mechanical chillers
Mechanical Chillers: A Comprehensive Guide
Mechanical chillers are widely used devices that play a crucial role in providing cooling solutions across numerous sectors. They are designed to remove heat from a process or space, maintaining a desired low temperature.
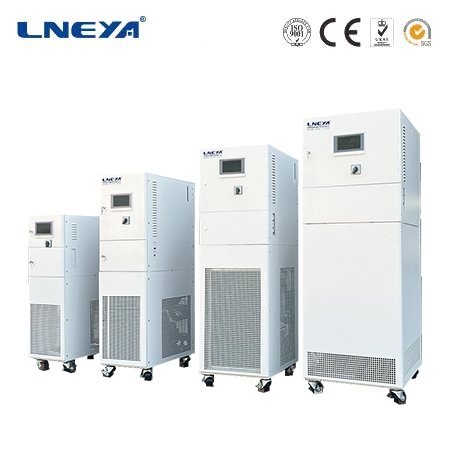
Working Principle of Mechanical Chillers
The Vapor – Compression Refrigeration Cycle
Mechanical chillers primarily operate on the vapor – compression refrigeration cycle. This cycle consists of four main processes: compression, condensation, expansion, and evaporation.
Compression: The cycle begins with a compressor. The compressor takes in low – pressure, low – temperature refrigerant vapor. As the refrigerant passes through the compressor, mechanical energy is applied to increase its pressure and temperature. The high – pressure, high – temperature refrigerant vapor is then discharged from the compressor.
Condensation: The hot refrigerant vapor enters the condenser. In the condenser, heat is transferred from the refrigerant to a cooling medium. This cooling medium can be either air (in air – cooled condensers) or water (in water – cooled condensers). As the refrigerant releases heat, it condenses into a high – pressure liquid.
Expansion: The high – pressure liquid refrigerant then passes through an expansion device, such as an expansion valve. The expansion valve reduces the pressure of the refrigerant, causing it to expand and cool down rapidly.
Evaporation: The cold, low – pressure refrigerant enters the evaporator. In the evaporator, the refrigerant absorbs heat from the substance or space that needs to be cooled. As the refrigerant absorbs heat, it vaporizes, and the cooled substance or space can then be used or further processed. The cycle then repeats continuously to maintain the cooling effect.
Types of Mechanical Chillers
Reciprocating Chillers
Operation and Features: Reciprocating chillers use a reciprocating compressor, which consists of a piston that moves back and forth within a cylinder. The piston compresses the refrigerant vapor. These chillers are known for their ability to handle a wide range of cooling loads. They are relatively simple in design and can be easily customized for specific applications. However, they tend to be more suitable for small – to – medium – sized applications due to their limited capacity compared to some other types of mechanical chillers. They also produce more vibration and noise during operation.
Applications: Reciprocating chillers are often used in small commercial buildings, such as local restaurants or small office spaces. They can provide sufficient cooling for air – conditioning systems in these buildings. In some industrial settings, they may be used for cooling small – scale processes, like in a local bakery where they can cool the dough during preparation.
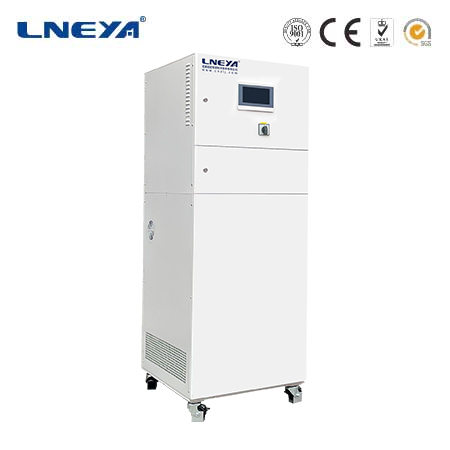
Screw Chillers
Operation and Features: Screw chillers employ a screw compressor. The compressor has two intermeshing helical screws (rotors). As the rotors rotate, the refrigerant is compressed. Screw chillers can handle larger cooling loads compared to reciprocating chillers. They offer a relatively smooth compression process, resulting in lower vibration and noise levels. Their capacity can be adjusted continuously, which is beneficial for applications where the cooling load varies. For example, they can use slide valves to modulate the compressor’s capacity.
Applications: In medium – to – large – scale commercial buildings, such as shopping malls and multi – story office complexes, screw chillers are commonly used for air – conditioning. In industrial applications, they are used to cool large – scale manufacturing processes. For instance, in a plastics manufacturing plant, screw chillers can cool the molds during injection – molding to ensure the proper shaping of plastic products.
Centrifugal Chillers
Operation and Features: Centrifugal chillers use a centrifugal compressor. The compressor consists of an impeller that rotates at high speeds. As the refrigerant enters the impeller, it is flung outward by centrifugal force, which increases its pressure. Centrifugal chillers are highly efficient for large – scale applications. They can handle very high cooling loads. They are also known for their low – maintenance requirements compared to some other types of mechanical chillers. However, they are more suitable for applications with relatively stable cooling loads.
Applications: In large industrial plants, such as chemical plants and power generation facilities, centrifugal chillers are widely used. They can provide the significant cooling capacity needed for various industrial processes. In large – scale data centers, which generate a substantial amount of heat from servers and other electronic equipment, centrifugal chillers are often installed to maintain a low and stable temperature for the proper operation of the equipment.
