low temp chillers
In many industrial and scientific applications, the need for cooling below normal ambient temperatures is essential. Low – temp chillers are designed to meet this requirement, providing a reliable and efficient way to achieve and maintain sub – zero temperatures. These chillers are not just modified versions of standard chillers; they are engineered with specific components and operating principles to function optimally in low – temperature environments.
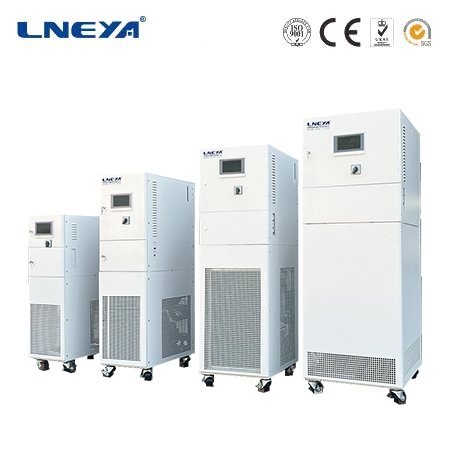
Components of Low – Temp Chillers
Compressors
Specialized Compressor Types: Low – temp chillers often use compressors that are specifically designed for the demands of low – temperature operation. Screw compressors are commonly employed due to their ability to handle a wide range of pressure ratios and maintain efficient operation at low temperatures. They can provide a stable flow of refrigerant, which is crucial for consistent cooling performance. For example, in a large – scale food freezing facility, screw compressors can handle the high – volume refrigerant flow required to rapidly cool large quantities of food products.
Compressor Lubrication: Lubrication is a critical aspect in low – temp compressors. The lubricating oil needs to maintain its viscosity at low temperatures to ensure proper functioning of the compressor’s moving parts. Specialized lubricants are used that have a low pour point, meaning they do not thicken or solidify at the low temperatures encountered in these chillers. This ensures smooth operation and reduces wear and tear on the compressor components.
Condensers
Air – Cooled Condensers: In some low – temp chiller applications, air – cooled condensers can be used, especially in environments where water availability is limited or where the heat load is relatively small. However, in cold climates, the performance of air – cooled condensers can be affected by the already low ambient air temperature. To address this, some air – cooled condensers in low – temp chillers are equipped with variable – speed fans. The fans can adjust their speed based on the temperature difference between the refrigerant and the ambient air, optimizing the heat – transfer process.
Water – Cooled Condensers: Water – cooled condensers are more commonly used in low – temp chillers for larger – scale applications. They offer higher heat – transfer efficiency compared to air – cooled condensers. In a water – cooled condenser, the refrigerant releases heat to the water, which is then typically cooled in a cooling tower. The design of water – cooled condensers for low – temp chillers needs to account for the low – temperature operation. For instance, the materials used in the condenser tubes need to be resistant to corrosion and embrittlement at low temperatures.
Evaporators
Finned – Tube Evaporators: Finned – tube evaporators are widely used in low – temp chillers. The fins increase the surface area of the evaporator, enhancing heat transfer between the refrigerant and the fluid being cooled. In applications such as food freezing, the finned – tube evaporators are designed to quickly transfer heat from the food products to the refrigerant, enabling rapid freezing. The spacing and design of the fins are optimized to prevent ice buildup, which can reduce heat – transfer efficiency.
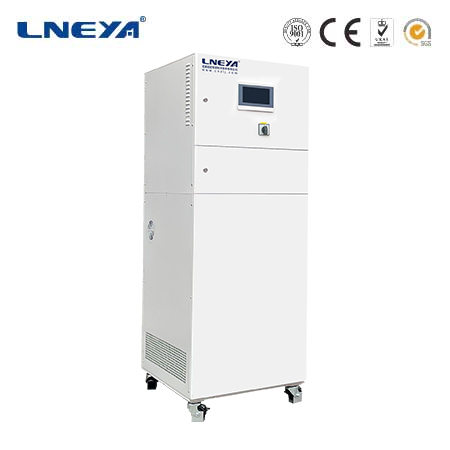
Plate – Type Evaporators: Plate – type evaporators are also used in some low – temp chiller applications. They consist of a series of thin metal plates with corrugated surfaces. The glycol – water mixture (in indirect – expansion systems) or the fluid being cooled flows between alternate plates. Plate – type evaporators offer high heat – transfer efficiency in a compact design, making them suitable for applications where space is limited, such as in some laboratory – based low – temp cooling setups.
