propylene glycol for chiller
In chiller systems, maintaining an efficient and reliable cooling process is of utmost importance. Propylene glycol has emerged as a popular choice for use in chiller coolants. It is a clear, colorless, viscous liquid that is miscible with water. When added to water, it forms a mixture that can significantly enhance the performance of chiller systems in various applications.
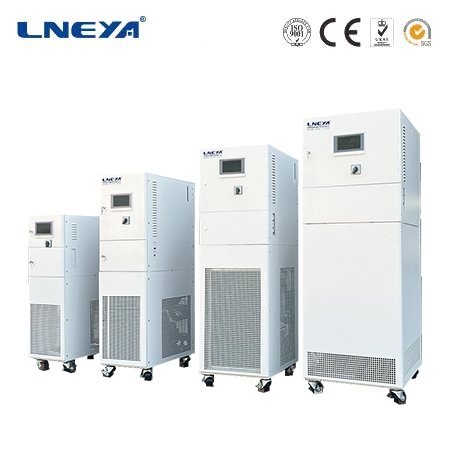
Properties of Propylene Glycol That Benefit Chillers
Antifreeze Properties
Freezing Point Depression: One of the primary reasons propylene glycol is used in chiller coolants is its ability to lower the freezing point of water. Pure water freezes at 0°C (32°F). By adding propylene glycol to water, the freezing point of the mixture can be reduced substantially. For example, a 30% propylene glycol – water solution has a freezing point of approximately – 15°C (5°F), and a 50% solution can have a freezing point as low as – 37°C (- 35°F). This property is crucial in chiller applications where the coolant may be exposed to low temperatures, such as in outdoor – installed chillers in cold climates or in industrial processes that require cooling below the freezing point of water. In these cases, the antifreeze property of propylene glycol ensures that the coolant remains in a liquid state, allowing for continuous heat transfer and preventing damage to the chiller system due to frozen coolant, which could cause pipes to burst and components to malfunction.
Protection Against Ice Formation: In addition to depressing the freezing point, propylene glycol also affects the formation of ice crystals. When the temperature of the coolant approaches the freezing point, instead of forming large, damaging ice crystals as pure water would, the propylene glycol – water mixture forms smaller, less – harmful ice structures. This helps to maintain the flow of the coolant within the chiller system, even in sub – freezing conditions, minimizing the risk of blockages and ensuring the chiller can continue to operate effectively.
Heat – Transfer Characteristics
Thermal Conductivity: Propylene glycol has a relatively good thermal conductivity, especially when mixed with water. Although its thermal conductivity is lower than that of pure water, the combination of propylene glycol and water in appropriate ratios can still provide efficient heat – transfer capabilities. In a chiller system, the coolant needs to absorb heat from the process or space being cooled and then release it to the environment or a secondary cooling medium. The heat – transfer properties of the propylene glycol – water mixture enable it to carry heat effectively from the evaporator (where it absorbs heat) to the condenser (where it releases heat). This is important for maintaining the desired temperature in the cooled area and for the overall energy efficiency of the chiller. For example, in a food – processing plant where precise temperature control is required, the heat – transfer characteristics of the propylene glycol – based coolant ensure that the products are cooled evenly and at the correct rate.
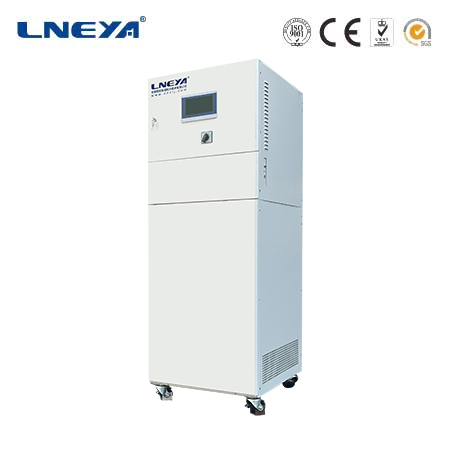
Specific Heat Capacity: Propylene glycol also has a specific heat capacity that, when combined with water, contributes to the coolant’s ability to store and transfer heat. The specific heat capacity of the propylene glycol – water mixture is such that it can absorb a significant amount of heat energy without a large increase in its own temperature. This property allows the coolant to carry more heat per unit mass, enhancing the cooling capacity of the chiller system. In industrial applications where large amounts of heat need to be removed from processes, such as in metalworking or chemical manufacturing, the high heat – storage capacity of the propylene glycol – water coolant helps to ensure efficient cooling and stable process operation.
