industrial water heater electric
Introduction
In the industrial landscape, maintaining precise water temperatures is essential for numerous operations, from manufacturing processes to facility sanitation. Industrial electric water heaters have emerged as a reliable and efficient solution for heating large volumes of water. Unlike gas – fired or other fuel – based heaters, electric water heaters rely on electrical energy, providing advantages such as cleaner operation, precise temperature control, and ease of integration into existing industrial setups. This article delves deep into the world of industrial electric water heaters, exploring their functionality, applications, and how industries can make the most of them.
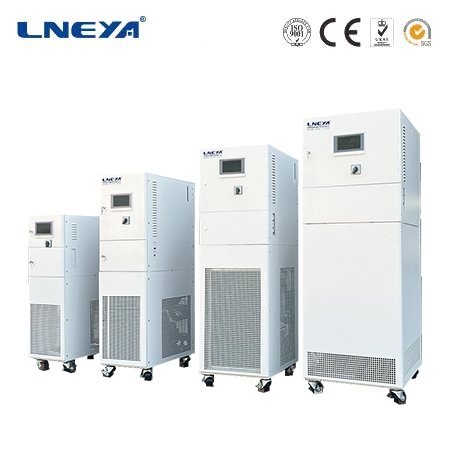
Working Principles
Induction Heating
Induction heating operates on a different principle. It uses electromagnetic induction to generate heat within the water. An alternating current (AC) passes through a coil, creating a changing magnetic field. When water, which is a conductive medium, is placed within this magnetic field, eddy currents are induced in the water. These eddy currents encounter the electrical resistance of the water, generating heat. Induction heating offers rapid heating, precise temperature control, and energy – efficient operation. It can heat water directly without the need for a separate heating element in contact with the water, reducing the risk of scaling and corrosion.
Key Components
3.1 Heating Elements
Heating elements are the core of industrial electric water heaters. For resistance – based heaters, common materials for heating elements include nichrome, stainless steel, and Incoloy. Nichrome is popular due to its high resistivity, good oxidation resistance, and ability to withstand high temperatures. Stainless – steel elements offer excellent corrosion resistance, making them suitable for heating water with various chemical compositions. Incoloy elements combine high – temperature strength and corrosion resistance, ideal for demanding industrial applications. In induction heaters, the coil is the key component responsible for generating the magnetic field that heats the water.
Control Systems
Modern industrial electric water heaters are equipped with advanced control systems. These systems typically include thermostats, which monitor the water temperature and regulate the power supply to the heating elements. Programmable logic controllers (PLCs) are often used in more complex setups, allowing for precise temperature control, scheduling, and integration with other industrial processes. Some control systems also feature remote monitoring capabilities, enabling operators to adjust settings and receive alerts from a central location. This ensures that the water temperature remains within the required range, optimizing process efficiency and product quality.
Insulation
Insulation is crucial for minimizing heat loss and improving the energy efficiency of industrial electric water heaters. High – quality insulation materials, such as fiberglass, polyurethane foam, or mineral wool, are used to wrap the water tank or the heater unit. Good insulation reduces the amount of heat that escapes into the surrounding environment, keeping the water hot for longer periods and reducing the energy consumption required to maintain the desired temperature. Additionally, proper insulation helps protect operators from accidental burns and reduces the overall operating costs of the heater.
Types of Industrial Electric Water Heaters
4.1 Immersion Heaters
Design and Operation: Immersion heaters are designed to be directly immersed in the water tank or vessel. They consist of a heating element enclosed in a protective sheath, usually made of stainless steel or other corrosion – resistant materials. The heating element is connected to an electrical power source, and when energized, it transfers heat directly to the water. Immersion heaters can be flanged, where they are mounted through a flange on the side of a tank, or cartridge – type, which are inserted into drilled holes in the tank wall.
Applications: These heaters are widely used in industrial processes where large volumes of water need to be heated in a static tank. For example, in the food and beverage industry, immersion heaters can be used to heat water for cleaning equipment, pasteurization processes, or cooking. In chemical plants, they are employed to heat water used in various chemical reactions or for maintaining the temperature of storage tanks.
