thermal oil heaters
Introduction
In the industrial sector, the need for efficient and reliable heat – transfer solutions is paramount. Thermal oil heaters have emerged as a crucial technology, providing a means to transfer heat with high precision and stability. Unlike traditional steam or hot – water – based heating systems, thermal oil heaters use thermal oil as the heat – transfer medium. This medium offers several advantages, such as a high heat – carrying capacity, the ability to operate at high temperatures without boiling, and low vapor pressure, making it suitable for a wide range of industrial applications. This article delves into the various aspects of thermal oil heaters, from their fundamental principles to practical applications and future developments.
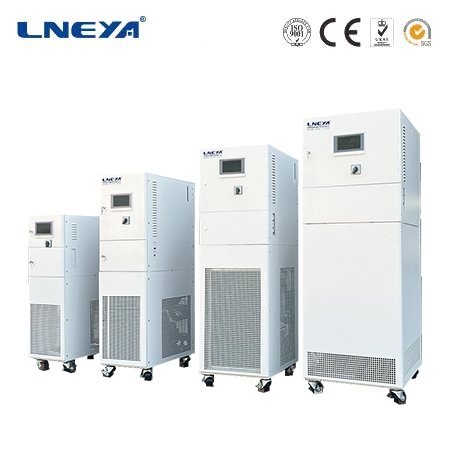
Working Principles
Heat Transfer Process
The operation of thermal oil heaters is based on the principle of forced – circulation heat transfer. A pump circulates the thermal oil through the heater, where it absorbs heat from the heating source. The heating source can be an electric element, a combustion chamber (in the case of fuel – fired heaters), or a waste – heat recovery system. Once heated, the thermal oil is then transported to the point of use, such as a heat exchanger, a reactor, or a processing equipment. In the heat exchanger, the thermal oil transfers its heat to the target medium (such as air, water, or a process fluid) through conduction and convection, without directly mixing with it. After releasing the heat, the cooled thermal oil returns to the heater to be reheated, creating a continuous loop.
Temperature Control
Temperature control is a critical aspect of thermal oil heater operation. Most thermal oil heaters are equipped with a control system that monitors the temperature of the thermal oil at various points in the system, such as the inlet and outlet of the heater and the point of use. Thermocouples or other temperature sensors are used to measure the temperature and send signals to the control system. Based on the set temperature, the control system adjusts the heat input to the heater. For example, in an electric thermal oil heater, the control system may regulate the electrical power supplied to the heating elements. In a fuel – fired heater, it can adjust the fuel flow rate and combustion air supply to maintain the desired temperature of the thermal oil. This precise temperature control ensures that the industrial processes that rely on the heated oil operate at optimal conditions.
Key Components
Heating Elements
Electric Heating Elements: In electric thermal oil heaters, heating elements are the primary source of heat. These elements are usually made of materials with high electrical resistance, such as nichrome or Incoloy. Nichrome is commonly used due to its excellent resistance to oxidation and high – temperature stability. The heating elements are designed in various forms, such as tubular, ribbon – shaped, or coiled, and are immersed in the thermal oil within the heater. As electricity passes through the elements, they generate heat, which is then transferred to the thermal oil.
Combustion Chambers (for fuel – fired heaters): Fuel – fired thermal oil heaters use combustion chambers where fuel (such as natural gas, diesel, or biomass) is burned. The combustion process releases a large amount of heat, which is transferred to the thermal oil through a heat – transfer surface. The design of the combustion chamber is crucial for efficient combustion and heat transfer. It needs to ensure proper mixing of the fuel and air, complete combustion, and effective heat transfer to the thermal oil. Combustion chambers are often equipped with burners, which control the fuel – air mixture and the combustion process.
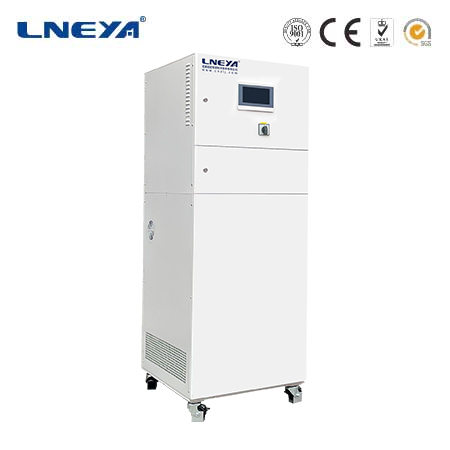
Pumps
Pumps play a vital role in the operation of thermal oil heaters by ensuring the continuous circulation of the thermal oil. They are typically centrifugal pumps, which are capable of handling high – viscosity fluids like thermal oil. The pump is sized according to the flow rate and pressure requirements of the heating system. A properly sized pump ensures that the thermal oil is circulated at an optimal rate, allowing for efficient heat transfer. It also helps prevent the thermal oil from overheating due to stagnation. Additionally, some advanced pump systems may have variable – speed drives, which can adjust the pump speed based on the heating demand, further improving the energy efficiency of the system.
