process water heater
Understanding Process Water Heaters
Process water heaters are essential in many industrial settings, where they provide heated water for a variety of applications. These applications can range from cleaning and sterilization to maintaining process temperatures in manufacturing. The choice of water heater can significantly impact the efficiency and cost-effectiveness of these processes. In this article, we will explore the different types of process water heaters, their operating principles, and factors to consider when selecting and maintaining these systems.
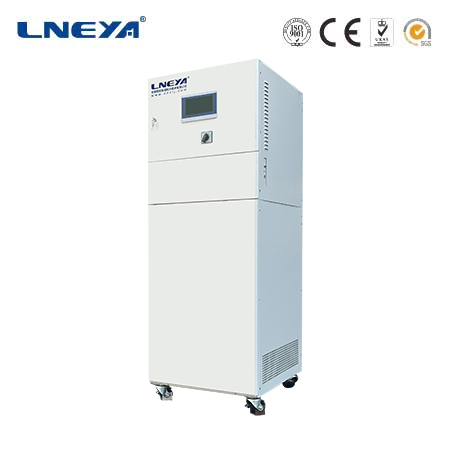
Types of Process Water Heaters
There are several types of process water heaters, each with its own advantages and disadvantages:
Electric Water Heaters: These heaters use electric resistance elements to heat water. They are simple to install and operate, and they do not produce any emissions. However, they can be less energy-efficient than gas heaters, especially in areas with high electricity costs.
Gas Water Heaters: Gas heaters use either natural gas or propane to heat water. They are generally more energy-efficient than electric heaters and can provide a higher flow rate. However, they require a gas supply and proper ventilation.
Indirect Water Heaters: These heaters use a heat exchanger to transfer heat from a primary heat source, such as a boiler, to the water. Indirect heaters can be very energy-efficient, as they recover heat that would otherwise be wasted. They are also suitable for applications where high purity water is required.
Working Principles
The basic principle behind all process water heaters is the transfer of heat to the water. In electric heaters, this is achieved through resistance heating, where an electric current passes through a resistance element, generating heat. Gas heaters use a burner to heat a heat exchanger, which then transfers heat to the water. Indirect heaters, on the other hand, use the heat from a primary heat source to warm the water through a heat exchanger.
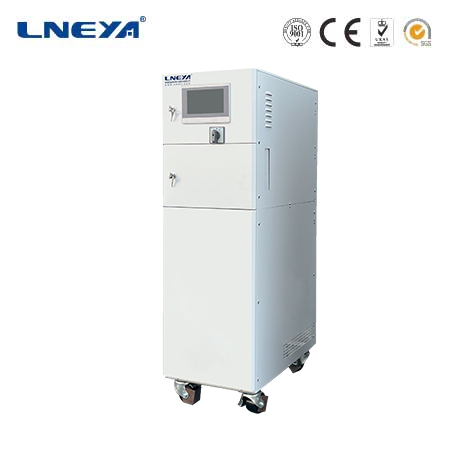
Efficiency Considerations
When selecting a process water heater, efficiency is a key factor. The recovery rate of a heater refers to the amount of heat it can add to the water per unit of time. Standby loss is another important consideration, which is the heat lost when the heater is not in use. Insulation and proper sizing can help minimize standby loss.
Energy efficiency can also be improved by using demand-controlled systems, which only heat water as needed, and by maintaining the heater properly to ensure optimal performance.
Safety Features
Safety is paramount in industrial settings, and process water heaters are equipped with several safety features to prevent accidents. These can include pressure relief valves to prevent over-pressurization, temperature and pressure gauges to monitor the system, and safety shut-offs that turn off the heater if it detects abnormal conditions.
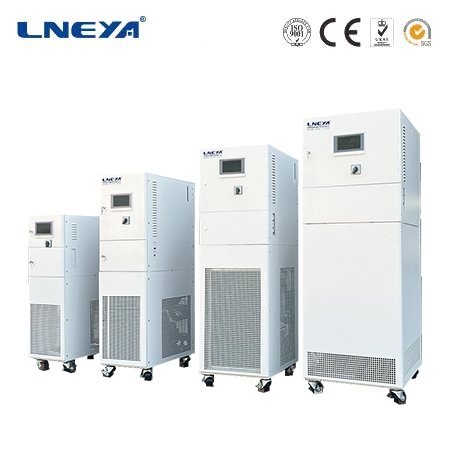
Maintenance Tips
Regular maintenance is crucial for the longevity and efficiency of process water heaters. This can include:
Inspecting and cleaning the heat exchanger to ensure efficient heat transfer.
Checking the burner in gas heaters for any signs of wear or damage.
Replacing the anode rod in electric heaters to prevent corrosion.
Monitoring the water quality to prevent scale buildup, which can reduce efficiency and cause damage.
Conclusion
Process water heaters are a vital part of many industrial processes, and selecting the right type for your needs is essential. By understanding the different types of heaters, their working principles, and the factors that affect their efficiency, you can make an informed decision. Additionally, ensuring that your heater is equipped with the necessary safety features and that it is maintained regularly will help to keep your processes running smoothly and efficiently.
Related recommendations
low pressure chiller
238Understanding Low Pressure Chillers Low pressure chillers represent a class of refrigeration systems that operate at pressures below atmospheric pressure. This design allows for the use of refr...
View detailschiller capacity unit
183Chiller Capacity Units: Understanding the Basics Chiller capacity is a critical parameter in the specification and selection of chillers for HVAC systems. It refers to the cooling capacity of a...
View detailswater bath maintenance
289Water Bath Maintenance: Ensuring Optimal Performance and Safety Water baths are indispensable pieces of equipment in laboratories, playing a vital role in maintaining precise temperatures for a...
View detailsclosed cycle cooling water system
173Water-Cooled Chiller: Efficient Heat Rejection for HVAC Systems A water-cooled chiller is a type of HVAC equipment that utilizes water as a medium for heat rejection, offering a more efficient ...
View details
HelloPlease log in