process heaters
Process heaters are industrial equipment designed to raise the temperature of a process fluid, gas, or solid. They play a crucial role in numerous industries by providing the necessary heat for chemical reactions, material processing, and maintaining specific temperature conditions. These heaters are engineered to meet the unique requirements of different industrial processes, whether it’s heating a liquid to a precise temperature for a manufacturing process or drying a solid material.
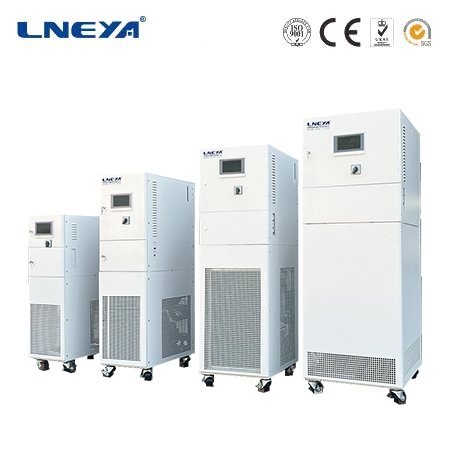
Working Principles of Process Heaters
Heat Generation
Process heaters generate heat through various methods. In electric process heaters, electrical resistance elements are used. When an electric current passes through these elements, the resistance causes the elements to heat up. This heat is then transferred to the process fluid or material in contact with the heating elements. For example, in a small – scale laboratory setting, an electric heating mantle is used to heat a glass vessel containing a chemical solution. The heating mantle consists of a coil of resistance wire, and when powered, it heats the vessel and the solution inside.
In fuel – fired process heaters, combustion of a fuel source, such as natural gas, oil, or coal, is used to generate heat. The fuel is burned in a combustion chamber, and the hot gases produced transfer heat to the process fluid or material through a heat – transfer surface. This could be in the form of a heat exchanger, where the hot combustion gases pass through tubes, and the process fluid flows around the tubes, absorbing the heat.
Heat Transfer
There are three main modes of heat transfer in process heaters: conduction, convection, and radiation. Conduction occurs when heat is transferred through direct contact between two substances. In a process heater, for instance, heat is conducted from the heating element (such as a metal tube in a steam – heated process heater) to the process fluid flowing inside the tube.
Convection involves the transfer of heat through the movement of a fluid (liquid or gas). In a forced – convection process heater, a fan or a pump is used to circulate the process fluid. As the fluid flows over the heated surface, it absorbs heat and carries it away. This is common in air – cooled process heaters, where a fan blows air over a heated coil, and the heated air is then directed to the area where the heat is needed.
Radiation is the transfer of heat through electromagnetic waves. In high – temperature process heaters, radiation plays a significant role. For example, in a direct – fired furnace used in the steel – making industry, the intense heat from the combustion of fuel radiates towards the steel being processed, heating it up to the required temperature for shaping and treatment.
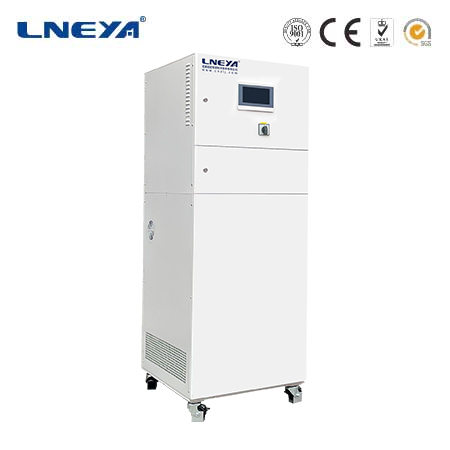
Types of Process Heaters
Direct – Fired Process Heaters
Construction and Operation
Direct – fired process heaters have a combustion chamber where the fuel is burned. The hot combustion gases directly contact the process fluid or material being heated. For example, in a petrochemical refinery, a direct – fired heater may be used to heat crude oil. The combustion gases from the burning of natural gas pass through a series of tubes, and the crude oil flows through these tubes. The direct contact between the hot gases and the oil allows for rapid heat transfer.
Advantages and Disadvantages
Advantages: They offer high – temperature capabilities and can achieve rapid heating. The direct – contact heat transfer results in high heat – transfer efficiency. In applications where a quick temperature rise is required, such as in some chemical reactions, direct – fired heaters are very effective.
Disadvantages: There is a risk of contamination of the process fluid by the combustion products if not properly designed. Also, they may require more complex safety measures due to the presence of open flames and high – temperature combustion gases.
Indirect – Fired Process Heaters
Construction and Operation
Indirect – fired process heaters use a heat – transfer medium, such as steam, hot oil, or a thermal fluid, to transfer heat from the heat source to the process fluid or material. For example, in a food – processing plant, an indirect – fired hot – oil heater may be used to heat a cooking vessel. The hot oil is heated in a separate heater unit by burning fuel. The heated oil is then pumped through a heat exchanger, where it transfers heat to the cooking vessel, heating the food product inside without direct contact with the combustion gases.
Advantages and Disadvantages
Advantages: They are safer as there is no direct contact between the combustion products and the process fluid, reducing the risk of contamination. They also offer more precise temperature control as the heat – transfer medium can be regulated more accurately.
Disadvantages: Indirect – fired heaters may be more complex in design and require additional components such as heat – transfer fluid pumps and heat exchangers. They can also be less energy – efficient compared to direct – fired heaters in some cases due to the additional heat – transfer steps.
Electric Process Heaters
Construction and Operation
Electric process heaters use electrical energy to generate heat. They can have different configurations, such as resistance heaters, induction heaters, and infrared heaters. Resistance heaters, as mentioned earlier, use resistance elements. Induction heaters use electromagnetic induction to heat conductive materials. An alternating current is passed through a coil, creating a magnetic field. When a conductive material is placed within this field, electric currents are induced in the material, causing it to heat up. Infrared heaters emit infrared radiation, which is absorbed by the process material, converting the radiation into heat.