Expansion Devices
Thermal Expansion Valves: Thermal expansion valves are commonly used in low – temp chillers to regulate the flow of refrigerant into the evaporator. These valves adjust the refrigerant flow based on the temperature of the refrigerant leaving the evaporator. In low – temperature applications, the thermal expansion valves need to be carefully calibrated to ensure proper refrigerant distribution. For example, in a pharmaceutical manufacturing process where precise temperature control is crucial, an accurately calibrated thermal expansion valve can help maintain the desired low temperature within a narrow range.
Electronic Expansion Valves: Electronic expansion valves are becoming increasingly popular in low – temp chillers. They offer more precise control over the refrigerant flow compared to thermal expansion valves. Electronic expansion valves can adjust the flow rate based on multiple parameters, such as temperature, pressure, and the load on the chiller. This allows for better optimization of the chiller’s performance, especially in applications where the cooling load may vary significantly.
Types of Low – Temp Chillers
Direct – Expansion Low – Temp Chillers
Working Principle: In direct – expansion low – temp chillers, the refrigerant evaporates directly in the evaporator coil, which is in direct contact with the fluid or space being cooled. This type of chiller offers a fast cooling response as there is no intermediate heat – transfer fluid. For example, in a small – scale laboratory freezer, a direct – expansion low – temp chiller can quickly cool the samples placed inside the freezer compartment.
Applications: Direct – expansion low – temp chillers are commonly used in applications where rapid cooling is required, such as in food display freezers in grocery stores. They can maintain the low temperatures necessary to keep food products frozen while also providing quick cooling when new products are added to the display.
Indirect – Expansion Low – Temp Chillers
Working Principle: Indirect – expansion low – temp chillers use a secondary coolant, such as a glycol – water mixture. The refrigerant cools the secondary coolant in a heat exchanger, and then the cooled secondary coolant is circulated to the area or process that needs to be cooled. This setup provides an extra layer of protection, as the refrigerant is not in direct contact with the area being cooled. In applications where there is a risk of refrigerant leakage and contamination, such as in pharmaceutical manufacturing, indirect – expansion low – temp chillers are preferred.
Applications: Indirect – expansion low – temp chillers are widely used in large – scale food storage facilities. The secondary coolant can be circulated through a network of pipes in the storage area to maintain a uniform low temperature throughout the space, ensuring the proper preservation of food products.
Applications of Low – Temp Chillers
Pharmaceutical Industry
Drug Storage and Manufacturing: In the pharmaceutical industry, low – temp chillers are used for both drug storage and manufacturing processes. Many medications, such as vaccines and certain biologics, need to be stored at low temperatures to maintain their efficacy. Low – temp chillers are used in warehouses and distribution centers to ensure that the drugs are kept within the required temperature range. During the manufacturing process, low – temp chillers are used to control the temperature of chemical reactions. For example, in the synthesis of some drugs, precise low – temperature control is necessary to ensure the correct chemical structure and purity of the final product.
Stability Testing: Low – temp chillers are also used in pharmaceutical stability testing. These tests are conducted to determine how a drug product will degrade over time under different storage conditions. By using low – temp chillers to maintain specific low temperatures, pharmaceutical companies can predict the shelf – life of their products and ensure their quality and safety.
