water to water chiller
Introduction
Water to water chillers are sophisticated systems designed to transfer heat from one water source (the warm water) to another (the cool water), thereby reducing the temperature of the warm water. These chillers play a crucial role in a wide range of industrial, commercial, and even some residential applications. They are essential for maintaining optimal temperatures in processes or equipment that generate heat, ensuring efficient operation and product quality. Understanding the working principle, types, applications, advantages, and maintenance of water to water chillers is fundamental for their proper utilization.
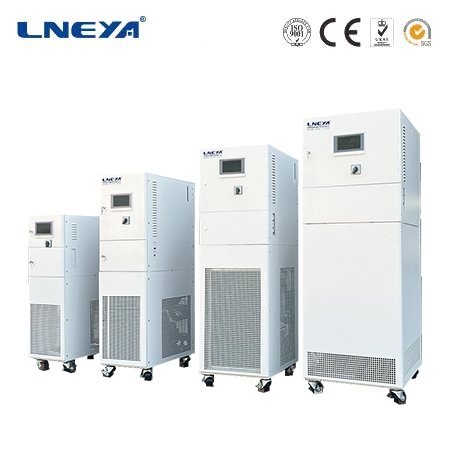
Working Principle
Refrigeration Cycle Basics
Water to water chillers operate based on the vapor – compression refrigeration cycle, which is a well – established method for heat transfer. This cycle involves four main components: an evaporator, a compressor, a condenser, and an expansion valve.
Evaporation: In the evaporator, a low – boiling – point refrigerant circulates. Warm water from the source that needs to be cooled passes over the evaporator coils. Heat from the warm water is transferred to the refrigerant, causing the refrigerant to change from a liquid state to a vapor state. As the refrigerant absorbs heat, it cools the warm water. For example, in an industrial process where a large amount of heat is generated, the warm water flowing through the evaporator section of the water to water chiller loses heat to the refrigerant, resulting in a decrease in its temperature.
Compression: The low – pressure refrigerant vapor then enters the compressor. The compressor’s function is to increase the pressure and temperature of the refrigerant vapor. By compressing the vapor, work is done on it, raising its internal energy and temperature. This high – pressure, high – temperature vapor is now ready for the next stage of the cycle.
Condensation: The high – pressure, high – temperature refrigerant vapor flows into the condenser. Here, the refrigerant releases heat to the cool water stream. The cool water can be sourced from a cooling tower, a nearby water body, or a closed – loop water – cooling system. As the refrigerant loses heat, it condenses back into a liquid state.
Expansion: The high – pressure liquid refrigerant passes through an expansion valve. The expansion valve reduces the pressure of the refrigerant, causing it to expand rapidly. This sudden expansion leads to a drop in the refrigerant’s temperature, and it re – enters the evaporator as a cold, low – pressure liquid to start the cycle anew.
Heat Exchanger Function
Heat exchangers are key components in water to water chillers. They facilitate the transfer of heat between the warm water, the refrigerant, and the cool water.
Evaporator Heat Exchanger: The evaporator heat exchanger is designed to maximize the heat transfer from the warm water to the refrigerant. It usually consists of a series of tubes or plates. The warm water flows on one side of the heat exchanger, while the refrigerant flows on the other side. The large surface area of the heat exchanger and the close proximity of the two fluids (warm water and refrigerant) allow for efficient heat transfer.
Condenser Heat Exchanger: The condenser heat exchanger serves the opposite purpose. It enables the transfer of heat from the high – pressure, high – temperature refrigerant vapor to the cool water. Similar to the evaporator heat exchanger, it has a design that maximizes heat transfer, such as a shell – and – tube or plate – type configuration. The cool water absorbs the heat from the refrigerant, causing the refrigerant to condense.
Types of Water to Water Chillers
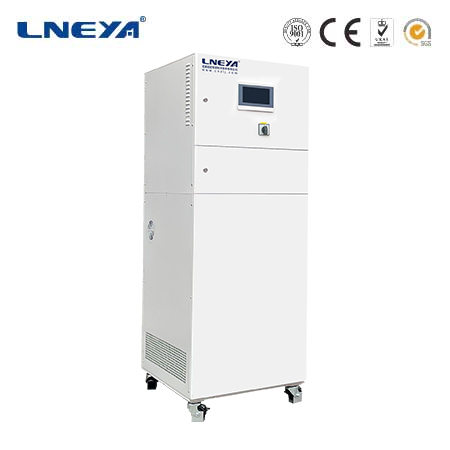
Air – Cooled Water to Water Chillers
Operation and Design: Air – cooled water to water chillers use ambient air to cool the refrigerant in the condenser. The condenser coils are exposed to the air, and fans are used to blow air over the coils to enhance heat dissipation. These chillers are often self – contained units and can be relatively compact. They are suitable for applications where access to a water source for cooling is limited. For example, in a small – scale industrial workshop or a commercial building with no dedicated water – cooling infrastructure, an air – cooled water to water chiller can be installed easily.
