hot water oil heating system
Hot Water Oil Heating System: A Comprehensive Explanation
A hot water oil heating system is a heating mechanism designed to transfer heat from hot water to oil, which is then used to provide thermal energy for a wide range of industrial processes. This system plays a significant role in maintaining the proper temperature conditions required for various operations.
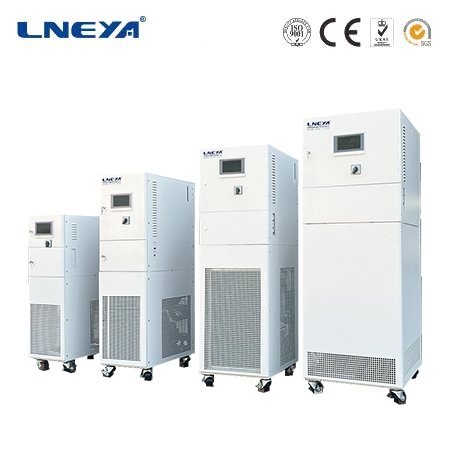
Working Principle
The basic principle of a hot water oil heating system is centered around heat transfer. Hot water, which is usually generated by a boiler or other heat – generating sources, serves as the primary heat – carrier. The hot water flows through a heat exchanger, where it comes into contact with the oil. Through the process of conduction and convection, heat is transferred from the hot water to the oil. As the oil absorbs heat, its temperature rises. The heated oil is then circulated to the areas where heat is needed, such as industrial reactors, dryers, or other equipment. After releasing its heat, the oil returns to the heat exchanger to be reheated, creating a continuous heating cycle.
Key Components
Heat Exchanger: This is the core component of the system. It is designed to maximize the heat – transfer efficiency between the hot water and the oil. There are different types of heat exchangers, such as shell – and – tube heat exchangers, where the hot water and oil flow through separate channels within the exchanger, allowing heat to transfer across the walls. Plate – type heat exchangers are also commonly used, which consist of a series of thin plates with channels for the hot water and oil, providing a large surface area for heat transfer.
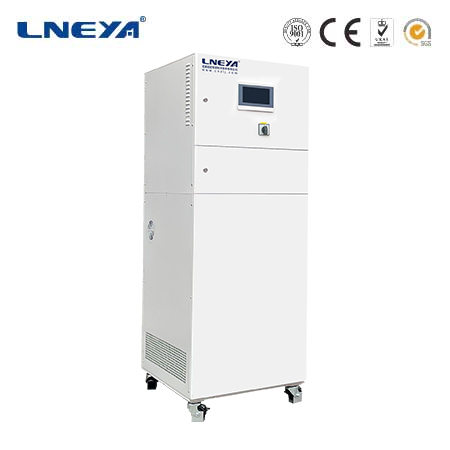
Pumps: Pumps are essential for circulating both the hot water and the oil within the system. The hot – water pump ensures a continuous flow of hot water from the heat source to the heat exchanger, while the oil pump is responsible for moving the oil through the system, from the heat exchanger to the heat – consuming equipment and back.
Control Units: These units are used to regulate the operation of the system. Temperature sensors are installed to monitor the temperature of the hot water, oil, and the process where the heated oil is applied. Based on the temperature readings, the control units can adjust the flow rate of the hot water and oil, as well as the heat input to the hot – water source, ensuring that the system operates within the desired temperature range.
Types of Hot Water Oil Heating Systems
Direct – Contact Systems: In direct – contact hot water oil heating systems, the hot water and oil come into direct physical contact. This type of system offers high – speed heat transfer as there is no intermediate barrier between the two fluids. However, it requires careful selection of the oil and water to ensure compatibility and prevent contamination. For example, in some specific industrial processes where the oil and water can be safely mixed during the heat – transfer process, direct – contact systems can be highly efficient.
Indirect – Contact Systems: Most common hot water oil heating systems are indirect – contact. In these systems, a heat exchanger separates the hot water and the oil. This design provides better control over the heating process and ensures that the oil remains pure without the risk of water contamination. It is suitable for a wide range of applications, especially in industries where the purity of the oil is crucial, such as in the food and pharmaceutical industries.
