rooftop chiller units
Rooftop Chiller Units: Detailed Explanation
- Introduction to Rooftop Chiller Units
Rooftop chiller units are complete refrigeration systems mounted on building roofs that provide chilled liquid for cooling purposes. Unlike traditional chiller plants that require separate rooms, these packaged units contain all major components in a weatherproof enclosure.
Key characteristics include:
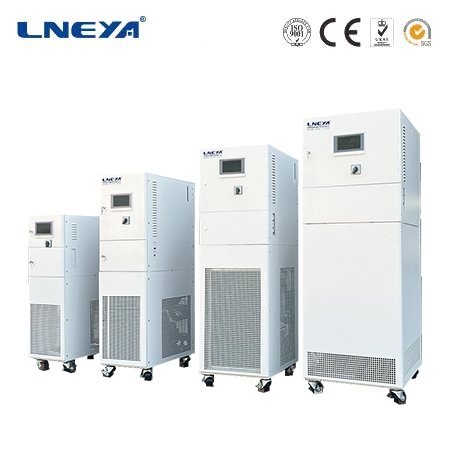
Designed for outdoor installation
Pre-assembled at factory
Simplified connection to building systems
Reduced installation time and cost
- System Components
A. Core Components
Compressor
Scroll, screw or centrifugal types
Single or multiple compressors for staging
Heat Exchangers
Evaporator for chilling water/glycol
Air-cooled or water-cooled condenser
Refrigerant Circuit
Expansion device
Filter-drier
Sight glass
Control System
Microprocessor controller
Safety cutouts
Communication interfaces
B. Auxiliary Components
Liquid pumps (on some models)
Vibration isolators
Weatherproof enclosure
Service access panels
- Types of Rooftop Chiller Units
A. By Cooling Method
Air-Cooled Rooftop Chillers
Use ambient air to condense refrigerant
Axial or centrifugal fans
Simpler installation (no cooling tower needed)
Water-Cooled Rooftop Chillers
Require cooling tower connection
Higher efficiency
More complex water system
B. By Configuration
Single-Package Units
Complete system in one enclosure
Fixed capacity
Economical for smaller applications
Modular Systems
Multiple interconnected units
Capacity staging
Redundancy options
Variable Refrigerant Flow (VRF) Options
Advanced inverter technology
Simultaneous heating/cooling
Zoned temperature control
- How Rooftop Chillers Work
The refrigeration cycle operates as follows:
Chilled Liquid Production
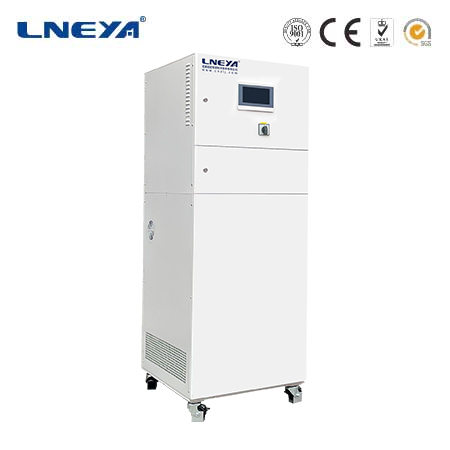
Warm return water (10-15°C) enters evaporator
Refrigerant absorbs heat, chilling water to 6-7°C
Chilled water pumps to air handlers
Heat Rejection
Compressed refrigerant (70-90°C) flows to condenser
Air or water removes heat from refrigerant
Condensed refrigerant returns to expansion device
Capacity Control
Digital controllers monitor load requirements
Compressor staging or variable speed operation
Pump speed modulation (if equipped)
- Performance Characteristics
A. Efficiency Metrics
COP: 2.5-4.5 for air-cooled models
EER: 10-16 (higher is better)
IPLV: Measures part-load efficiency
B. Capacity Range
Small units: 10-50 tons
Medium units: 50-150 tons
Large units: 150-400+ tons
C. Temperature Capabilities
Standard chilled water: 6-7°C supply
Low temperature: Down to -10°C (special models)
Precision control: ±0.5°C
- Applications
A. Commercial HVAC
Office buildings
Shopping centers
Hotels and convention centers
B. Institutional Facilities
Schools and universities
Hospitals and clinics
Government buildings
C. Light Industrial
Food processing
Pharmaceutical manufacturing
Plastic molding
- Advantages of Rooftop Installation
Space Optimization
Frees up valuable ground space
No dedicated mechanical room needed
Ideal for urban locations
Installation Benefits
Pre-assembled units reduce on-site work
Faster commissioning
Minimal building disruption
Maintenance Advantages
Easy outdoor access
Simplified service procedures
Better containment of refrigerant
Architectural Considerations
Preserves building aesthetics
Noise removed from occupied spaces
Flexible placement options
- Installation Requirements
A. Structural Considerations
Roof load capacity verification
Proper mounting frame/curb
Wind load calculations
B. Mechanical Requirements
Vibration isolation
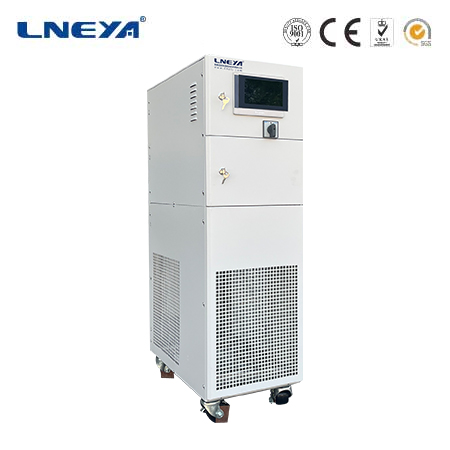
Piping connections
Electrical service
C. Environmental Factors
Local climate conditions
Sun exposure management
Drainage provisions
D. Safety Provisions
Fall protection
Service access pathways
Lightning protection
- Maintenance Procedures
A. Routine Maintenance
Monthly:
Filter inspection/cleaning
Visual component check
System parameter logging
Quarterly:
Coil cleaning
