portable industrial chiller
Portable Industrial Chiller: Detailed Explanation
- Introduction to Portable Industrial Chillers
Portable industrial chillers are complete refrigeration systems packaged in mobile enclosures designed to provide process cooling in industrial environments. Unlike centralized cooling systems, these units offer:
Immediate cooling capacity without installation delays
Flexibility to support multiple machines sequentially
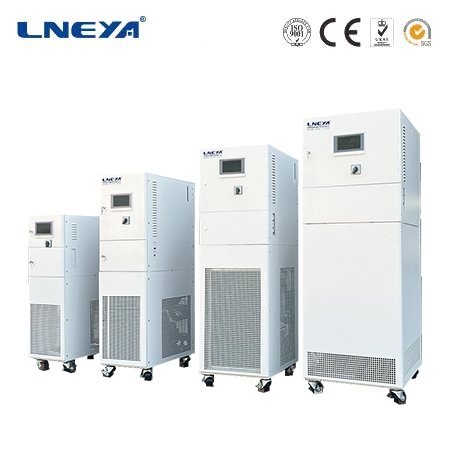
Easy relocation as production needs change
Simplified maintenance with accessible components
- System Components
A. Core Components
Compressor
Reciprocating, scroll or rotary types
Hermetically sealed or semi-hermetic designs
Single or multiple for capacity control
Heat Exchangers
Evaporator: Plate or shell-and-tube designs
Condenser: Air-cooled (most common) or water-cooled
Refrigeration Circuit
Expansion device (TXV or capillary tube)
Filter-drier
Sight glass/moisture indicator
Pump System
Centrifugal or positive displacement
Flow rates from 5-100 LPM typically
Pressure capabilities up to 10 bar
B. Supporting Components
Mobile chassis with casters or wheels
Control panel with temperature display
Safety devices (flow switches, pressure controls)
Insulated fluid reservoir (on some models)
- Types of Portable Industrial Chillers
A. By Cooling Method
Air-Cooled Portable Chillers
Most common type
Uses ambient air to reject heat
Requires adequate ventilation space
Water-Cooled Portable Chillers
Higher efficiency
Requires connection to cooling water supply
Used where air cooling is impractical
B. By Temperature Range
Standard Temperature (5°C to 30°C)
General purpose cooling
Most common for equipment cooling
Low Temperature (-10°C to 5°C)
Specialized applications
May use secondary refrigerants
Ultra-Low Temperature (-40°C to -10°C)
Cascade systems
Special compressor designs
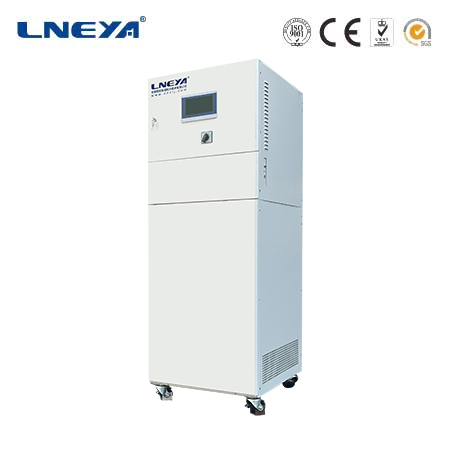
C. By Configuration
Benchtop Models
Small capacity (<1kW)
For laboratories and small equipment
Floor-standing Units
Medium capacity (1-20kW)
Most common industrial type
Skid-mounted Systems
Large capacity (20-60kW)
Heavy-duty industrial use
- How Portable Chillers Work
The operational cycle consists of four main processes:
Fluid Circulation
Process pump moves fluid through system
Fluid absorbs heat from application
Returns to chiller at elevated temperature
Heat Absorption
Warm fluid passes through evaporator
Refrigerant absorbs heat, cooling fluid
Chilled fluid returns to application
Heat Rejection
Refrigerant compressed to high pressure
Heat expelled via air or water condenser
Refrigerant condenses back to liquid
Temperature Regulation
Controller monitors process temperature
Adjusts compressor operation
Maintains setpoint within ±0.5°C typically
- Performance Characteristics
A. Cooling Capacity
Expressed in kW or BTU/hr
Ranges from 0.5kW to 60kW typically
Calculated based on:
Fluid flow rate
Temperature differential
Fluid specific heat
B. Temperature Control
Stability: ±0.1°C to ±1°C depending on model
Range: -40°C to +30°C
Proportional control for precise regulation
C. Flow Characteristics
Flow rates: 5-100 liters per minute
Pressure capabilities: 2-10 bar
Connection sizes: 1/4″ to 2″ typically
- Applications
A. Plastics Industry
Injection molding machines
Extruders and blow molders
3D printing equipment
B. Laser Systems
CO2 laser cutting
Fiber laser marking
Laser welding systems
C. Medical & Laboratory
MRI machines
Analytical equipment
Laboratory reactors
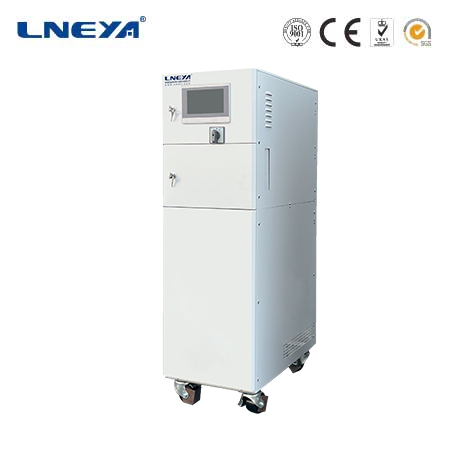
D. Food Processing
Batch cooling
Chocolate tempering
Beverage cooling
E. Other Industrial
Vacuum pumps
Hydraulic systems
Test chambers
- Advantages of Portable Chillers
Mobility Benefits
Move between multiple machines
Temporary cooling solutions
Rental options available
Installation Advantages
No permanent piping required
Quick setup (plug-and-play)
Minimal space requirements
Economic Benefits
Lower capital cost than built-in systems
Pay-as-you-need capacity
Energy efficient operation
Operational Flexibility
Adjust capacity by adding units
Seasonal usage patterns
Emergency backup capability
- Selection Criteria
Key factors when selecting a portable chiller:
Cooling Requirements
Temperature range needed
Heat load calculation
Flow rate requirements
Environmental Conditions
Ambient temperature range
Available utilities (power, water)
Space constraints
Fluid Considerations
Water or glycol mixture
Corrosion potential
Viscosity characteristics
Operational Needs
Duty cycle requirements
Mobility frequency
Control sophistication
Regulatory Compliance
Electrical safety standards
Refrigerant regulations
Noise restrictions
- Installation Considerations