Applications of Mechanical Chillers
Commercial Air – Conditioning
Mechanical chillers are extensively used in commercial buildings for air – conditioning purposes. They provide chilled water to air – handling units. These units then cool and dehumidify the air in the building, creating a comfortable indoor environment for occupants. In large hotels, mechanical chillers ensure that the rooms, lobbies, and other public areas are kept at a pleasant temperature throughout the year. In shopping malls, they maintain a cool environment for customers, which is not only for comfort but also helps in preserving the quality of goods on display.
Industrial Processes
In the industrial sector, mechanical chillers are used in a wide range of processes. In the food and beverage industry, they are used to cool products during production, storage, and transportation. For example, in a brewery, mechanical chillers are used to cool the beer during fermentation and storage to maintain its taste and quality. In the pharmaceutical industry, they are used to cool reaction vessels and storage areas to ensure the stability of drugs and the proper functioning of manufacturing processes. In manufacturing plants, they are used to cool machinery, such as metal – cutting tools, to prevent overheating and ensure accurate machining.
Data Centers
Data centers generate a large amount of heat due to the continuous operation of servers and other electronic equipment. Mechanical chillers are essential for cooling these facilities. They maintain a low and stable temperature, typically around 20 – 25 °C, to prevent overheating of the servers. Overheating can lead to equipment failure and data loss. Mechanical chillers help in ensuring the reliable operation of data centers, which are crucial for various industries, including finance, technology, and entertainment.
Advantages and Limitations of Mechanical Chillers
Advantages
High Cooling Capacity: Mechanical chillers, especially screw and centrifugal types, can provide a high cooling capacity, making them suitable for large – scale applications where significant amounts of heat need to be removed.
Relatively Fast Cooling Speed: They can quickly reduce the temperature of the substance or space to be cooled. This is beneficial in applications where rapid cooling is required, such as in some industrial processes where the temperature needs to be adjusted promptly to control the reaction.
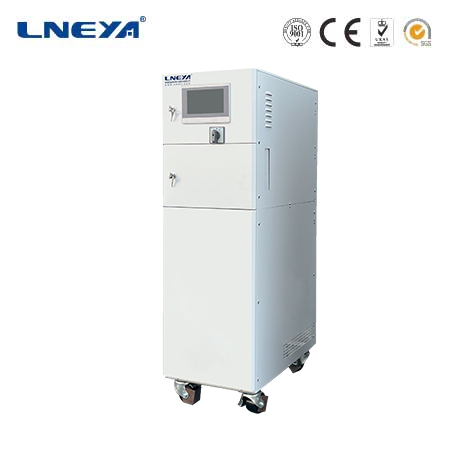
Flexibility in Application: Different types of mechanical chillers can be selected based on the specific requirements of the application. For example, reciprocating chillers are suitable for small – scale applications, while screw and centrifugal chillers can handle medium – to – large – scale applications.
Limitations
High Energy Consumption: Mechanical chillers, especially those with large cooling capacities, consume a significant amount of energy. This can result in high operating costs, especially in regions with high electricity prices. The compressor, which is a major energy – consuming component, requires a substantial amount of power to operate.
Complex Maintenance: They require regular and often complex maintenance. Components such as compressors, condensers, and expansion valves need to be inspected, serviced, and repaired as necessary. The maintenance of mechanical chillers often requires trained technicians due to the complexity of the refrigeration cycle and the mechanical components involved.
Maintenance of Mechanical Chillers
Regular Inspection of Components
The compressor, being a critical component, should be inspected regularly. This includes checking for signs of wear and tear, such as in the pistons of reciprocating compressors or the rotors of screw and centrifugal compressors. The oil levels in the compressor should also be monitored and changed as per the manufacturer’s recommendations.
The condenser, whether air – cooled or water – cooled, needs to be inspected. In air – cooled condensers, the fins should be checked for dirt and debris, which can impede heat transfer. In water – cooled condensers, the tubes should be inspected for scaling and corrosion.
The expansion device should be checked to ensure proper operation. It may need to be adjusted or replaced if it is not regulating the refrigerant flow correctly.
Refrigerant Management
Monitoring the refrigerant levels is crucial. Low refrigerant levels can indicate a leak, which should be promptly detected and repaired. Over – charging or under – charging the refrigerant can also affect the performance and efficiency of the chiller. In addition, the quality of the refrigerant should be maintained, and any contaminants should be removed.
Electrical System Maintenance
The electrical components of the mechanical chiller, including wiring, switches, and motors, should be inspected regularly. Loose connections can cause electrical problems and affect the operation of the chiller. The motors should be checked for proper rotation and alignment, and their bearings should be lubricated as needed.
In conclusion, mechanical chillers are essential for a wide range of applications. Understanding their working principle, types, applications, advantages, limitations, and maintenance requirements is crucial for effectively using and maintaining these devices to meet cooling needs efficiently.
Related recommendations
ac glycol chiller
74All about AC Glycol ChillersAC glycol chillers are a specialized type of chiller system that uses a mixture of glycol and water as the heat - transfer fluid. This combination offers distinct advan...
View detailsWhat details should be paid attention to in the daily maintenance and upkeep of industrial air cooled chiller?
761What details should be paid attention to in the daily maintenance and upkeep of industrial air cooled chiller? 1. When starting an air-cooled industrial chiller unit, it should be check...
View detailsglycol cooler unit
61Glycol Cooler Unit: A Comprehensive OverviewA glycol cooler unit is a specialized piece of equipment that plays a vital role in heat transfer processes across different sectors. At its core, it ut...
View detailsportable industrial chiller
199Portable Industrial Chiller: Versatile Cooling Solutions for Industrial Applications Portable industrial chillers, also known as portable cooling units, are essential in providing flexible and ...
View details
HelloPlease log in