low pressure chiller
Low Pressure Chillers: A Comprehensive Guide
Introduction
Low pressure chillers play a crucial role in modern cooling applications. They are designed to provide efficient cooling solutions by circulating a refrigerant through a closed – loop system. The distinguishing feature of low pressure chillers is their operation at pressures lower than those of traditional chillers, which brings about several advantages in terms of energy consumption, safety, and environmental friendliness.
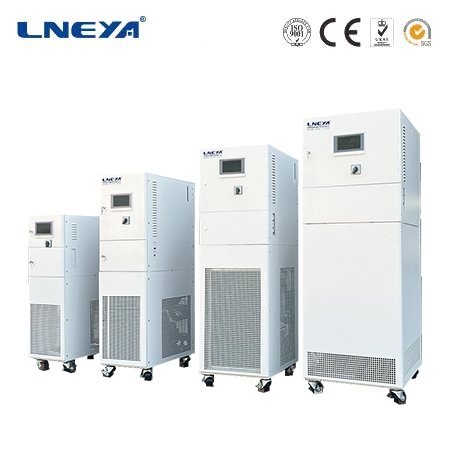
Components of Low Pressure Chillers
Compressor
Function and Types: The compressor in a low pressure chiller is responsible for increasing the pressure and temperature of the refrigerant vapor. Different types of compressors are used depending on the specific requirements of the chiller. Screw compressors are common in larger low pressure chiller applications. They operate by meshing two helical rotors, which trap and compress the refrigerant gas as the rotors turn. Reciprocating compressors, with their piston – cylinder arrangement, are also used, especially in smaller – scale or more specialized low pressure chiller setups. The choice of compressor type depends on factors such as the required cooling capacity, the type of refrigerant used, and the overall design of the chiller system.
Adaptations for Low – Pressure Operation: Compressors in low pressure chillers are often designed with specific features to handle the low – pressure refrigerant flow. They may have larger displacement volumes to accommodate the larger volume of low – pressure refrigerant gas. The internal components are engineered to withstand the unique pressure and temperature conditions associated with low – pressure refrigeration cycles. For example, the seals and bearings in the compressor are designed to prevent refrigerant leakage and ensure smooth operation at lower pressures.
Condenser
Heat Rejection Mechanisms: The condenser in a low pressure chiller is where the high – pressure, high – temperature refrigerant vapor releases its heat and condenses back into a liquid state. There are two main types of condensers used in low pressure chillers: air – cooled and water – cooled. Air – cooled condensers use ambient air to dissipate heat. The hot refrigerant vapor passes through a series of fins and tubes, and fans blow air over these surfaces to transfer heat from the refrigerant to the air. Water – cooled condensers, on the other hand, use water as a heat sink. The refrigerant releases heat to the water, which is then typically cooled in a cooling tower or a similar water – cooling system.
Design Considerations for Low Pressure: In low pressure chiller applications, the design of the condenser needs to account for the lower pressure and temperature of the refrigerant. The heat – transfer surfaces in the condenser are optimized to ensure efficient heat transfer at these lower conditions. For air – cooled condensers, the fin design and the size of the fan are carefully selected to maximize the cooling effect. In water – cooled condensers, the water flow rate and the heat – exchanger design are adjusted to effectively remove heat from the refrigerant.
Evaporator
Heat Absorption Process: The evaporator is the component where the refrigerant absorbs heat from the medium that needs to be cooled, such as water in a chilled water system. In a low pressure chiller, the low – pressure liquid refrigerant enters the evaporator and absorbs heat from the warm water or other cooling medium. As the refrigerant absorbs heat, it evaporates and turns into a low – pressure vapor. The evaporator is designed with a large surface area to enhance the heat – transfer process. It typically consists of a coil of tubes through which the refrigerant flows, and the warm medium being cooled passes over or through these tubes.
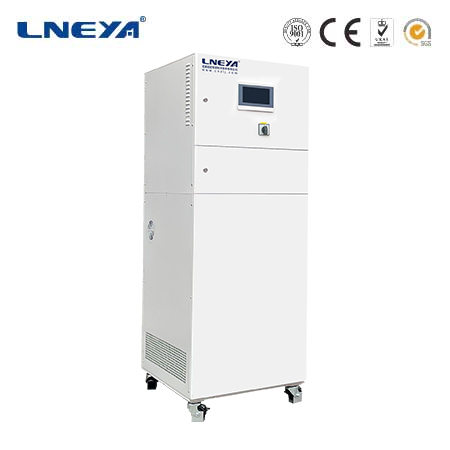
Optimization for Low – Pressure Refrigerants: Since low pressure refrigerants have different thermophysical properties compared to high – pressure refrigerants, the evaporator in a low pressure chiller is optimized accordingly. The tube material, diameter, and length are carefully selected to ensure proper refrigerant flow and heat transfer. In some cases, the evaporator may be designed with enhanced heat – transfer features, such as micro – channels or finned surfaces, to improve the efficiency of heat absorption.
