water cooled liquid chiller
Water Cooled Liquid Chiller: Detailed Explanation
- Introduction to Water Cooled Liquid Chillers
Water cooled liquid chillers are refrigeration machines designed to cool water or water-glycol mixtures for process cooling or air conditioning applications. Unlike air-cooled chillers that reject heat to the atmosphere, water-cooled models transfer heat to a water stream that is typically cooled in a cooling tower.
These systems are preferred when:
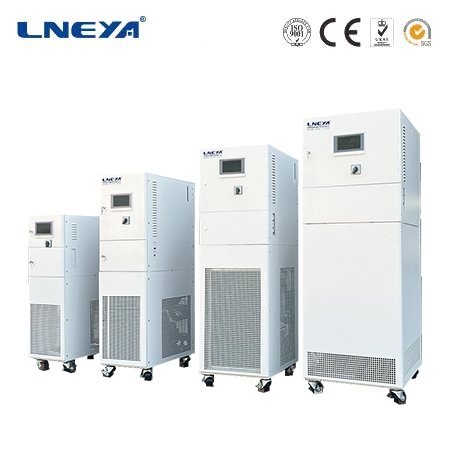
Energy efficiency is a priority
Space constraints exist
Ambient temperatures are consistently high
Noise reduction is important
- System Components and Configuration
A. Major Components
Compressor
Reciprocating, scroll, screw, or centrifugal types
Increases refrigerant pressure and temperature
Water-Cooled Condenser
Shell-and-tube or plate heat exchanger design
Transfers refrigerant heat to cooling water
Evaporator
Cools the process fluid (water or glycol)
Typically shell-and-tube or plate design
Expansion Device
Thermostatic or electronic expansion valve
Controls refrigerant flow into evaporator
Control System
Manages operation parameters
Modern units feature advanced microprocessor controls
B. Auxiliary Systems
Cooling tower (open or closed circuit)
Water pumps and piping
Water treatment system
Flow regulation valves
- How Water Cooled Chillers Work
The refrigeration cycle consists of four main processes:
Evaporation
Process fluid (water/glycol) enters evaporator at 6-12°C
Refrigerant absorbs heat and evaporates
Chilled fluid exits at desired temperature (typically 4-7°C)
Compression
Low-pressure refrigerant vapor is compressed
Temperature rises to 70-90°C
Pressure increases to 10-20 bar
Condensation
Hot refrigerant enters water-cooled condenser
Cooling water (27-32°C) absorbs heat
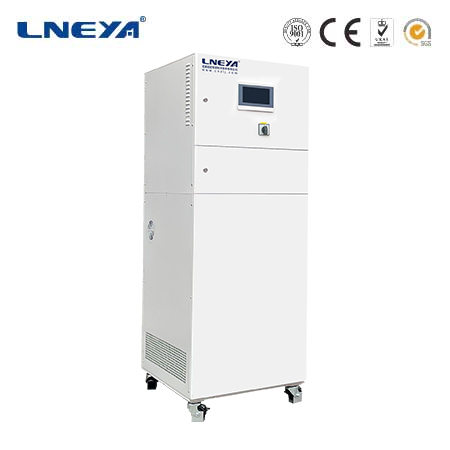
Refrigerant condenses to liquid
Expansion
High-pressure liquid passes through expansion device
Pressure and temperature drop sharply
Cycle repeats continuously
- Types of Water Cooled Chillers
A. By Compressor Technology
Centrifugal Chillers
For large capacity applications (200+ tons)
Highest efficiency at full load
Variable speed options available
Screw Chillers
Medium to large capacities (50-500 tons)
Good part-load performance
Robust design for industrial use
Scroll Chillers
Small to medium capacities (5-150 tons)
Simple and reliable
Common in commercial applications
Reciprocating Chillers
Small capacities (<100 tons)
Being phased out for more efficient options
B. By Configuration
Package Chillers
All components in one skid
Easy installation
Limited to smaller capacities
Modular Chillers
Multiple smaller units in parallel
Redundancy and scalability
Better part-load efficiency
Custom-Built Chillers
Designed for specific applications
Unique capacity or fluid requirements
Longer lead times
- Performance Characteristics
A. Efficiency Metrics
COP (Coefficient of Performance): 4.0-7.0 (higher is better)
kW/ton Rating: 0.5-0.7 kW/ton for efficient models
IPLV (Integrated Part Load Value): Measures part-load efficiency
B. Capacity Range
Small units: 5-50 tons
Medium units: 50-300 tons
Large units: 300-2000+ tons
C. Temperature Capabilities
Standard chilled water: 6.7°C supply
Medium temperature: 0°C to 5°C
Low temperature: -40°C to 0°C (special designs)
- Applications
A. Industrial Processes
Plastic injection molding
Laser cutting and welding
Chemical processing
Food and beverage production
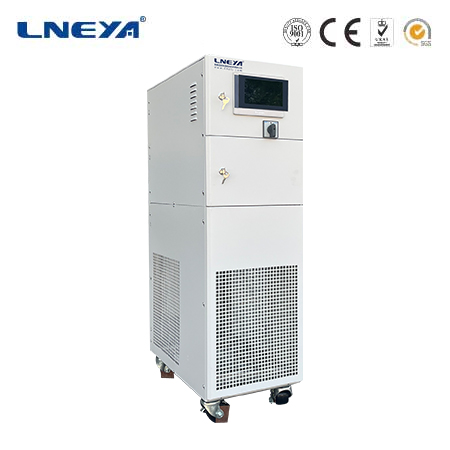
B. Commercial HVAC
Large office buildings
Hospitals and healthcare facilities
Hotels and resorts
Shopping malls
C. Specialized Applications
Data center cooling
MRI machine cooling
Pharmaceutical manufacturing
Semiconductor production
- Advantages Over Air-Cooled Chillers
Energy Efficiency
Lower condensing temperatures
Reduced compressor work
Typically 15-30% more efficient
Longer Lifespan
More stable operating conditions
Less thermal stress on components
Typical life expectancy of 20-25 years
Space Savings
No large condenser fans needed
Can be installed indoors
Smaller footprint per ton of cooling
Performance Stability
Less affected by ambient temperature
More consistent cooling capacity
Better performance in high temperatures
- Installation Considerations
A. Space Requirements
Mechanical room specifications
Access for maintenance
Vibration isolation needs
B. Water System Design
Cooling tower selection
Pipe sizing and insulation
Water treatment system
C. Electrical Requirements
Power supply specifications
Starter and control wiring
Emergency power options