Circulation Heaters
Design and Operation: Circulation heaters are used when a continuous flow of heated water is required. They typically have a cylindrical housing with one or more heating elements inside. Water enters the heater, flows around the heating elements, absorbs the heat, and then exits at an elevated temperature. Some circulation heaters are equipped with built – in pumps to ensure a consistent flow rate, while others rely on an external pumping system. The flow rate and temperature of the water can be precisely controlled by adjusting the power input to the heating elements and the speed of the pump (if applicable).
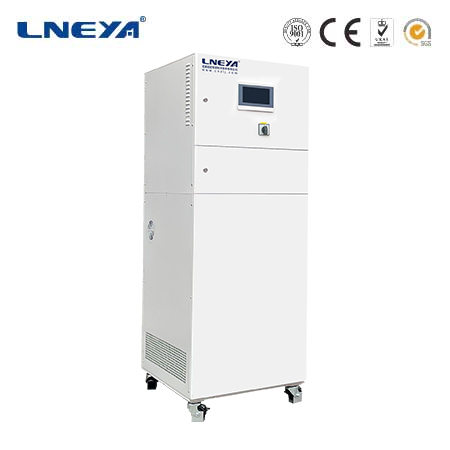
Applications: Circulation heaters are essential in industries such as plastics manufacturing, where they heat the water used in injection – molding machines to maintain the proper temperature of the plastic material. In power plants, they are used to heat the water in closed – loop systems for various purposes, including pre – heating feedwater or maintaining the temperature of cooling water.
Duct Heaters
Design and Operation: Duct heaters are installed within air ducts or ventilation systems to heat the air that will be used to heat water indirectly. They consist of heating elements, usually in the form of finned – tube elements or wire – wound elements, mounted in a metal housing. As air passes over the heating elements, it is heated and then directed towards the water – heating process, such as in a heat exchanger where the heated air transfers its heat to the water. Duct heaters can be controlled to regulate the temperature of the air, and they often feature safety devices to prevent overheating.
Applications: In industrial drying processes where water – laden materials need to be dried, duct heaters are used to heat the air that will evaporate the moisture. They are also found in some industrial buildings where they provide pre – heated air for water – heating systems, improving the overall efficiency of the heating process.
Applications in Industry
5.1 Manufacturing Industry
Metalworking: In metalworking operations, industrial electric water heaters are used for various purposes. For example, in hot forging processes, water is heated and used for cooling dies and tools to prevent overheating and extend their lifespan. The precise temperature control of electric water heaters ensures that the cooling water is at the optimal temperature, maintaining the quality of the metal products. In electroplating, heated water is used for cleaning and preparing metal surfaces before plating, and electric water heaters provide a reliable source of heated water with consistent temperature.
Plastics Processing: The plastics industry relies on industrial electric water heaters for heating the water used in injection – molding machines, extruders, and other processing equipment. Maintaining the correct water temperature is crucial for the proper melting and shaping of plastic materials. Electric water heaters offer fast heating times and accurate temperature control, which helps improve production efficiency and product quality by ensuring that the plastic is in the right state during processing.
Chemical Industry
Reactor Heating: In chemical plants, many chemical reactions require specific temperature conditions, and industrial electric water heaters are used to heat the reactors. The water is heated and circulated around the reactor jacket to provide the necessary heat for the reaction. The ability to precisely control the water temperature is essential for the success of the chemical reactions, as even small temperature variations can affect the reaction rate and the quality of the final product.
Process Water Heating: Electric water heaters are also used to heat the process water used in various chemical processes, such as distillation, evaporation, and crystallization. The heated water helps drive these processes forward, and the consistent temperature provided by electric heaters ensures the reliability and efficiency of the chemical operations.
Food and Beverage Industry
Cooking and Processing: In food processing plants, industrial electric water heaters are used for cooking, baking, and pasteurization. For instance, in the production of soups, sauces, and canned foods, heated water is used in large – scale cooking vats. The accurate temperature control of electric water heaters helps ensure that the food is cooked evenly and safely, meeting the strict quality and safety standards of the industry. In beverage production, heated water is used for cleaning equipment, sanitizing bottles, and in the brewing process.