Refrigerant level check
Electrical connections
B. Annual Maintenance
Comprehensive system inspection
Lubrication of moving parts
Control calibration
Performance testing
C. Seasonal Considerations
Winterization for cold climates
Monsoon preparation
High-temperature operation checks
- Energy Efficiency Measures
Variable Speed Operation
Compressor speed modulation
ECM fan motors
Smart pump control
Heat Recovery Options
Desuperheater for water heating
Full heat recovery models
Waste heat utilization
Advanced Controls
Adaptive capacity control
Remote monitoring
Predictive maintenance
- Selection Criteria
Key factors when selecting rooftop chillers:
Cooling load requirements
Available roof space/access
Local climate conditions
Energy efficiency goals
Noise restrictions
Maintenance accessibility
Future expansion needs
Budget considerations
- Common Operational Issues
A. Refrigerant Management
Leak detection
Proper charging procedures
Retrofit considerations
B. Water Side Problems
Freeze protection
Flow rate issues
Corrosion prevention
C. Electrical Issues
Power quality problems
Component failures
Control system errors
D. Mechanical Concerns
Vibration and noise
Fan and motor failures
Compressor wear
- Technological Advances
A. Improved Components
Magnetic bearing compressors
Microchannel heat exchangers
Advanced motor designs
B. Smart Features
IoT connectivity
Cloud-based analytics
Automated diagnostics
C. Alternative Refrigerants
Low-GWP options
Natural refrigerant systems
Blends for specific applications
D. Hybrid Systems
Solar-assisted operation
Thermal storage integration
Combined heating/cooling
- Economic Considerations
A. Cost Factors
Initial equipment cost
Installation expenses
Operating costs
Maintenance budget
B. Lifecycle Analysis
Energy consumption projections
Replacement timelines
Total cost of ownership
C. Financial Incentives
Utility rebates
Tax credits
Green building certifications
- Future Trends
A. Sustainability Focus
Net-zero energy systems
Carbon-neutral operation
Circular economy principles
B. Digital Transformation
AI-powered optimization
Digital twin technology
Blockchain-enabled maintenance
C. Advanced Materials
Graphene-enhanced components
Self-healing materials
Nano-coatings
D. System Integration
Smart grid compatibility
Building automation convergence
District energy connections
Conclusion
Rooftop chiller units provide a practical and efficient cooling solution for commercial and light industrial applications where ground space is limited. Their packaged design offers installation advantages while maintaining the performance characteristics of traditional chiller systems. Proper selection, installation and maintenance are critical to achieving optimal performance and longevity. As technology advances, rooftop chillers are incorporating more energy-efficient designs, smart features and sustainable operation capabilities. These systems will continue to play a vital role in building cooling infrastructure, particularly in urban environments where space optimization is essential.
Related recommendations
water cooled cooling system
170Water-Cooled Cooling Systems: An In-Depth Analysis Water-cooled cooling systems play a critical role in maintaining optimal temperatures in various industrial and commercial applications. These...
View details25 ton chiller price
177Understanding the Cost of a 25-ton Chiller When considering the purchase of a 25-ton chiller, it's essential to understand that the price is not a one-size-fits-all figure. Chillers are complex...
View detailsindustrial chiller service
91What is Industrial Chiller Service? Industrial chiller service refers to the professional maintenance, repair, and optimization of cooling systems used in industrial applications. These service...
View detailschiller for water
240Water Chillers: Definition and Working Principles Definition of Water ChillersA water chiller is a refrigeration system that cools a fluid, typically water, which is then circulated to provide ...
View details
HelloPlease log in