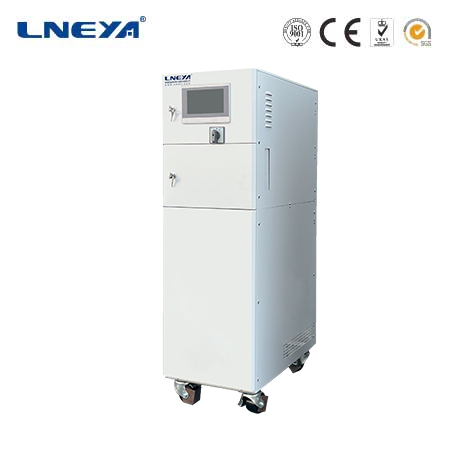
Food Industry
Freezing and Preservation: The food industry is one of the major users of low – temp chillers. In food freezing plants, low – temp chillers are used to rapidly freeze food products, such as meat, fish, and vegetables. Rapid freezing helps to preserve the quality, texture, and nutritional value of the food. Low – temp chillers are also used in cold storage warehouses to maintain the frozen state of food products during storage and distribution.
Beverage Production: In the beverage industry, low – temp chillers are used for cooling during the production process. For example, in the brewing industry, low – temp chillers are used to cool the wort (the liquid extracted from the mashing process) before fermentation. This helps to control the fermentation process and ensure the production of high – quality beer.
Scientific Research
Cryogenic Experiments: In scientific research, low – temp chillers are used in cryogenic experiments. Cryogenics involves the study of materials and processes at very low temperatures. Low – temp chillers can provide the necessary cooling to reach temperatures close to absolute zero. For example, in superconducting research, low – temp chillers are used to cool superconducting materials to the low temperatures required for them to exhibit zero electrical resistance.
Biological Research: In biological research, low – temp chillers are used for storing biological samples, such as cell lines and tissues. These samples need to be stored at low temperatures to preserve their viability. Low – temp chillers are also used in some biological experiments that require precise temperature control at low temperatures, such as in the study of enzyme activity at cold temperatures.
Design Considerations for Low – Temp Chillers
Refrigerant Selection
Low – Boiling – Point Refrigerants: Low – temp chillers require refrigerants with low boiling points to achieve the desired low temperatures. Refrigerants such as R – 404A, R – 507, and ammonia are commonly used in low – temp applications. These refrigerants can evaporate and absorb heat at very low temperatures. For example, ammonia has a boiling point of -33.3°C at standard atmospheric pressure, making it suitable for applications where extremely low temperatures are required.
Environmental Impact: In addition to their low – boiling – point properties, the environmental impact of refrigerants is also a consideration. Older refrigerants, such as chlorofluorocarbons (CFCs) and hydrochlorofluorocarbons (HCFCs), are being phased out due to their ozone – depleting properties. Newer refrigerants, such as hydrofluoroolefins (HFOs), are being developed and used in low – temp chillers as they have a lower global warming potential (GWP) while still maintaining the necessary thermodynamic properties for low – temperature operation.
Insulation
High – Performance Insulation Materials: Proper insulation is crucial in low – temp chillers to minimize heat gain from the surrounding environment. High – performance insulation materials, such as polyurethane foam and expanded polystyrene, are used. These materials have low thermal conductivity, which helps to keep the cold inside the chiller and prevent heat from entering. In a food freezing facility, thick layers of insulation are applied to the walls of the freezer rooms and the pipes carrying the refrigerant and secondary coolant to reduce heat transfer and energy consumption.
Insulation Installation: The installation of insulation in low – temp chillers needs to be carefully done to ensure there are no gaps or leaks. Any gaps in the insulation can allow heat to penetrate, reducing the efficiency of the chiller and increasing the energy required to maintain the low temperature. Special attention is paid to the joints and connections in the insulation to ensure a continuous and effective thermal barrier.
System Control
Precise Temperature Control: Low – temp chillers require precise temperature control to meet the specific needs of their applications. Advanced control systems are used that can monitor and adjust the temperature within a very narrow range. These control systems use temperature sensors placed at various points in the chiller, such as at the inlet and outlet of the evaporator and in the area being cooled. The controller then adjusts the operation of the compressor, expansion valve, and fans (if applicable) to maintain the desired temperature.
Safety Controls: Safety controls are also an important part of the design of low – temp chillers. These include high – and low – pressure switches to protect the compressor from over – pressure or under – pressure conditions. In addition, temperature – limit switches are installed to prevent the chiller from operating at temperatures outside the safe range. In a pharmaceutical manufacturing plant, these safety controls are essential to ensure the integrity of the drug – manufacturing process and the safety of the personnel working with the chiller.