Expansion Valve
Pressure Reduction and Flow Control: The expansion valve in a low pressure chiller serves two main functions: it reduces the pressure of the high – pressure liquid refrigerant as it enters the evaporator, and it controls the flow rate of the refrigerant. Thermostatic expansion valves are commonly used in low pressure chiller systems. These valves regulate the refrigerant flow based on the temperature of the refrigerant vapor leaving the evaporator. If the temperature is too high, the valve opens wider to allow more refrigerant to flow into the evaporator, and if the temperature is too low, the valve closes slightly to reduce the flow. This helps to maintain the optimal cooling performance of the chiller.
Compatibility with Low – Pressure Systems: Expansion valves in low pressure chillers need to be compatible with the low – pressure refrigerants and the overall system pressure range. They are designed to accurately control the pressure drop and refrigerant flow at low pressures. The internal components of the expansion valve, such as the diaphragm, spring, and orifice, are sized and calibrated to work effectively in a low – pressure environment.
Working Principles
Refrigeration Cycle
Evaporation: The refrigeration cycle in a low pressure chiller begins with the low – pressure liquid refrigerant entering the evaporator. In the evaporator, the refrigerant absorbs heat from the medium being cooled, such as water in a chilled water loop. As the refrigerant absorbs heat, it evaporates and turns into a low – pressure vapor. This evaporation process cools down the water, which is then circulated to the areas or processes that require cooling.
Compression: The low – pressure refrigerant vapor then enters the compressor. The compressor increases the pressure and temperature of the refrigerant vapor. This compression process is essential as it raises the temperature of the refrigerant above that of the ambient environment or the cooling medium in the condenser, allowing for efficient heat rejection.
Condensation: The high – pressure, high – temperature refrigerant vapor then travels to the condenser. In the condenser, the refrigerant releases its heat to the surrounding environment (either air or water). As the refrigerant releases heat, it condenses back into a high – pressure liquid state. The heat – transfer process in the condenser is crucial for the overall efficiency of the chiller.
Expansion: The high – pressure liquid refrigerant then passes through the expansion valve. The expansion valve reduces the pressure of the refrigerant, causing it to expand and cool down. The low – pressure liquid refrigerant then enters the evaporator again to start the cycle over.
Heat Transfer Mechanisms
Evaporator Heat Transfer: In the evaporator, heat is transferred from the warmer medium (e.g., water) to the cooler refrigerant. The rate of heat transfer depends on several factors, including the temperature difference between the two substances, the surface area of the evaporator, and the thermal conductivity of the materials involved. The design of the evaporator is optimized to maximize the heat – transfer rate. For example, the use of enhanced heat – transfer surfaces, such as finned tubes, can increase the surface area available for heat transfer and improve the efficiency of the evaporator.
Condenser Heat Transfer: In the condenser, the heat – transfer process is reversed. Heat is transferred from the hot refrigerant to the cooler air or water. The efficiency of the condenser depends on factors such as the air or water flow rate, the surface area of the condenser, and the temperature difference between the refrigerant and the cooling medium. The design of the condenser, including the fin design in air – cooled condensers and the heat – exchanger configuration in water – cooled condensers, is optimized to ensure efficient heat transfer.
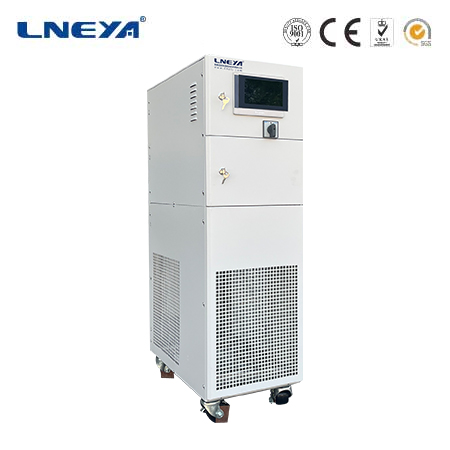
Types of Low Pressure Chillers
Air – Cooled Low Pressure Chillers
Advantages: Air – cooled low pressure chillers are popular in many applications due to their simplicity and ease of installation. They do not require a complex water – cooling infrastructure, which makes them suitable for areas where water is scarce or expensive. They are also relatively easy to maintain as there are no water – related components such as cooling towers or water pumps. In addition, air – cooled low pressure chillers can be more flexible in terms of installation location as they do not need to be close to a water source.