Advantages: They are simple to install as they only require access to ambient air and an electrical connection. They are also more flexible in terms of location, as they do not depend on a water supply. Air – cooled chillers are generally less expensive to install compared to water – cooled ones, as there is no need for complex water – piping systems.
Disadvantages: They are less energy – efficient compared to water – cooled chillers, especially in high – temperature environments. The performance of air – cooled chillers can be significantly affected by the ambient air temperature. In hot weather, the condenser may struggle to reject heat effectively, reducing the overall cooling capacity.
Water – Cooled Water to Water Chillers
Operation and Design: Water – cooled water to water chillers use a water source, such as a cooling tower or a closed – loop water – cooling system, to cool the refrigerant in the condenser. The condenser heat exchanger transfers heat from the refrigerant to the cool water. These chillers are often used in large – scale industrial and commercial applications where a reliable water source is available. For instance, in a power plant or a large manufacturing facility, water – cooled water to water chillers are commonly employed.
Advantages: They are more energy – efficient than air – cooled chillers, as water has a higher heat – carrying capacity than air. This allows for more effective heat dissipation, resulting in better overall performance. Water – cooled chillers are also less affected by high ambient temperatures, as the water used for cooling can be maintained at a relatively stable temperature.
Disadvantages: They require a reliable water supply and proper water treatment to prevent scale and corrosion in the condenser heat exchanger. Installation costs can be higher due to the need for plumbing infrastructure to supply and manage the water.
Applications
Power Generation
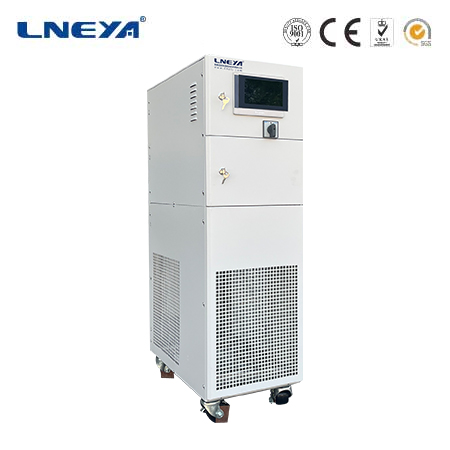
Thermal Power Plants: In coal – fired, natural – gas – fired, and nuclear power plants, water to water chillers are essential for cooling various components. After steam passes through turbines to generate electricity, it needs to be condensed back into water. Water to water chillers are used to remove heat from the steam in the condenser, ensuring the efficient operation of the power – generation cycle. For example, in a large – scale coal – fired power plant, water to water chillers can be used to cool the condenser, reducing the temperature of the steam and converting it back into water for reuse in the boiler.
Hydroelectric Power Plants: Although hydroelectric power plants rely on the energy of flowing or falling water to generate electricity, water to water chillers may still be used to cool the generators and other electrical equipment. The cool water helps in maintaining the optimal operating temperature of the equipment, preventing overheating and ensuring reliable power generation.
Manufacturing
Plastic Manufacturing: In plastic injection molding and extrusion processes, water to water chillers are used to cool the molds and the extruded plastic products. Precise temperature control is crucial in plastic manufacturing to ensure dimensional accuracy and product quality. Uneven cooling can lead to warping, cracking, and other defects in plastic parts. Water to water chillers help in maintaining a consistent cooling rate, resulting in high – quality plastic products.
Metalworking: In metal – cutting and machining operations, coolants (which are often water – based) are used to remove heat generated by friction. Water to water chillers can be used to cool these water – based coolants. By keeping the coolant at the right temperature, it improves the performance of the cutting tools and the surface finish of the machined parts. In a metal – working factory, a water to water chiller can be used to cool the coolant used in a high – speed milling operation, extending the tool life and improving the quality of the machined components.
Data Centers
Server Cooling: Data centers house a large number of servers and other electronic equipment that generate a significant amount of heat. Water to water chillers are increasingly being used to cool the water that circulates through the server racks. Warm water that has absorbed heat from the servers is cooled by the water to water chiller and then recirculated. This helps in maintaining a low and stable temperature in the data center, preventing server failures and ensuring the reliable operation of the data center.
Energy Efficiency: Water to water chillers in data centers offer better energy efficiency compared to some other cooling methods. Since water has a high heat – carrying capacity, it can remove more heat with less energy consumption. This is crucial for data centers, which consume a large amount of electricity, as it helps in reducing overall energy costs.
Advantages of Water to Water Chillers
High – Efficiency Heat Transfer
Efficient Heat Exchange: Water to water chillers are designed to achieve high – efficiency heat transfer between the warm water, the refrigerant, and the cool water. The use of advanced heat exchanger designs, such as plate – type or shell – and – tube heat exchangers, allows for a large surface area for heat transfer. This results in a more effective transfer of heat, reducing the temperature of the warm water more quickly and efficiently compared to some other cooling methods.