Heat Exchangers
Heat exchangers are the interface where the heat from the thermal oil is transferred to the target medium. There are different types of heat exchangers used in thermal oil heating systems, such as shell – and – tube heat exchangers, plate – type heat exchangers, and finned – tube heat exchangers. Shell – and – tube heat exchangers consist of a shell with a bundle of tubes inside. The thermal oil flows through the tubes, while the target medium flows around the tubes in the shell, allowing for heat transfer through the tube walls. Plate – type heat exchangers use a series of thin metal plates to transfer heat, offering high heat – transfer efficiency in a compact design. Finned – tube heat exchangers are often used when the target medium is air, as the fins increase the surface area for better heat transfer to the air.
Control Systems
Modern thermal oil heaters are equipped with sophisticated control systems. These systems include temperature controllers, pressure gauges, flow meters, and safety devices. Temperature controllers, as mentioned earlier, monitor and regulate the temperature of the thermal oil. Pressure gauges are used to monitor the pressure within the heating system to ensure safe operation and prevent overpressure. Flow meters measure the flow rate of the thermal oil to ensure that it is circulating at the required rate. Safety devices, such as pressure relief valves, high – temperature cut – off switches, and low – flow alarms, are essential for protecting the system and preventing accidents. In case of abnormal conditions, these safety devices can automatically shut down the heater or take other corrective actions.
Types of Thermal Oil Heaters
Electric Thermal Oil Heaters
Advantages: Electric thermal oil heaters offer several advantages. They are relatively easy to install and operate, as they only require an electrical connection. They provide precise temperature control, which is crucial for many industrial processes. Since there is no combustion involved, they produce no emissions at the point of use, making them environmentally friendly and suitable for indoor applications. They also have a fast response time, allowing for quick heating up and adjustment of the temperature.
Disadvantages: However, their operation depends entirely on the availability of electricity. In areas with high electricity costs, the operating expenses can be relatively high. Additionally, the heating capacity of electric thermal oil heaters may be limited compared to large – scale fuel – fired heaters, which can be a drawback for some high – heat – demand industrial processes.
Fuel – Fired Thermal Oil Heaters
Advantages: Fuel – fired thermal oil heaters can provide high heating capacities, making them suitable for large – scale industrial applications. They can use a variety of fuels, including natural gas, diesel, and biomass, offering flexibility in fuel choice. In some cases, when the cost of the fuel is relatively low, the operating cost of fuel – fired heaters can be more economical compared to electric heaters. They can also be used in areas where electricity supply is limited or unreliable.
Disadvantages: On the downside, fuel – fired heaters require a proper fuel supply and storage system, as well as a flue gas exhaust system. The combustion process produces emissions, including carbon dioxide, nitrogen oxides, and particulate matter, which need to be managed to meet environmental regulations. Regular maintenance is also required to ensure efficient combustion and prevent issues such as soot buildup in the combustion chamber and heat – transfer surfaces.
Waste – Heat – Recovery Thermal Oil Heaters
Advantages: Waste – heat – recovery thermal oil heaters are designed to utilize waste heat generated from other industrial processes, such as exhaust gases from boilers, furnaces, or engines. By recovering this otherwise wasted heat, these heaters can significantly improve the overall energy efficiency of the industrial facility. They reduce the need for additional energy sources, thereby lowering energy costs and environmental impact. This type of heater is particularly beneficial in industries where a significant amount of waste heat is available.
Disadvantages: The operation of waste – heat – recovery thermal oil heaters depends on the availability and quality of the waste – heat source. The temperature and flow rate of the waste heat may vary, which can affect the performance of the heater. Additionally, the design and installation of these heaters can be more complex compared to traditional electric or fuel – fired heaters, as they need to be integrated with the existing waste – heat – generating processes.
Applications of Thermal Oil Heaters
Chemical Industry
Reactor Heating: In the chemical industry, thermal oil heaters are widely used to heat reactors. Many chemical reactions require specific temperature conditions to proceed efficiently and safely. Thermal oil heaters can provide a stable and precise heat source, ensuring that the reactors are maintained at the desired temperature. For example, in the production of polymers, the reactors need to be heated to specific temperatures to initiate and control the polymerization process. The high – temperature – resistant and stable – heat – transfer properties of thermal oil make it an ideal medium for this application.