Applications
Petrochemical Industry: In petrochemical processes like distillation, cracking, and polymerization, hot water oil heating systems are used to provide the necessary heat. For instance, in distillation columns, the heated oil is used to vaporize the crude oil fractions, enabling their separation based on different boiling points.
Food Industry: In food processing, these systems are used for processes such as baking, drying, and sterilization. For example, in a bakery, the heated oil can be used to maintain the temperature of baking ovens, ensuring even baking of bread and other products.
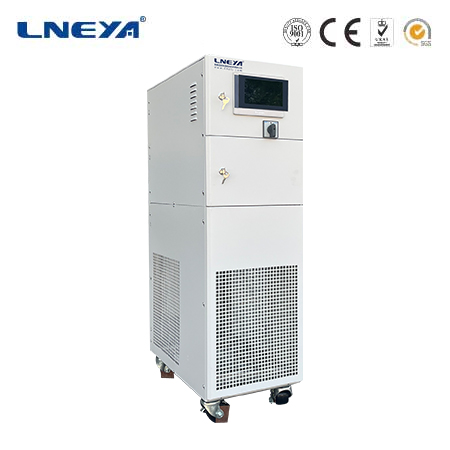
Manufacturing Industry: In manufacturing processes like plastic molding and metal casting, hot water oil heating systems play a vital role. In plastic molding, the heated oil is used to heat the molds, allowing the plastic to flow and take the shape of the mold accurately.
Advantages
High – Efficiency Heat Transfer: The use of heat exchangers in hot water oil heating systems enables efficient heat transfer from the hot water to the oil. This results in quick heating of the oil and reduces energy consumption, as the heat is transferred effectively without significant losses.
Stable Temperature Control: The control units in the system can precisely regulate the temperature of the oil, ensuring stable operation in industrial processes. This stable temperature control is crucial for maintaining product quality and process efficiency.
Energy – Saving Features: By using hot water as a heat – carrier, which can be generated from various energy sources, including waste heat recovery systems, hot water oil heating systems can be energy – efficient. The ability to recycle and reuse heat further contributes to energy savings.
Factors to Consider When Choosing a Hot Water Oil Heating System
Heating Capacity: The heating capacity of the system should match the heat requirements of the industrial process. This depends on factors such as the size of the equipment to be heated, the heat – consuming rate of the process, and the desired operating temperature.
Temperature Requirements: Different industrial processes have specific temperature requirements. The hot water oil heating system should be able to provide the oil at the required temperature accurately. Some processes may require a constant high – temperature oil supply, while others may need a variable – temperature oil depending on the stage of the process.
Cost – Effectiveness: This includes the initial investment cost of the system, the operating cost (such as energy consumption, water, and oil costs), and the maintenance cost. A cost – effective system should have a reasonable initial investment and low long – term operating and maintenance costs.
In conclusion, hot water oil heating systems are versatile and efficient heating solutions with a wide range of applications in different industries. Understanding their working principle, components, types, applications, advantages, and selection criteria is essential for industries to make informed decisions when choosing a heating system.
Related recommendations
small heating system
31What are Small Heating Systems?Small heating systems are self - contained or integrated heating units designed to meet the heating requirements of relatively small - sized areas. These areas can ...
View detailssmall heating system
251Small Heating System: Efficient and Sustainable Heating Solutions Small heating systems are increasingly popular for their ability to provide localized heating or serve as a primary heating sou...
View detailsHow effective is the chiller for rotary evaporator in industrial refrigeration?
727How effective is the chiller for rotary evaporator in industrial refrigeration? 1. Can effectively cool equipment, slow down heat accumulation, and improve production efficiency; ...
View detailschillers equipment
134Understanding Chillers Equipment Chillers are refrigeration systems designed to remove heat from a liquid through a vapor-compression or absorption refrigeration cycle. They are widely used in ...
View details
HelloPlease log in