Optimal Temperature Control: These chillers can provide precise temperature control. The refrigeration cycle can be adjusted to maintain the desired temperature of the cooled water within a narrow range. In applications where precise temperature control is crucial, such as in pharmaceutical manufacturing or precision manufacturing processes, water to water chillers can ensure that the temperature remains stable, leading to better product quality.
Energy – Efficient Operation
Lower Energy Consumption: Water to water chillers, especially water – cooled ones, generally consume less energy compared to some other cooling methods. The high – efficiency heat transfer allows for a more energy – efficient operation, as less energy is required to transfer the same amount of heat. In a closed – loop water – cooled system, the energy required to cool the water can be optimized, reducing the overall energy consumption of the cooling process.
Waste Heat Recovery: In some applications, water to water chillers can be integrated with waste – heat recovery systems. The warm water that has absorbed heat can be used for other purposes, such as heating buildings or pre – heating water for industrial processes. This further improves the overall energy efficiency of the system, as it makes use of the otherwise wasted heat.
Maintenance
Refrigerant Checks
Proper Refrigerant Charge: The refrigerant charge in a water to water chiller is crucial for its proper operation. An improper refrigerant charge can lead to reduced cooling capacity, increased energy consumption, and potential damage to the compressor. Regular checks should be carried out to ensure that the refrigerant level is correct. If the refrigerant level is too low, it may indicate a leak in the system, which needs to be repaired promptly.
Refrigerant Quality: The quality of the refrigerant should also be monitored. Over time, the refrigerant may become contaminated with moisture, non – condensable gases, or other impurities. Contaminated refrigerant can affect the performance of the chiller and may cause corrosion in the system. Periodic testing of the refrigerant quality and, if necessary, refrigerant replacement or purification should be done.
Heat Exchanger Cleaning
Evaporator and Condenser Heat Exchangers: The evaporator and condenser heat exchangers of a water to water chiller need to be cleaned regularly. Dust, dirt, and debris can accumulate on the heat exchanger surfaces, reducing the heat – transfer efficiency. In the case of water – cooled condensers, scale and algae can also build up if the water is not properly treated. Cleaning the heat exchangers can be done using a variety of methods, such as mechanical cleaning with brushes, chemical cleaning with specialized cleaners, or a combination of both.
Frequency of Cleaning: The frequency of heat exchanger cleaning depends on the operating environment and the type of water used. In a dusty or polluted environment, the heat exchangers may need to be cleaned more frequently. Similarly, if the water used in the chiller contains a high amount of minerals or impurities, more frequent cleaning may be required to prevent scale and corrosion.
Component Inspection
Compressor and Expansion Valve: The compressor and expansion valve are critical components of the water to water chiller. The compressor should be inspected regularly for signs of wear, leaks, or abnormal noise. The expansion valve should also be checked to ensure that it is operating correctly and regulating the refrigerant flow as designed. Any malfunction in these components can affect the performance of the chiller and may lead to costly repairs.
Pumps and Fans: In water to water chillers, pumps are used to circulate the water, and fans (in air – cooled chillers) are used to dissipate heat. These components should be inspected regularly for proper operation. The pumps should be checked for leaks, and the fans should be checked for balanced operation and proper airflow. Regular lubrication of moving parts in pumps and fans is also important to ensure smooth operation and extend their lifespan.
Conclusion
Water to water chillers are essential devices in many industries and applications, providing efficient and reliable cooling solutions. Their ability to transfer heat effectively, combined with their energy – efficient operation and precise temperature control, makes them an attractive option for various heat – management needs. However, proper maintenance, including refrigerant checks, heat exchanger cleaning, and component inspection, is crucial to ensure the long – term reliable operation of these chillers. By understanding the working principle, types, applications, advantages, and maintenance requirements of water to water chillers, users can make informed decisions about their implementation and management.
Related recommendations
chiller cycling
7Introduction Chiller cycling is an important aspect of the operation of chiller systems. It involves the repeated starting and stopping of the chiller unit in response to various factors withi...
View detailspropylene glycol for chiller
243Propylene Glycol for Chiller Systems: An In-Depth Analysis Understanding Propylene Glycol in Chillers Propylene glycol is a popular fluid used in chiller systems, particularly for its effect...
View detailsprocess water heater
174Understanding Process Water Heaters Process water heaters are essential in many industrial settings, where they provide heated water for a variety of applications. These applications can range ...
View detailsuse of chiller
296Introduction to the Use of Chillers Chillers are essential cooling systems that transfer heat from one medium to another, providing cooling for a variety of applications. They are used in heati...
View details
HelloPlease log in