Dairy Operations: In the dairy industry, electric water heaters play a vital role in heating milk for pasteurization, a process that kills harmful bacteria while preserving the nutritional value of the milk. The ability to precisely control the temperature and heating time is crucial for the effectiveness of pasteurization. Additionally, heated water is used for cleaning and sanitizing dairy equipment to maintain hygiene standards.
Selection Criteria
6.1 Heating Capacity
Future Expansion: Industries should also consider future growth and expansion when selecting a water heater. If there is a possibility of increasing production volume or adding more processes that require heated water in the future, choosing a heater with a slightly higher heating capacity than the current needs can save the cost and inconvenience of having to replace the heater later.
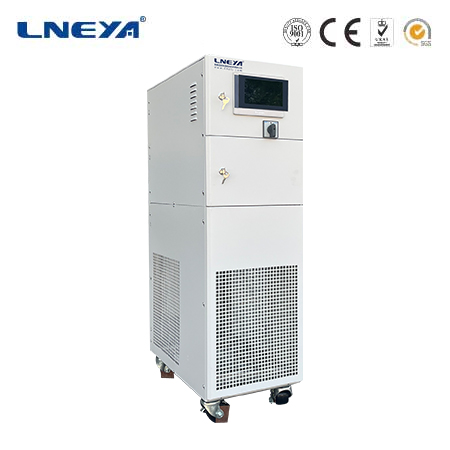
Temperature Range
Process Requirements: Different industrial processes have specific temperature requirements. Some processes may only need water heated to a relatively low temperature, while others, such as certain chemical reactions or heat – treatment processes in manufacturing, require high – temperature water. It’s crucial to choose an electric water heater that can provide the required temperature range for the specific application. For example, in a high – temperature sterilization process in the pharmaceutical industry, the water heater must be able to reach and maintain temperatures above 120°C.
Temperature Control Accuracy: In addition to the temperature range, the accuracy of temperature control is also important. In precision manufacturing processes or chemical reactions where a specific temperature needs to be maintained within a narrow tolerance, heaters with advanced control systems that offer high – accuracy temperature control are required. Some electric water heaters can maintain the temperature within ±1°C, ensuring consistent process results and product quality.
Energy Efficiency
Efficiency Ratings: Energy – efficient electric water heaters can significantly reduce operating costs. Look for heaters with high – efficiency ratings, such as those that meet or exceed industry – standard energy – efficiency requirements. Some water heaters feature technologies like insulation enhancements, smart control systems that optimize energy usage based on demand, and high – efficiency heating elements. Energy – efficient models may have a higher upfront cost but can result in long – term savings through reduced energy consumption.
Operating Costs: Consider the long – term operating costs when selecting a water heater. This includes not only the electricity consumption but also factors such as maintenance costs and the lifespan of the heater. A more energy – efficient heater may have lower electricity bills over time, and a longer – lasting heater with fewer maintenance requirements can further reduce the overall cost of ownership.
Safety Features
Over – Temperature Protection: Over – temperature protection is a critical safety feature in industrial electric water heaters. This feature monitors the water temperature and shuts off the power supply if the temperature exceeds a pre – set limit. Over – temperature protection helps prevent damage to the heater, the connected equipment, and potential safety hazards such as scalding or steam explosions.
Ground Fault Protection: Ground fault protection is designed to detect and interrupt the electrical current in case of a fault, such as a short circuit to ground. This helps protect operators from electrical shocks and prevents damage to the heater and other electrical components. Industrial electric water heaters should be equipped with reliable ground fault protection devices, especially in environments where there is a risk of water or moisture exposure.
Pressure Relief Valves: In water heaters that operate under pressure, pressure relief valves are essential. These valves open automatically if the pressure inside the heater exceeds a safe level, releasing excess pressure to prevent the tank from bursting. Regular inspection and maintenance of pressure relief valves are necessary to ensure their proper functioning.
Maintenance Practices
7.1 Regular Inspections
Heating Elements: Regularly inspect the heating elements for signs of wear, damage, or scaling. In resistance – based heaters, look for visible signs of corrosion, breaks, or discoloration on the heating elements. If any damage is detected, the heating elements should be replaced promptly to ensure the proper operation of the heater. For induction heaters, check the coil for any physical damage or signs of overheating.
