portable chiller units
Introduction
In an era where adaptability and convenience are highly valued, portable chiller units have emerged as a practical cooling solution. Unlike traditional, fixed – installation chillers, portable units can be easily moved and deployed as needed, making them suitable for a wide range of scenarios. From providing emergency cooling in case of equipment breakdowns to cooling small – scale industrial processes and temporary event spaces, portable chiller units offer versatility and efficiency. This article aims to explore all aspects of portable chiller units, including their design, operation, applications, and how to choose the right one for specific requirements.
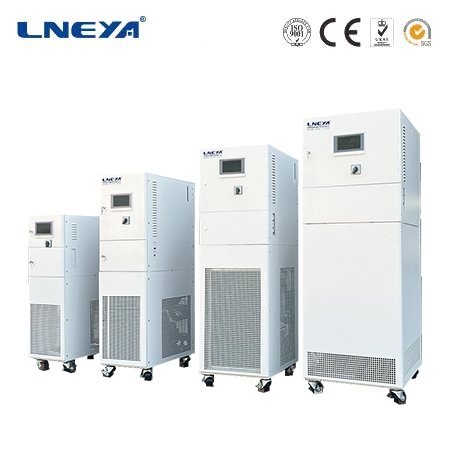
Working Principles
The Refrigeration Cycle Basics
At the core of portable chiller units is the refrigeration cycle, which is similar to that of larger, non – portable chillers. It consists of four main stages: compression, condensation, expansion, and evaporation.
Compression: The cycle starts with the compressor. The compressor takes in low – pressure, low – temperature refrigerant gas. Using mechanical energy, it compresses the gas, increasing its pressure and temperature significantly. This step is crucial as it raises the energy level of the refrigerant, preparing it for heat release in the next stage.
Condensation: The high – pressure, high – temperature refrigerant gas then enters the condenser. In air – cooled portable chillers, fans blow ambient air over the condenser coils to dissipate heat. In water – cooled models, a secondary water source is used to remove heat from the refrigerant. As the refrigerant releases heat, it condenses back into a liquid state.
Expansion: The liquid refrigerant passes through an expansion valve or capillary tube. Here, there is a sudden drop in pressure, causing the refrigerant to cool down rapidly and turn into a low – pressure, low – temperature liquid – vapor mixture.
Evaporation: The cooled refrigerant mixture enters the evaporator. In the evaporator, it absorbs heat from the medium that needs to be cooled, such as water or air. As the refrigerant absorbs heat, it evaporates back into a gas, creating the cooling effect. The refrigerant gas then returns to the compressor to start the cycle again.
Heat Transfer Mechanisms
Portable chiller units rely on efficient heat transfer to function effectively. In the condenser, heat is transferred from the refrigerant to the cooling medium (air or water) through conduction and convection. The condenser coils, often made of materials with good thermal conductivity like copper, allow heat to transfer from the refrigerant inside the coils to the outer surface. Convection then takes over as the cooling medium (air or water) flows over the coils, carrying away the heat.
In the evaporator, the heat transfer process is reversed. The heat from the medium being cooled is transferred to the refrigerant through conduction. As the refrigerant absorbs heat and evaporates, it creates a cooling effect on the surrounding medium. Proper design and maintenance of the heat transfer components are essential for the optimal performance of portable chiller units.
Types of Portable Chiller Units
Air – Cooled Portable Chillers
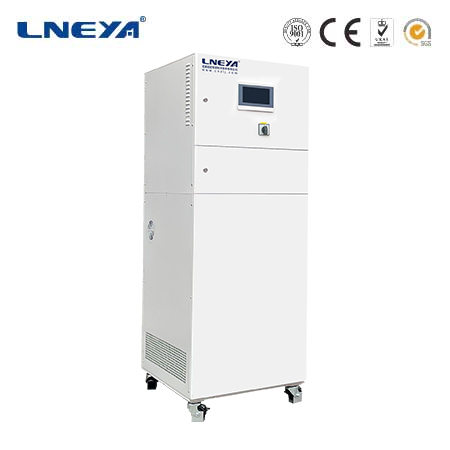
Design and Operation: Air – cooled portable chillers are the most common type. They are designed with an air – cooled condenser, which uses fans to blow ambient air over the condenser coils for heat dissipation. These units are self – contained and do not require a separate water supply for cooling, making them highly portable and easy to install. They typically come with wheels or handles for easy movement. The compressor, condenser, evaporator, and other components are housed in a single enclosure.