Distillation and Evaporation: Thermal oil is also used in distillation and evaporation processes in chemical plants. In distillation columns, the thermal oil heats the mixture to be separated, causing the components with different boiling points to vaporize at different rates. In evaporation units, the heat from the thermal oil is used to remove the solvent from a solution, concentrating the remaining solute. The ability of thermal oil to operate at high temperatures without boiling allows for efficient separation and concentration in these processes.
Food and Beverage Industry
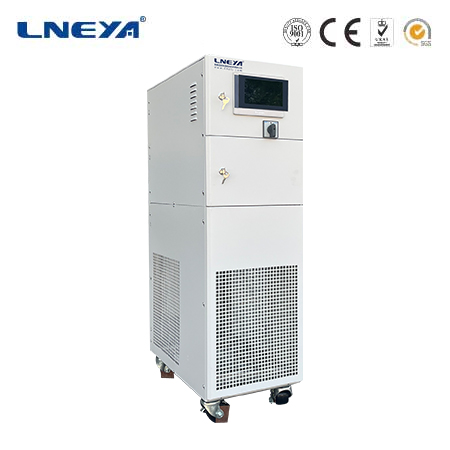
Baking and Cooking: In the food and beverage industry, thermal oil heaters are used for baking, cooking, and frying processes. They provide a consistent and even heat source, which is essential for achieving high – quality food products. For example, in large – scale bakeries, thermal oil – heated ovens can ensure that bread, cakes, and pastries are baked evenly, resulting in a better texture and taste. In commercial kitchens, thermal oil fryers can maintain a stable temperature, reducing the absorption of oil by the food and improving its nutritional value.
Food Processing and Preservation: Thermal oil is also used in various food – processing operations, such as pasteurization, sterilization, and drying. In pasteurization and sterilization, the heat from the thermal oil is used to kill harmful microorganisms in food products, ensuring their safety and extending their shelf life. In drying processes, the thermal oil heats the air or the food directly, removing moisture and preserving the food.
Textile Industry
Dyeing and Printing: In the textile industry, thermal oil heaters play a crucial role in dyeing and printing processes. Dyeing requires precise temperature control to ensure that the dyes are absorbed evenly by the fabric, resulting in a consistent color. Thermal oil heaters can provide the required heat with high accuracy, enabling the dyeing process to be carried out efficiently. In textile printing, the thermal oil is used to heat the printing paste, making it more fluid and ensuring better transfer onto the fabric.
Finishing Processes: Thermal oil is also used in textile finishing processes, such as drying, calendering, and heat – setting. Drying processes remove moisture from the fabric after washing or dyeing, and the heat from the thermal oil helps speed up the drying process. Calendering uses heated rollers to smooth and compress the fabric, and thermal oil is used to heat these rollers. Heat – setting is used to give the fabric a permanent shape, and the precise temperature control provided by thermal oil heaters is essential for this process.
Pharmaceutical Industry
Pharmaceutical Manufacturing: In the pharmaceutical industry, thermal oil heaters are used in various manufacturing processes, such as the synthesis of active pharmaceutical ingredients (APIs), drying of powders, and sterilization of equipment. The precise temperature control required in pharmaceutical manufacturing is crucial for ensuring the quality and efficacy of the drugs. Thermal oil heaters can provide a stable heat source, allowing for accurate control of the reaction temperatures during API synthesis. In drying processes, the thermal oil – heated dryers can remove moisture from the pharmaceutical powders without causing degradation of the active ingredients.
Laboratory Applications: Thermal oil heaters are also commonly used in pharmaceutical laboratories for heating reaction vessels, distillation equipment, and other laboratory apparatus. The ability to maintain a constant and precise temperature is essential for conducting accurate experiments and obtaining reliable results in pharmaceutical research and development.
Selection Criteria for Thermal Oil Heaters
Heating Capacity
Calculation: Determining the appropriate heating capacity of a thermal oil heater is essential. The heating capacity is usually measured in kilowatts (kW) or British Thermal Units per hour (BTU/h). To calculate the required heating capacity, factors such as the heat load of the process, the flow rate of the thermal oil, and the temperature difference between the inlet and outlet of the heater need to be considered. The heat load of the process is the amount of heat required to maintain the desired temperature of the target medium. The formula
Q=mcΔT
(where
Q
is the heat energy,
m
is the mass of the fluid,
c
is the specific heat capacity of the fluid, and
ΔT
is the temperature change) can be used to estimate the heat load. Once the heat load is determined, the appropriate heating capacity of the heater can be selected, adding a safety factor to account for any unexpected heat losses or variations in the process.