Comparison with Other Coolant Additives, Especially Ethylene Glycol
Toxicity
Lower Toxicity of Propylene Glycol: One of the significant advantages of propylene glycol over ethylene glycol is its lower toxicity. Ethylene glycol is highly toxic and can be fatal if ingested. In contrast, propylene glycol is generally recognized as safe (GRAS) by the U.S. Food and Drug Administration (FDA) for use in food, pharmaceutical, and cosmetic applications. This makes propylene glycol a much safer choice for chiller applications where there may be a risk of coolant leakage and potential exposure to humans or the environment. For example, in a commercial building’s chiller system located in an area where there is a possibility of coolant seeping into the building’s water supply or being accessed by maintenance personnel, the use of propylene glycol reduces the health risks associated with accidental ingestion or exposure. In addition, in outdoor – installed chillers, propylene glycol is less harmful to plants and wildlife in case of a spill, making it a more environmentally friendly option.
Environmental Impact: Due to its lower toxicity, propylene glycol has a reduced environmental impact compared to ethylene glycol. When ethylene glycol – based coolants are released into the environment, they can contaminate soil and water sources, causing harm to aquatic life and other organisms. Propylene glycol, on the other hand, is more biodegradable and breaks down more easily in the environment. This makes it a preferred choice for applications where environmental concerns are a priority, such as in sensitive ecological areas or in industries that are subject to strict environmental regulations.
Performance in Chiller Systems
Similar Antifreeze and Heat – Transfer Performance: In terms of antifreeze and heat – transfer performance, propylene glycol and ethylene glycol are quite similar when used in chiller coolants. Both can effectively lower the freezing point of water and contribute to heat transfer within the chiller system. However, the optimal concentration ratios for achieving the best performance may vary between the two. For example, to achieve a certain freezing – point depression, a slightly higher concentration of propylene glycol may be required compared to ethylene glycol. But overall, in most chiller applications, the performance differences are not significant enough to be a determining factor in choosing between the two, except in cases where toxicity and environmental factors are not a concern, and cost or other specific performance requirements come into play.
Corrosion Inhibition: Both propylene glycol and ethylene glycol can cause corrosion in chiller systems if not properly formulated. However, with the addition of appropriate corrosion inhibitors, both can be made suitable for use in chiller systems. In some cases, the corrosion – inhibition requirements may be different for propylene glycol – based and ethylene – glycol – based coolants. For example, the type and amount of corrosion inhibitors needed to protect copper, steel, and aluminum components in a chiller may vary depending on whether propylene glycol or ethylene glycol is used as the base coolant. It is important to ensure that the coolant formulation, including the type of glycol and the corrosion inhibitors, is compatible with the materials used in the chiller system to prevent corrosion and extend the lifespan of the equipment.
Determining the Right Concentration of Propylene Glycol in Chiller Coolants
Freezing – Point Requirements
Calculating Based on Operating Temperature: The concentration of propylene glycol in the chiller coolant is primarily determined by the lowest operating temperature the chiller is expected to encounter. As mentioned earlier, different concentrations of propylene glycol – water mixtures have different freezing points. To determine the appropriate concentration, the operator needs to know the minimum temperature the coolant will be exposed to. For example, if a chiller is installed in an area where the outdoor temperature can drop as low as – 20°C (- 4°F) during winter, a propylene glycol – water mixture with a freezing point well below this temperature is required. Using a freezing – point – concentration chart for propylene glycol – water mixtures, the operator can determine that a concentration of around 40 – 45% propylene glycol may be necessary to achieve a freezing point of approximately – 25°C (- 13°F), providing a sufficient margin of safety to prevent freezing.