Advantages: Their simplicity and lack of dependence on a water source make air – cooled portable chillers suitable for a wide range of applications. They can be quickly deployed in areas where water – cooling infrastructure is not available, such as construction sites, outdoor events, or small workshops. They are also relatively easy to maintain, as there is no need to worry about water treatment or plumbing issues.
Limitations: However, air – cooled portable chillers are generally less efficient than water – cooled models, especially in hot and humid environments. The fans can generate noise, which may be a concern in some settings. Additionally, their cooling capacity is often limited compared to larger, fixed – installation chillers.
Water – Cooled Portable Chillers
Design and Operation: Water – cooled portable chillers use a secondary water source, such as a water tank or a connection to a building’s water supply, to cool the refrigerant in the condenser. They usually have a pump to circulate the water through the condenser coils. The heat from the refrigerant is transferred to the water, which then needs to be cooled, often through a cooling tower or a heat exchanger. Water – cooled portable chillers can offer higher cooling capacities and better energy efficiency compared to air – cooled models.
Advantages: These units are more suitable for applications that require higher cooling loads or more consistent cooling performance. They can operate more efficiently in hot environments as water has a higher heat – carrying capacity than air. Water – cooled portable chillers are commonly used in industrial settings, data centers, and laboratories where precise temperature control is crucial.
Limitations: On the downside, water – cooled portable chillers are more complex and require a reliable water source. They also need additional components such as pumps, hoses, and sometimes cooling towers, which can increase the cost and complexity of installation and maintenance. There is also a risk of water leakage, which can cause damage to the equipment and the surrounding area.
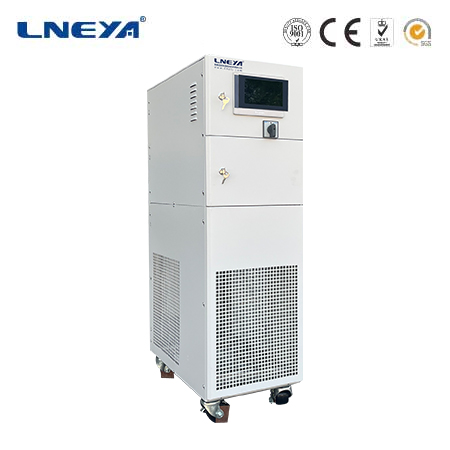
Key Features of Portable Chiller Units
Compact and Lightweight Design
One of the main features of portable chiller units is their compact and lightweight design. This allows them to be easily transported and maneuvered, even in tight spaces. Manufacturers use advanced materials and engineering techniques to reduce the size and weight of the units without sacrificing performance. For example, some portable chillers use lightweight metals and high – efficiency components to achieve a more portable form factor.
Built – in Wheels and Handles
Most portable chiller units are equipped with built – in wheels and handles for easy movement. The wheels are often designed to be durable and suitable for different types of surfaces, such as concrete, asphalt, or indoor floors. Handles are ergonomically designed to make it easy for operators to push or pull the units. Some units may also have locking mechanisms on the wheels to keep them in place when in use.
Variable Cooling Capacity
Many portable chiller units offer variable cooling capacity, allowing users to adjust the cooling output according to their specific needs. This can be achieved through various means, such as variable – speed compressors or adjustable refrigerant flow rates. Variable cooling capacity is useful as it enables the unit to operate more efficiently, saving energy when the full cooling capacity is not required.
Integrated Control Systems
Modern portable chiller units come with integrated control systems that provide easy operation and monitoring. These control systems typically include digital displays that show the current temperature, cooling capacity, and other important parameters. Users can set the desired temperature and adjust other settings using intuitive controls. Some units also have built – in safety features, such as over – temperature protection and low – refrigerant alarms, to ensure safe and reliable operation.
Applications of Portable Chiller Units
Industrial Applications
Manufacturing Processes: In manufacturing, portable chiller units can be used to cool various equipment and processes. For example, in metalworking, they can cool cutting tools, preventing overheating and extending their lifespan. In plastic injection molding, portable chillers can regulate the temperature of the molds, ensuring consistent product quality. They are also useful in electronics manufacturing, where precise temperature control is required for the production of sensitive components.
Emergency Cooling: In case of breakdowns or malfunctions of the main cooling systems in industrial plants, portable chiller units can provide emergency cooling. This helps prevent damage to expensive equipment and minimizes production downtime. They can be quickly moved to the affected area and connected to the system to restore cooling.