Limitations: However, air – cooled low pressure chillers have some limitations. In hot and humid climates, their efficiency can be reduced as the warm and humid air may not be as effective in cooling the refrigerant. The cooling capacity of air – cooled low pressure chillers is also generally limited compared to larger water – cooled chillers. They may require a larger footprint due to the need for sufficient air circulation around the condenser.
Water – Cooled Low Pressure Chillers
Advantages: Water – cooled low pressure chillers offer higher energy efficiency compared to air – cooled models, especially in hot and humid environments. Water is a more effective heat sink than air, allowing for better heat transfer in the condenser. This can result in lower condensing temperatures and reduced compressor work, leading to energy savings. Water – cooled low pressure chillers are also capable of handling larger cooling loads, making them suitable for large – scale industrial and commercial applications.
Disadvantages: The main disadvantage of water – cooled low pressure chillers is their complexity. They require a reliable water supply, a cooling tower or other water – cooling system, and proper water treatment to prevent corrosion and fouling in the chiller’s components. The installation and maintenance of water – cooled low pressure chillers are more involved and costly compared to air – cooled models. There is also a risk of water leakage, which can cause damage to the chiller and the surrounding area if not properly managed.
Absorption Low Pressure Chillers
Working Principle: Absorption low pressure chillers operate on a different principle compared to compression – based chillers. They use a heat – driven process instead of mechanical compression. In an absorption chiller, a refrigerant (such as water – lithium bromide or ammonia – water) is absorbed by an absorbent. Heat is then applied to the absorbent – refrigerant solution in the generator, causing the refrigerant to vaporize. The refrigerant vapor then goes through the condenser, evaporator, and absorber, similar to a compression – based chiller, but without the need for a mechanical compressor.
Applications and Benefits: Absorption low pressure chillers are often used in applications where there is a readily available source of waste heat, such as in industrial plants or power generation facilities. By using waste heat to drive the cooling process, absorption low pressure chillers can achieve high energy efficiency and reduce the overall energy consumption of the facility. They are also suitable for applications where noise and vibration from a mechanical compressor are a concern, as they operate more quietly. However, absorption low pressure chillers are generally more complex and expensive to install and maintain compared to compression – based low pressure chillers.
Applications of Low Pressure Chillers
Industrial Processes
Manufacturing Plants: In manufacturing plants, low pressure chillers are used to cool various processes and equipment. For example, in the plastics industry, they are used to cool injection molding machines. These machines generate a significant amount of heat during the molding process, and low pressure chillers help maintain the optimal temperature for the plastic materials to solidify properly. In the chemical industry, low pressure chillers are used to cool reactors, ensuring that chemical reactions occur at the right temperature and preventing overheating, which could lead to safety hazards or incorrect reaction outcomes.
Food and Beverage Industry: The food and beverage industry relies heavily on low pressure chillers for cooling and refrigeration. In food processing plants, low pressure chillers are used to cool products during processing, storage, and transportation. For example, in a dairy plant, low pressure chillers are used to cool milk and other dairy products to prevent spoilage. In a brewery, low pressure chillers are used to cool the fermentation vessels and maintain the proper temperature for yeast growth and beer production.
Commercial Buildings (HVAC Systems)
Office Buildings: In office buildings, low pressure chillers are used to provide chilled water for the building’s HVAC system. The chilled water is circulated through air – handling units to cool the indoor air, providing a comfortable working environment for employees. Low pressure chillers can be sized according to the cooling load of the building, and their energy – efficient operation can result in significant cost savings on electricity bills.
Shopping Malls and Retail Spaces: Shopping malls and large retail spaces require substantial cooling to maintain a comfortable environment for customers. Low pressure chillers are used to cool the large indoor areas, and their ability to handle large cooling loads makes them suitable for these applications. In addition, the energy – efficiency of low pressure chillers can help reduce the operating costs of the mall or retail space.
Data Centers
Server Cooling: Data centers generate a large amount of heat due to the continuous operation of servers and other electronic equipment. Low pressure chillers are essential for cooling these facilities. They cool the water that is used to cool the air around the servers, preventing server overheating, which can lead to hardware failures and data loss. The high – capacity and energy – efficient low pressure chillers are well – suited for the demanding cooling requirements of data centers.