Future Expansion: Industries should also consider future growth and expansion when choosing a thermal oil heater. If there is a possibility of adding more processes or increasing the scale of the existing processes that require heating, selecting a heater with a slightly higher heating capacity than the current needs can save the cost and hassle of replacing the heater in the future.
Temperature Range
Process Requirements: Different industrial processes have specific temperature requirements. Some processes may only need low – to – medium – temperature heating, while others, such as certain chemical reactions or heat – treatment processes, require high – temperature operation. It’s crucial to choose a thermal oil heater that can provide the required temperature range for the specific application. For example, if a process requires heating up to 300°C, the selected heater should be capable of operating stably within this temperature range.
Temperature Stability: In addition to the temperature range, the stability of the temperature during operation is also important. Fluctuations in temperature can affect the quality of the products or the efficiency of the processes. Look for thermal oil heaters with advanced control systems that can maintain the temperature within a narrow tolerance band, ensuring consistent and reliable operation.
Fuel or Energy Source
Availability and Cost: The choice of fuel or energy source for the thermal oil heater depends on the availability and cost in the area. In regions where natural gas is readily available and cost – effective, a natural gas – fired heater may be a good option. If electricity is the most convenient and economical energy source, an electric thermal oil heater can be considered. For industries with access to waste heat, a waste – heat – recovery heater can offer significant cost savings and environmental benefits.
Environmental Impact: Environmental considerations are also important when selecting the energy source. Fuel – fired heaters produce emissions, and industries need to ensure that the emissions meet the local environmental regulations. Electric heaters, on the other hand, produce no emissions at the point of use, making them a more environmentally friendly choice in terms of local air quality.
Safety Features
Over – Temperature Protection: Over – temperature protection is a critical safety feature in thermal oil heaters. This feature monitors the temperature of the thermal oil and shuts off the heater or takes other corrective actions if the temperature exceeds a pre – set limit. Over – temperature protection helps prevent damage to the heater, the process equipment, and potential safety hazards, such as the degradation of the thermal oil or the ignition of flammable materials.
Pressure Relief and Safety Valves: Thermal oil heating systems operate under pressure, and pressure relief and safety valves are essential to prevent overpressure. These valves automatically open if the pressure within the system exceeds a safe level, releasing the excess pressure and protecting the system from damage. Regular inspection and maintenance of these valves are necessary to ensure their proper functioning.
Leak Detection and Alarm Systems: Since thermal oil can be flammable and harmful if it leaks, leak – detection and alarm systems are important safety features. These systems can detect any leaks of thermal oil in the system and trigger an alarm, allowing for prompt action to be taken to prevent accidents and environmental contamination.
Maintenance Requirements
Accessibility of Components: Choose a thermal oil heater with components that are easily accessible for inspection, cleaning, and maintenance. This includes the heating elements, pumps, heat exchangers, and control systems. Easy access to components can reduce the time and effort required for maintenance, as well as the cost of maintenance.
Availability of Spare Parts: Consider the availability of spare parts for the heater. In case of a breakdown or the need for component replacement, having readily available spare parts can minimize downtime. Choose a heater from a manufacturer with a good reputation for providing reliable spare – part support.
Maintenance Schedule: Different thermal oil heaters have different maintenance requirements. Some may require more frequent maintenance, such as regular filter changes, oil analysis, and component inspections, while others may have longer maintenance intervals. Understanding the maintenance schedule and associated costs is important for budgeting and ensuring the long – term reliable operation of the heater.
Related recommendations
water cooled chiller system
284Water-Cooled Chiller Systems: Efficiency and Versatility in Cooling Solutions Introduction to Water-Cooled Chiller Systems Water-cooled chiller systems are a type of industrial cooling solut...
View detailschilled glycol
147Chilled Glycol: Definition and Applications Chilled glycol refers to a coolant mixture used in industrial process cooling systems, typically consisting of glycol and water. Glycol, an organic c...
View detailshot water oil heating system
77Hot Water Oil Heating System: A Comprehensive ExplanationA hot water oil heating system is a heating mechanism designed to transfer heat from hot water to oil, which is then used to provide therma...
View detailsexternal chiller
272Closed-Cycle Cooling Water System: Precision Temperature Control for Diverse Applications A closed-cycle cooling water system, often referred to as a recirculating water bath chiller, is an ess...
View details
HelloPlease log in