Commercial Applications
Events and Venues: Portable chiller units are commonly used in events such as concerts, exhibitions, and outdoor festivals. They can be used to cool food and beverage storage areas, ensuring the freshness of perishable items. In large tents or temporary structures, portable chillers can be used to create a comfortable indoor environment for attendees.
Retail and Hospitality: In the retail and hospitality industry, portable chiller units can be used for various purposes. For example, in a small restaurant or café, a portable chiller can be used to cool the kitchen equipment or the display cases for food and beverages. In hotels, they can be used for emergency cooling in case of air – conditioning system failures.
Residential and DIY Projects
Home Renovations: During home renovations, especially in situations where the existing air – conditioning system is disrupted, portable chiller units can provide temporary cooling. They can be used to cool specific rooms or areas, making the renovation process more comfortable for homeowners and workers.
DIY Cooling Solutions: For DIY enthusiasts, portable chiller units can be used to create custom cooling solutions. For example, in a home – made greenhouse, a portable chiller can be used to regulate the temperature and humidity, providing an optimal growing environment for plants.
Advantages of Portable Chiller Units
Flexibility
The most significant advantage of portable chiller units is their flexibility. They can be easily moved from one location to another, allowing users to adapt to changing cooling needs. Whether it’s a temporary project, a seasonal requirement, or an emergency situation, portable chillers can be quickly deployed where they are needed.
Cost – Effective
Compared to installing a permanent, large – scale chiller system, portable chiller units can be a more cost – effective solution, especially for short – term or intermittent cooling needs. They eliminate the need for extensive installation work, such as plumbing and electrical wiring, which can significantly reduce upfront costs. Additionally, their energy – efficient operation and variable cooling capacity can lead to lower operating costs over time.
Quick Installation
Portable chiller units are designed for quick and easy installation. Most units only require a power connection and, in the case of water – cooled models, a connection to a water source. This means they can be up and running in a short period, without the need for specialized installation teams or long – drawn – out setup processes.
Limitations of Portable Chiller Units
Limited Cooling Capacity
Portable chiller units generally have a lower cooling capacity compared to large, fixed – installation chillers. This makes them less suitable for applications that require extremely high cooling loads, such as large industrial plants or multi – story commercial buildings. While some models offer relatively high cooling capacities, they still may not be sufficient for very large – scale cooling requirements.
Noise Generation
Air – cooled portable chiller units, in particular, can generate noise due to the operation of the fans. This noise can be a nuisance in noise – sensitive environments, such as residential areas, libraries, or hospitals. Although manufacturers are constantly working on reducing noise levels, it remains a limitation for some applications.
Dependency on Power and Water (for water – cooled models)
Portable chiller units require a reliable power source to operate. In areas with unstable power supplies or during power outages, their functionality can be severely affected. Water – cooled portable chillers also depend on a consistent water source. Any disruptions in the water supply can lead to reduced performance or even shutdown of the unit.
Selection Criteria for Portable Chiller Units
Cooling Capacity
Calculation: Determining the appropriate cooling capacity is crucial when selecting a portable chiller unit. The cooling capacity is usually measured in British Thermal Units per hour (BTU/h) or tons of refrigeration (TR). To calculate the required cooling capacity, factors such as the size of the area to be cooled, the number of heat – generating devices, and the ambient temperature need to be considered. For example, in a small workshop with several pieces of machinery, the heat generated by the machines, along with the heat from the occupants and the environment, needs to be accounted for to ensure the chiller can maintain the desired temperature.
Future Needs: It’s also important to consider future cooling needs. If there is a possibility of adding more equipment or expanding the area to be cooled in the future, choosing a chiller with a slightly higher cooling capacity than the current requirements can save the cost and hassle of replacing the unit later.
Type of Cooling
Air – Cooled vs. Water – Cooled: Deciding between an air – cooled and a water – cooled portable chiller depends on various factors. Air – cooled chillers are more convenient and require less infrastructure, making them suitable for applications where water supply is limited or not available. Water – cooled chillers, on the other hand, offer higher efficiency and cooling capacity, making them a better choice for applications with higher cooling demands and a reliable water source.
Hybrid Options: Some portable chiller units offer hybrid cooling options, combining features of both air – cooled and water – cooled systems. These hybrid models can provide more flexibility and may be suitable for applications where the cooling requirements or available resources vary.
Energy Efficiency
Efficiency Ratings: Look for portable chiller units with high energy – efficiency ratings. Energy – efficient models consume less electricity, resulting in lower operating costs. Ratings such as Energy Star (in some regions) can be used as a guide to identify more energy – efficient units. Additionally, features like variable – speed compressors and intelligent control systems can enhance the energy efficiency of the chiller.