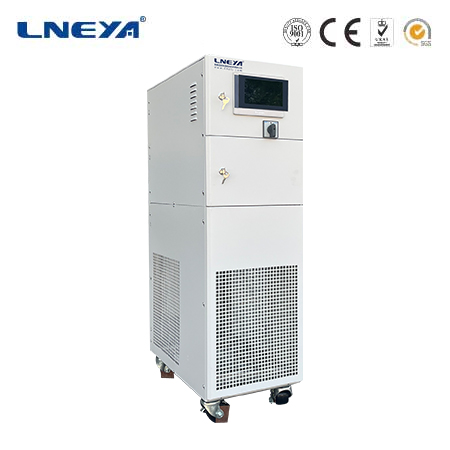
Advantages and Disadvantages
Advantages: Electric heaters are clean as they do not produce combustion by – products. They offer precise temperature control and can be quickly turned on and off. They are also suitable for applications where a compact and easily – installed heating solution is required.
Disadvantages: They can be more expensive to operate in terms of energy costs compared to fuel – fired heaters, especially in regions with high electricity prices. The heating capacity of electric heaters may also be limited in some cases, making them less suitable for large – scale, high – temperature applications.
Applications of Process Heaters
Petrochemical Industry
In the petrochemical industry, process heaters are used in various processes. For example, in the distillation of crude oil, process heaters are used to heat the crude oil to high temperatures. The different components of crude oil have different boiling points, and by heating the crude oil, the lighter components vaporize first and can be separated from the heavier ones. Process heaters are also used in chemical reactors to provide the heat required for chemical reactions. In the production of plastics from petrochemical feedstocks, heaters are used to heat the reactants to the appropriate temperature for polymerization reactions to occur.
Food and Beverage Industry
In the food and beverage industry, process heaters are used for cooking, baking, and drying processes. In a bakery, process heaters are used to heat ovens to the correct temperature for baking bread, cakes, and pastries. In a beverage production plant, heaters are used to heat water for cleaning equipment, as well as for heating and pasteurizing beverages. For example, in the production of fruit juices, the juice may be heated to a specific temperature for a certain period to kill harmful microorganisms while maintaining the flavor and nutritional value.
Pharmaceutical Industry
In the pharmaceutical industry, process heaters are used for processes such as drying of pharmaceutical powders, sterilization of equipment, and heating of reaction mixtures. In the production of tablets, the pharmaceutical powders need to be dried to the right moisture content. Process heaters are used to provide the heat for this drying process. Heaters are also used in autoclaves for sterilizing equipment and packaging materials. In pharmaceutical research and development, process heaters are used to heat reaction vessels where new drugs are synthesized, ensuring that the chemical reactions occur at the optimal temperature.
Textile Industry
In the textile industry, process heaters are used for processes like drying of wet fabrics, heat – setting of fibers, and dyeing. After fabrics are washed or treated with chemicals, they need to be dried. Process heaters provide the heat for this drying process. Heat – setting is a process where the fabric is heated to a specific temperature to improve its dimensional stability. Process heaters are used to achieve the required temperature for heat – setting. In the dyeing process, heaters are used to heat the dye bath to the appropriate temperature to ensure proper dye penetration into the fabric.
Maintenance of Process Heaters
Regular Inspections
For all types of process heaters, regular inspections are essential. In fuel – fired heaters, the combustion chamber should be inspected for signs of corrosion, wear, or damage. The burners should be checked for proper operation, and the fuel lines should be inspected for leaks. In electric heaters, the heating elements should be inspected for any signs of breakage or overheating. The electrical connections should also be checked to ensure they are secure and free from corrosion.
Cleaning
Cleaning is an important maintenance task. In process heaters with heat – transfer surfaces, such as heat exchangers, these surfaces should be cleaned regularly to remove any deposits or scale. Deposits on the heat – transfer surfaces can reduce the efficiency of the heater by impeding heat transfer. In direct – fired heaters, the flue gas passages should be cleaned to prevent the build – up of soot and other combustion by – products, which can also affect the performance of the heater.
Calibration and Testing
The temperature control systems of process heaters should be calibrated regularly to ensure accurate temperature settings. In fuel – fired heaters, the fuel – air ratio control system should be tested and adjusted as needed to ensure efficient combustion. In electric heaters, the electrical controls and safety devices should be tested to ensure they are functioning properly. This helps in preventing overheating and other safety hazards.
Conclusion
Process heaters are diverse in their types and applications, playing a vital role in numerous industries. Understanding their working principles, types, applications, and maintenance requirements is crucial for industries to ensure efficient and safe operation. Whether it’s a large – scale petrochemical plant or a small – scale food – processing unit, the proper selection and maintenance of process heaters can significantly impact the quality of products and the overall productivity of the operation.
Related recommendations
adiabatic chillers
16Adiabatic Chillers: A Deep Dive Introduction In the pursuit of more energy - efficient and sustainable cooling solutions, adiabatic chillers have emerged as a promising technology. They of...
View detailselectric heating cooling system
184Electric Heating and Cooling Systems: Efficient and Environmentally Friendly Solutions Electric heating and cooling systems are gaining popularity due to their ability to provide precise temper...
View detailsvapour compression chiller
202Understanding Vapor Compression Chillers Vapor compression chillers are the most common type of chiller system used in commercial and industrial applications. They operate by compressing a refr...
View detailschillers uk
18Chillers in the UK: A Comprehensive GuideChillers play a vital role in the United Kingdom across a wide range of industries and applications. They are used to remove heat from a process or space,...
View details
HelloPlease log in