Control Systems: Check the control systems, including thermostats, PLCs, and sensors, to ensure they are functioning correctly. Calibrate the temperature sensors regularly to ensure accurate temperature readings. Test the control functions, such as on/off switching, temperature adjustment, and safety shut – off mechanisms, to ensure they are working properly. Any malfunctioning control components should be repaired or replaced immediately.
Insulation: Inspect the insulation around the water tank or heater unit for any signs of damage or deterioration. Damaged insulation can lead to increased heat loss and reduced energy efficiency. Repair or replace the insulation as needed to maintain the optimal performance of the heater.
Cleaning
Water Tank Cleaning: Over time, sediment and scale can accumulate in the water tank, reducing its efficiency and potentially damaging the heating elements. Periodically drain and clean the water tank to remove these deposits. Use appropriate cleaning agents and methods based on the type of sediment and scale present. In some cases, chemical descaling may be required to remove stubborn scale deposits.
Heating Element Cleaning: For resistance – based heaters, clean the heating elements to remove any scale or deposits that may have formed on their surfaces. This can be done using a soft brush or a descaling solution. In induction heaters, ensure that the area around the coil is kept clean and free from debris that could interfere with the magnetic field.
Replacement of Worn – Out Parts
Monitoring and Replacement: Keep a close eye on all the components of the industrial electric water heater for signs of wear and tear. Replace any worn – out or damaged parts promptly, such as gaskets, seals, valves, and electrical connectors. Maintaining a stock of essential spare parts can help minimize downtime in case of a breakdown. Follow the manufacturer’s recommendations for the replacement intervals of different components to ensure the reliable operation of the heater.
Challenges and Future Trends
8.1 Challenges
High Energy Costs: One of the main challenges for industries using industrial electric water heaters is the high cost of electricity. Fluctuations in electricity prices can significantly impact the operating costs of these heaters, especially for industries that rely on large – scale water heating. To mitigate this challenge, industries are constantly looking for ways to improve the energy efficiency of their water heaters and explore alternative energy sources.
Scaling and Corrosion: Water quality can pose a challenge for industrial electric water heaters. Hard water, which contains high levels of minerals such as calcium and magnesium, can lead to scaling on the heating elements and inside the water tank. Scaling reduces the heat transfer efficiency of the heater and can cause the heating elements to burn out prematurely. Corrosion, especially in water with high acidity or chloride content, can also damage the components of the water heater. Proper water treatment and regular maintenance are required to address these issues.
Future Trends
Smart and Connected Heaters: The future of industrial electric water heaters lies in smart and connected technologies. These heaters will be equipped with sensors, internet – of – things (IoT) capabilities, and advanced control systems that can be remotely monitored and controlled. Smart heaters can optimize energy usage based on real – time data, predict maintenance needs, and integrate with other industrial processes, improving overall efficiency and reducing operating costs.
Renewable Energy Integration: As the world moves towards more sustainable energy sources, there is a growing trend of integrating industrial electric water heaters with renewable energy systems such as solar power and geothermal energy. Solar – powered water heaters use photovoltaic panels to generate electricity to heat the water, reducing the reliance on the grid. Geothermal systems can also be used in conjunction with electric water heaters to provide a more energy – efficient and environmentally friendly heating solution.
Related recommendations
cooler cooling
189Introduction to Chiller Cooling SystemsChiller cooling systems are essential for maintaining comfortable temperatures in commercial buildings, industrial processes, and data centers. These systems...
View detailsflow through chiller
96Definition and Basic StructureA flow through chiller, also known as a direct - flow chiller, consists of several key components. At its core, it has a refrigerant circuit, a heat exchanger, a pump...
View detailsheater lab
208Laboratory Heaters: Types, Applications, and Safety Laboratory heaters are essential for maintaining precise temperature control in various scientific applications. They are used for a wide ran...
View detailssmall industrial water chiller
237Small Industrial Water Chillers: Market Trends and Applications Small industrial water chillers are essential in maintaining optimal temperatures in various industrial processes. These chillers...
View details
HelloPlease log in