Long – Term Costs: Consider the long – term energy costs when selecting a chiller. A more energy – efficient unit may have a higher upfront cost but can save significant amounts of money on electricity bills over its lifespan. It’s important to balance the initial purchase price with the potential long – term savings in energy consumption.
Noise Level
Application Requirements: Depending on the application, the noise level of the portable chiller unit may be a critical factor. In noise – sensitive environments, such as offices or residential areas, a quiet – operating chiller is essential. Check the manufacturer’s specifications for the noise level of the unit, usually measured in decibels (dB). Some units are designed with noise – reduction features, such as sound – dampening enclosures or low – noise fans, which can be preferred for these applications.
Portability Features
Wheels and Handles: The quality and design of the wheels and handles can greatly affect the portability of the chiller unit. Look for units with durable wheels that can handle different surfaces and are easy to maneuver. Ergonomically designed handles make it easier to push or pull the unit, especially in tight spaces or over longer distances.
Size and Weight: The overall size and weight of the portable chiller unit also play a role in its portability. A smaller and lighter unit is generally easier to move around. However, it’s important to ensure that the unit still meets the required cooling capacity and performance criteria.
Maintenance of Portable Chiller Units
Regular Inspections
Component Check: Regularly inspect all the components of the portable chiller unit, including the compressor, condenser, evaporator, fans, and control systems. Look for signs of wear, damage, or leaks. Check the refrigerant lines for any signs of corrosion or leakage. Ensure that all electrical connections are secure and free from damage.
Filter Cleaning: Clean or replace the air filters (in air – cooled models) regularly. Clogged filters can reduce the efficiency of the chiller and lead to increased energy consumption. In water – cooled models, check and clean the water filters to prevent debris from entering the system and causing damage to the components.
Refrigerant Level Monitoring
Checking and Refilling: Monitor the refrigerant level in the chiller unit regularly. A low refrigerant level can indicate a leak and can significantly reduce the cooling performance of the unit. If a low refrigerant level is detected, it’s important to have the system inspected by a professional technician to identify and repair the leak before refilling the refrigerant.
Lubrication
Moving Parts: Lubricate the moving parts of the chiller unit, such as the compressor bearings and fan motors, according to the manufacturer’s recommendations. Proper lubrication reduces friction, wear, and noise, ensuring the smooth operation of the unit. Use the recommended lubricants and follow the correct lubrication procedures to avoid damage to the components.
Seasonal Maintenance
Pre – Season and Post – Season Checks: Before and after the peak cooling season, perform a more comprehensive maintenance check. This includes cleaning the entire unit, checking and tightening all connections, and testing the control systems. In the off – season, store the portable chiller unit in a dry, protected area to prevent damage from moisture, dust, and other environmental factors.
Future Trends in Portable Chiller Units
Smart and Connected Technologies
The future of portable chiller units is likely to involve the integration of smart and connected technologies. These units may be equipped with sensors and internet – of – things (IoT) capabilities, allowing users to monitor and control the chiller remotely. Smart features could include automatic adjustment of the cooling capacity based on real – time temperature and usage data, predictive maintenance alerts, and energy – consumption analytics. This would enhance the convenience, efficiency, and reliability of portable chiller units.
Improved Energy Efficiency
With the increasing focus on energy conservation and environmental sustainability, manufacturers are expected to develop more energy – efficient portable chiller units. This may involve the use of advanced compressor technologies, better heat – transfer materials, and more intelligent control systems. Newer models may also be designed to be more compatible with renewable energy sources, such as solar power, further reducing their carbon footprint.
Related recommendations
vapour compression chiller
217Understanding Vapor Compression Chillers Vapor compression chillers are the most common type of chiller system used in commercial and industrial applications. They operate by compressing a refr...
View details50 ton chiller cost
194Understanding the Cost of a 50-Ton ChillerThe cost of a 50-ton chiller is influenced by several factors, including the type of chiller, its efficiency, features, installation requirements, and ope...
View detailsHow to handle faults in industrial chiller systems?
796How to handle faults in industrial chiller systems? 1. Power on without power. ① If the power cord has poor contact, check the power interface and whether the power cord plug is properl...
View detailschiller heating and cooling system
89Chiller Heating and Cooling System: A Comprehensive GuideIntroductionA chiller heating and cooling system is a versatile HVAC solution that provides both cooling and heating capabilities in a sing...
View details
HelloPlease log in