D. Environmental Factors
Water availability and quality
Local regulations on water use
Discharge temperature limits
- Maintenance Requirements
A. Daily/Weekly Checks
Water pressure and temperature
Refrigerant pressures
Unusual noises or vibrations
B. Monthly Maintenance
Water treatment analysis
Strainer cleaning
Control system verification
C. Annual Service
Condenser and evaporator cleaning
Refrigerant charge check
Electrical component testing
Lubrication of moving parts
D. Water Treatment
Scale and corrosion inhibition
Biological growth prevention
Filtration requirements
- Economic Considerations
A. Initial Costs
Higher than air-cooled chillers
Additional cooling tower expense
Installation complexity
B. Operating Costs
Lower energy consumption
Water treatment expenses
Maintenance labor costs
C. Lifecycle Costs
Typically lower than air-cooled
Longer equipment life
Better ROI for high-usage applications
- Environmental Impact
A. Energy Efficiency
Reduced power plant emissions
Lower carbon footprint
B. Refrigerant Issues
Global warming potential
Phase-out schedules
Leak prevention
C. Water Usage
Consumption in cooling towers
Treatment chemical disposal
Water conservation strategies
- Recent Technological Advances
A. Variable Speed Operation
Compressor speed modulation
Pump speed control
Improved part-load efficiency
B. Magnetic Bearing Compressors
Oil-free operation
Reduced maintenance
Higher efficiency
C. Advanced Controls
Predictive maintenance
Remote monitoring
AI-driven optimization
D. Alternative Refrigerants
Low-GWP options
Natural refrigerants (ammonia, CO2)
Blends for specific applications
- Selection Criteria
When choosing a water cooled chiller, consider:
Cooling capacity requirements
Temperature range needed
Available water quality and quantity
Space constraints
Energy efficiency goals
Maintenance capabilities
Budget parameters
Future expansion plans
- Common Problems and Solutions
A. Scaling and Fouling
Regular cleaning schedules
Proper water treatment
Automatic tube brushing systems
B. Refrigerant Leaks
Regular leak testing
Proper installation practices
Quick repair protocols
C. Reduced Efficiency
Regular performance monitoring
Timely maintenance
Component upgrades when needed
D. Water Treatment Issues
Continuous monitoring
Professional water treatment services
Proper chemical dosing
- Future Trends
A. Smart Chiller Systems
IoT connectivity
Cloud-based analytics
Automated performance optimization
B. Improved Materials
Advanced heat exchanger coatings
Corrosion-resistant alloys
Composite components
C. Energy Recovery
Waste heat utilization
Combined heating/cooling systems
Integration with renewable energy
D. Sustainable Practices
Zero water discharge systems
Rainwater harvesting
Green certification standards
Conclusion
Water cooled liquid chillers represent a highly efficient solution for demanding cooling applications across various industries. Their superior performance characteristics, especially in terms of energy efficiency and operational stability, make them the preferred choice for many large-scale cooling requirements. While they require careful water management and have higher initial costs than air-cooled alternatives, their long-term operational benefits often justify the investment. Proper system design, regular maintenance, and attention to water treatment are essential for achieving optimal performance and longevity. As cooling technologies continue to evolve, water cooled chillers are expected to incorporate more smart features and sustainable practices while maintaining their position as workhorses of industrial and commercial cooling.
Related recommendations
process heater manufacturers
87Process Heater Manufacturers Process heaters are essential equipment in many industrial sectors as they are used to heat fluids, gases, or other materials to specific temperatures required for ...
View detailschiller 4 kw
156When considering the purchase of a 4 kW chiller, it's essential to understand the various factors that influence its price and performance. This article delves into the world of 4 kW chillers, exa...
View detailssmall chiller plant
279Small Chiller Plant: Selection and Efficiency A small chiller plant is an essential component of heating, ventilation, and air conditioning (HVAC) systems, particularly where precise temperatur...
View detailscooler cool
195Enhancing Cooling Efficiency: The Concept of "Cooler Cool" Introduction to "Cooler Cool"The phrase "cooler cool" encapsulates the idea of making cooling systems more effective. Whether it's kee...
View details
HelloPlease log in