A. Site Preparation
Level, stable surface
Adequate clearance for airflow
Access to power supply
B. Fluid Connections
Proper hose/tubing selection
Secure fittings to prevent leaks
Insulation for low-temp applications
C. Electrical Requirements
Voltage and phase compatibility
Circuit protection
Proper grounding
D. Ambient Conditions
Maximum/minimum operating temps
Protection from weather if outdoors
Clean environment free of debris
- Maintenance Requirements
A. Routine Maintenance
Daily:
Check fluid levels
Verify proper operation
Monitor temperatures
Weekly:
Clean air filters
Check for leaks
Inspect electrical connections
B. Periodic Service
Monthly:
Clean condenser coils
Verify refrigerant charge
Test safety controls
Annually:
Replace filter-driers
Check pump wear
Full system inspection
C. Fluid Management
Regular replacement schedule
Inhibitors for corrosion protection
Filtration to prevent clogging
- Troubleshooting Common Issues
A. Temperature Problems
Insufficient cooling:
Low refrigerant
Dirty condenser
Pump failure
Temperature fluctuations:
Air in system
Controller issues
Flow rate changes
B. Flow Issues
Low flow:
Clogged filter
Pump problems
Hose restrictions
No flow:
Empty reservoir
Pump failure
Closed valves
C. Electrical Faults
Power issues:
Tripped breaker
Loose connections
Voltage fluctuations
Control problems:
Sensor failures
Board issues
Programming errors
- Safety Considerations
A. Electrical Safety
Proper grounding
Circuit protection
Qualified personnel for repairs
B. Refrigerant Handling
EPA certification requirements
Proper recovery procedures
Leak prevention
C. Fluid Safety
High temperature warnings
Glycol toxicity
Pressure relief provisions
D. Physical Hazards
Moving parts guards
Hot surface warnings
Proper lifting techniques
- Energy Efficiency Measures
Variable Speed Technology
Compressor speed modulation
ECM pump motors
Intelligent fan control
Heat Recovery Options
Waste heat utilization
Combined heating/cooling
Process integration
System Optimization
Proper sizing
Setpoint adjustment
Insulation improvements
Maintenance Practices
Clean heat exchangers
Proper refrigerant charge
System leak checks
- Technological Advances
A. Improved Components
Inverter-driven compressors
Microchannel heat exchangers
Brushless DC pumps
B. Smart Features
IoT connectivity
Remote monitoring
Predictive maintenance
C. Alternative Refrigerants
Low-GWP options
Natural refrigerants
Zeotropic blends
D. Hybrid Systems
Solar-assisted operation
Thermal storage integration
Combined heating/cooling
- Future Trends
A. Sustainability Focus
Energy recovery systems
Eco-friendly refrigerants
Circular economy designs
B. Digital Transformation
AI-assisted optimization
Digital twin technology
Blockchain maintenance records
C. Advanced Materials
Graphene-enhanced components
Self-cleaning surfaces
Corrosion-resistant alloys
D. System Integration
Smart factory compatibility
Automated process control
Energy management systems
Conclusion
Portable industrial chillers provide versatile, efficient cooling solutions for a wide range of industrial applications. Their mobility and self-contained design offer significant advantages over fixed cooling systems, particularly in dynamic production environments. Proper selection based on application requirements and adherence to maintenance schedules are essential for reliable operation. As technology advances, portable chillers are becoming more energy efficient, intelligent and environmentally friendly while maintaining their core benefits of flexibility and ease of use. These units will continue to play a vital role in industrial cooling, especially where temporary, mobile or scalable cooling capacity is required.
Related recommendations
scroll water chiller
278Scroll Water Chiller: Technology and Efficiency Scroll water chillers are a type of HVAC equipment that utilize scroll compressor technology to provide efficient and reliable cooling. These chi...
View detailstemperature process control system
201Temperature Process Control Systems: Ensuring Precision in Industrial Processes Temperature process control systems are essential in maintaining the precise temperature conditions required for ...
View detailscool heating
228Cool Heating: Sustainable and Energy-Efficient Heating Solutions Cool heating is an innovative approach to heating that focuses on energy efficiency and minimal environmental impact. Unlike tra...
View detailschiller operation
197The Operation of Chiller Systems Chiller systems are essential in various industries for cooling applications, and their operation is based on well-established refrigeration principles. The pro...
View details
HelloPlease log in