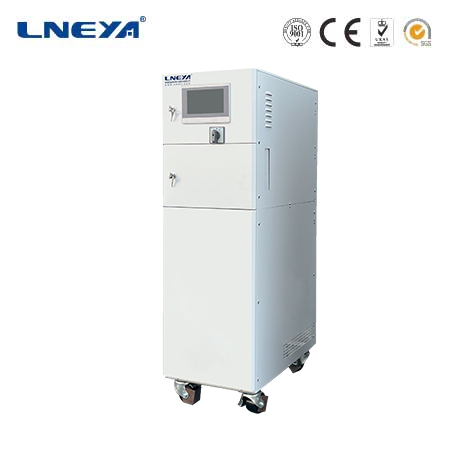
Heat Treatment Processes: They are used in annealing, hardening, and other heat treatment processes in metallurgy.
Food Processing: For applications like baking, roasting, and sterilization, where high temperatures are required.
Efficiency Factors
The efficiency of a high temp controller is influenced by:
Accuracy: The ability to measure and control temperature within tight tolerances.
Response Time: How quickly the controller can react to temperature changes and make adjustments.
Reliability: The controller’s ability to operate consistently without failure, even in extreme conditions.
Maintenance
Proper maintenance is essential for high temp controllers to ensure their accuracy and longevity:
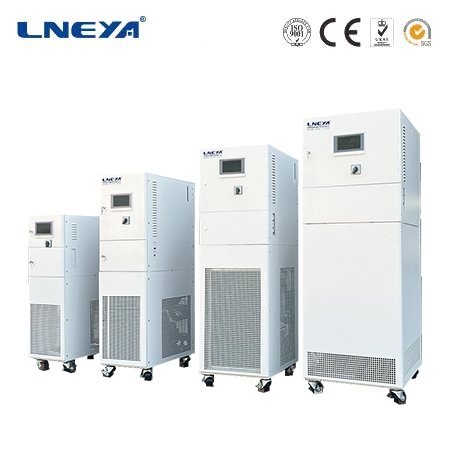
Regular Calibration: Periodic calibration ensures the controller provides accurate temperature readings.
Sensor Checks: Regularly inspecting and replacing sensors can prevent inaccurate readings and control issues.
Cleaning: Keeping the controller and its components free from dust and debris can improve its performance.
Conclusion
High temp controllers play a critical role in industries that require precise temperature control at elevated temperatures. By understanding their key features, applications, and maintenance requirements, operators can ensure that these controllers provide reliable and efficient temperature regulation. Regular maintenance and proper installation are key to achieving optimal performance from high temp controllers。
Related recommendations
laboratory cooling equipment
123The Significance of Laboratory Cooling EquipmentEnsuring Experiment Accuracy: Many scientific experiments are highly sensitive to temperature fluctuations. For example, in chemical reactions, even...
View detailsportable air cooled chillers
185Understanding Portable Air Cooled Chillers Portable air cooled chillers are self-contained, compact cooling systems that provide a flexible and efficient cooling solution for a variety of appli...
View detailswater heater coil
213Water Heater Coil: Enhancing Efficiency and Performance Water heater coils are critical components in both domestic and commercial water heating systems, providing efficient heat transfer to pr...
View detailsair cooled chiller manufacturers in india
172Air-Cooled Chiller Manufacturers in India: An Overview Introduction to Air-Cooled Chillers in India Air-cooled chillers are essential in various industries in India, including manufactur...
View details
HelloPlease log in