Accounting for System Variations: It is important to note that the actual operating temperature of the coolant within the chiller system may not be the same as the ambient temperature. Factors such as the heat load on the chiller, the efficiency of the heat – transfer process, and the insulation of the system can affect the coolant temperature. In some cases, the coolant may not reach the minimum ambient temperature due to the continuous heat – transfer process within the chiller. However, it is still crucial to consider the worst – case scenario when determining the propylene glycol concentration to ensure the system’s integrity in all operating conditions.
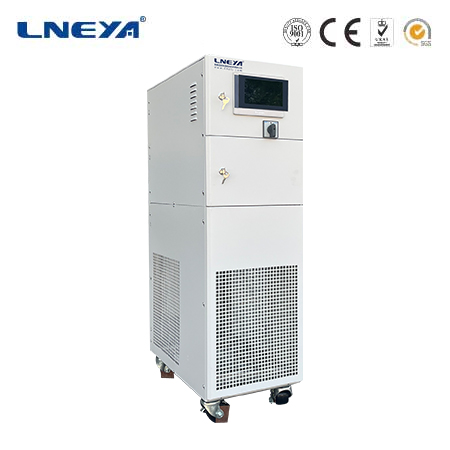
Heat – Transfer and System Performance
Balancing Antifreeze and Heat – Transfer: While the antifreeze property of propylene glycol is important, the concentration also affects the heat – transfer performance of the coolant. As the concentration of propylene glycol increases, the thermal conductivity of the mixture decreases slightly. Therefore, there is a need to balance the requirement for antifreeze protection with the need for efficient heat transfer. In applications where the operating temperature is not extremely low, a lower concentration of propylene glycol may be sufficient to meet the antifreeze needs while maintaining good heat – transfer performance. For example, in a chiller system used in a mild – climate region where the lowest expected temperature is around – 5°C (23°F), a 20 – 25% propylene glycol concentration may be adequate. This concentration provides enough antifreeze protection while minimizing the negative impact on heat transfer, ensuring optimal chiller performance.
System – Specific Considerations: The type of chiller system and the materials used in its construction can also influence the optimal propylene glycol concentration. For example, in a chiller with a high – efficiency heat exchanger that is very sensitive to changes in coolant properties, a more precise concentration of propylene glycol may be required to ensure proper heat transfer without causing any issues such as increased pressure drop or reduced heat – exchanger efficiency. Additionally, if the chiller system has components made of materials that are more prone to corrosion, the concentration of propylene glycol and the type of corrosion inhibitors may need to be carefully adjusted to provide adequate protection.
Potential Issues and Solutions When Using Propylene Glycol in Chillers
Corrosion
Causes of Corrosion: Although propylene glycol itself is not highly corrosive, in the presence of oxygen, water, and certain metals commonly used in chiller systems (such as copper, steel, and aluminum), corrosion can occur. The glycol – water mixture can act as an electrolyte, facilitating the electrochemical corrosion process. Additionally, if the pH of the coolant is not properly maintained, it can also accelerate corrosion. For example, if the coolant becomes acidic over time due to the breakdown of additives or the presence of contaminants, it can cause corrosion of metal components. Corrosion can lead to the formation of rust, pitting, and eventually, the failure of chiller components such as pipes, heat exchangers, and pumps.
Solutions for Corrosion Prevention: To prevent corrosion in chiller systems using propylene glycol – based coolants, several measures can be taken. First, the use of corrosion inhibitors is essential. These inhibitors work by forming a protective film on the surface of metal components, preventing the direct contact of the metal with the corrosive coolant. There are different types of corrosion inhibitors available, including those specifically designed for use with propylene glycol – water mixtures. Second, maintaining the proper pH of the coolant is crucial. Regular testing of the coolant’s pH and adjustment to a slightly alkaline range (usually around pH 8 – 10) can help prevent corrosion. Third, minimizing the exposure of the coolant to oxygen can also reduce corrosion. This can be achieved by using closed – loop chiller systems or by adding oxygen – scavenging additives to the coolant.