Reliability and Redundancy: In data centers, reliability is of utmost importance. Low pressure chillers can be configured in redundant systems to ensure continuous cooling in case of a chiller failure. Multiple low pressure chillers can be installed in parallel, and control systems can be used to manage the operation of the chillers, ensuring that the cooling load is met even if one or more chillers malfunction.
Advantages of Low Pressure Chillers
Energy Efficiency
Lower Compressor Work: The operation of low pressure chillers often results in lower compressor work compared to high – pressure chiller systems. The lower pressure ratio across the compressor in low pressure chillers means that the compressor consumes less energy to compress the refrigerant. This can lead to significant energy savings, especially in applications where the chiller operates continuously or for long periods.
Optimized Heat Transfer: The design of low pressure chillers is optimized for efficient heat transfer. The use of appropriate heat – transfer surfaces in the evaporator and condenser, as well as the selection of the right refrigerant, allows for better heat transfer between the refrigerant and the medium being cooled or the cooling medium. This optimized heat transfer process contributes to the overall energy efficiency of the chiller.
Environmental Benefits
Use of Natural Refrigerants: Many low pressure chillers can use natural refrigerants such as ammonia or hydrocarbons. These natural refrigerants have a much lower global warming potential (GWP) compared to many synthetic refrigerants used in traditional chiller systems. For example, ammonia has a GWP close to zero. By using natural refrigerants, low pressure chillers can significantly reduce their environmental impact and contribute to global efforts to mitigate climate change.
Reduced Energy Consumption: The energy – efficient operation of low pressure chillers also leads to reduced energy consumption. Since most electricity generation in many regions is associated with greenhouse gas emissions, the lower energy consumption of low pressure chillers results in a lower carbon footprint. This is beneficial for both the environment and the operating costs of the facility using the chiller.
Large Cooling Capacity
Suitability for High – Load Applications: Low pressure chillers are well – suited for applications with large cooling loads. Their design allows for the efficient handling of large volumes of refrigerant, which can transfer a significant amount of heat. In industrial plants, large commercial buildings, and data centers, low pressure chillers can provide the necessary cooling capacity to meet the demands of the processes or occupants.
Considerations when Choosing a Low Pressure Chiller
Refrigerant Selection
Safety and Environmental Impact: The choice of refrigerant in a low pressure chiller is crucial. Natural refrigerants, while offering environmental benefits, may have safety concerns. For example, ammonia is toxic and requires strict safety measures during handling, storage, and installation. Hydrocarbons are flammable, so proper safety protocols need to be in place. Synthetic low – pressure refrigerants may also be available, but their environmental impact, such as their GWP, needs to be carefully evaluated. The selection of refrigerant should be based on factors such as the application requirements, safety regulations, and environmental considerations.
Compatibility with Components: The refrigerant selected must be compatible with the components of the low pressure chiller. Different refrigerants have different thermophysical properties, and these properties can affect the performance and lifespan of the compressor, condenser, evaporator, and expansion valve. For example, some refrigerants may require specific materials for the compressor seals and the heat – exchanger surfaces to prevent corrosion and ensure proper operation.
Installation and Space Requirements
Size and Footprint: Low pressure chillers, especially larger models, can be quite large and require a significant amount of space for installation. The size and footprint of the chiller should be carefully considered when planning the installation location. In addition, the installation area should provide sufficient space for access to the chiller for maintenance and servicing.
Location and Ventilation: The location of the low pressure chiller is also important. For air – cooled chillers, proper ventilation is essential to ensure efficient heat transfer in the condenser. The chiller should be installed in an area where there is good air circulation and away from sources of heat or contaminants that could affect its performance. For water – cooled chillers, the installation location should be close to a reliable water supply and a suitable location for the cooling tower or water – cooling system.
Related recommendations
chiller layout
189Understanding Chiller Layout A chiller layout is the configuration of components within a chiller system, designed to optimize cooling efficiency and performance. Chiller systems are essential ...
View detailsWhat should I do if there is a water flow problem with a 50 ton chiller?
724What should I do if there is a water flow problem with a 50 ton chiller? The first question: What should I do if there is a water flow malfunction in a 50 ton chiller? 1. First, ...
View detailschiller for injection molding machine
123Chiller for Injection Molding Machine: Enhancing Efficiency and Quality Industrial chillers are crucial components in the injection molding process, providing precise temperature control to ens...
View details20 ton chiller
13A 20 - ton chiller is a powerful cooling system used in various applications to remove heat from a space or process. The “20 - ton” rating is a measure of its cooling capacity. Specifically, it me...
View details
HelloPlease log in