Advantages of Low – Temp Chillers
Precise Temperature Control
Critical for Applications: In applications such as pharmaceutical manufacturing and scientific research, precise temperature control is crucial. Low – temp chillers can maintain temperatures within a very narrow range, often within ±0.1°C or even less. This level of precision ensures that the chemical reactions in pharmaceutical manufacturing proceed as intended and that the biological samples in research laboratories are properly preserved.
Consistent Product Quality: In the food industry, precise temperature control in low – temp chillers helps to ensure consistent product quality. For example, in ice – cream production, maintaining a consistent low temperature during the freezing process results in a smooth and creamy texture. In frozen food production, precise temperature control helps to prevent the formation of large ice crystals, which can damage the texture and quality of the food.
Reliable Performance in Cold Conditions
Designed for Low – Temperature Operation: Low – temp chillers are specifically designed to operate in cold conditions. Their components, such as compressors, condensers, and evaporators, are engineered to function optimally at low temperatures. This reliability is essential in applications where continuous cooling is required, such as in 24 – hour food storage facilities or in scientific experiments that run for extended periods.
Reduced Downtime: The reliable performance of low – temp chillers reduces downtime. In industries where downtime can result in significant losses, such as in the pharmaceutical and food industries, the ability of low – temp chillers to operate continuously without failure is a major advantage. Regular maintenance and the use of high – quality components contribute to the reliable performance of these chillers.
Disadvantages and Considerations
High Energy Consumption
Demands of Low – Temperature Cooling: Achieving and maintaining low temperatures requires a significant amount of energy. The compressors in low – temp chillers need to work harder to compress the refrigerant to the high pressures required for low – temperature operation. In addition, the fans and pumps in the chiller system also consume energy. In a large – scale food freezing plant, the energy consumption of the low – temp chillers can be a major operating cost.
Energy – Efficiency Improvements: However, efforts are being made to improve the energy efficiency of low – temp chillers. The use of variable – speed drives for compressors, fans, and pumps can help to reduce energy consumption by adjusting the speed of these components based on the actual cooling load. In addition, the development of more efficient refrigerants and better insulation materials is also contributing to energy savings in low – temp chiller operation.
Maintenance Requirements
Component Wear and Tear: The components in low – temp chillers are subject to wear and tear due to the harsh operating conditions. The compressors, in particular, can experience increased stress at low temperatures. Regular maintenance, including lubrication of moving parts, inspection of refrigerant lines for leaks, and cleaning of condensers and evaporators, is necessary to ensure the proper functioning of the chiller. In a food freezing facility, maintenance may be scheduled on a monthly or quarterly basis depending on the usage and operating conditions of the chiller.
Refrigerant Management: Refrigerant management is also an important aspect of maintenance. The refrigerant levels need to be monitored regularly, and any leaks need to be repaired promptly. In addition, the quality of the refrigerant may degrade over time, and it may need to be replaced. In some cases, the refrigerant may need to be recycled or disposed of properly in accordance with environmental regulations.
In conclusion, low – temp chillers are essential components in many industries and scientific research applications. Understanding their components, types, applications, design considerations, advantages, and disadvantages is crucial for their effective use. As technology continues to advance, low – temp chillers are expected to become more energy – efficient and reliable, further enhancing their role in various fields.
Related recommendations
cold water chillers
203Cold Water Chillers: Efficient Cooling for Diverse Industries Cold water chillers are vital components in temperature control systems, used across a variety of industries for cooling processes,...
View detailsindustrial water chiller india
166Industrial Water Chiller India: Market Expansion and Technological Advancements India's industrial sector is experiencing significant growth, with a consequent increase in the demand for indust...
View details1 ton water chiller price
212Understanding the Price of a 1-Ton Water Chiller A 1-ton water chiller is an essential piece of equipment for cooling applications in various industries, including commercial HVAC systems and i...
View detailsWhat temperature sensors are commonly used for lab water chiller?
823What temperature sensors are commonly used for lab water chiller? Generally speaking, the temperature sensors used in laboratory chillers mainly include the following types: 1. T...
View details
HelloPlease log in