Contamination
Sources of Contamination: Contamination of the propylene glycol – based coolant can occur from various sources. In industrial applications, contaminants such as dirt, debris, and chemicals from the process being cooled can enter the coolant system. For example, in a metal – plating factory, small particles of metal or chemicals used in the plating process may leak into the chiller coolant. In addition, biological contaminants such as bacteria and algae can grow in the coolant, especially if the system is not properly maintained or if there is a source of nutrients present. Contamination can affect the performance of the coolant by reducing its heat – transfer efficiency, clogging filters and pipes, and accelerating corrosion.
Solutions for Contamination Control: To control contamination, regular filtration of the coolant is necessary. Installing high – quality filters in the coolant loop can remove solid particles and debris. In addition, the use of biocides can help prevent the growth of biological contaminants. Biocides are chemicals that are added to the coolant to kill or inhibit the growth of bacteria and algae. However, it is important to choose biocides that are compatible with the propylene glycol – water mixture and the materials used in the chiller system. Regular inspection and maintenance of the chiller system to detect and repair any leaks or sources of contamination are also crucial for keeping the coolant clean and ensuring optimal chiller performance.
Maintenance and Monitoring of Propylene Glycol – Based Chiller Coolants
Concentration Monitoring
Regular Testing: Regularly testing the concentration of propylene glycol in the coolant is essential to ensure that it remains within the optimal range. This can be done using a refractometer, which measures the refractive index of the coolant. The refractive index is directly related to the concentration of propylene glycol in the water – glycol mixture. By comparing the measured refractive index with a calibration chart, the operator can determine the propylene glycol concentration. Testing should be done at regular intervals, such as monthly or quarterly, depending on the operating conditions of the chiller system. If the concentration deviates from the desired range, additional propylene glycol or water can be added to adjust it.
Adjusting Concentration: If the propylene glycol concentration is too low, it may not provide sufficient antifreeze protection, and the coolant may be at risk of freezing. In this case, more propylene glycol needs to be added to the coolant. On the other hand, if the concentration is too high, it can reduce the heat – transfer efficiency of the coolant and increase the viscosity, which may cause problems with pump operation and flow. In such cases, water can be added to dilute the coolant to the appropriate concentration.
Quality Assessment
Visual Inspection: Visual inspection of the coolant is a simple but important part of maintenance. The coolant should be clear and free of any visible particles, discoloration, or signs of biological growth. If the coolant appears cloudy, has a strange color, or has a slimy texture, it may be contaminated or have undergone chemical changes. In such cases, further testing and analysis are required to determine the cause and take appropriate corrective actions.
Chemical Analysis: In addition to visual inspection, periodic chemical analysis of the coolant can provide more detailed information about its quality. Chemical analysis can detect the presence of contaminants, changes in pH, the effectiveness of corrosion inhibitors, and the breakdown products of propylene glycol. This information can help in making informed decisions about coolant maintenance, such as when to replace the coolant or adjust the additives. For example, if the chemical analysis shows that the concentration of corrosion inhibitors has decreased below the recommended level, additional inhibitors can be added to protect the chiller components from corrosion.
In conclusion, propylene glycol is a valuable coolant additive for chiller systems, offering excellent antifreeze and heat – transfer properties. By understanding its properties, comparing it with other options, determining the right concentration, addressing potential issues, and maintaining proper monitoring, chiller operators can ensure the efficient and reliable operation of their systems.
Related recommendations
self contained water chiller
162Self-contained water chillers are designed to provide efficient and reliable cooling in a variety of industrial and commercial applications. These chillers are particularly useful in scenarios whe...
View detailswater bath device
234Water Bath Device: A Cornerstone of Temperature Regulation in Laboratories Water bath devices are essential tools in laboratories and industrial settings, providing precise temperature control ...
View detailsconstant temperature water heater
152Introduction to Constant Temperature Water HeatersConstant temperature water heaters, also known as water baths, are vital in laboratories for maintaining a consistent temperature for processes su...
View detailsair and water cooling system
60Air and Water Cooling Systems: A Comprehensive OverviewI. IntroductionIn modern technological and industrial settings, maintaining appropriate temperatures is vital for the proper functioning an...
View details
HelloPlease log in